Your cart is currently empty!
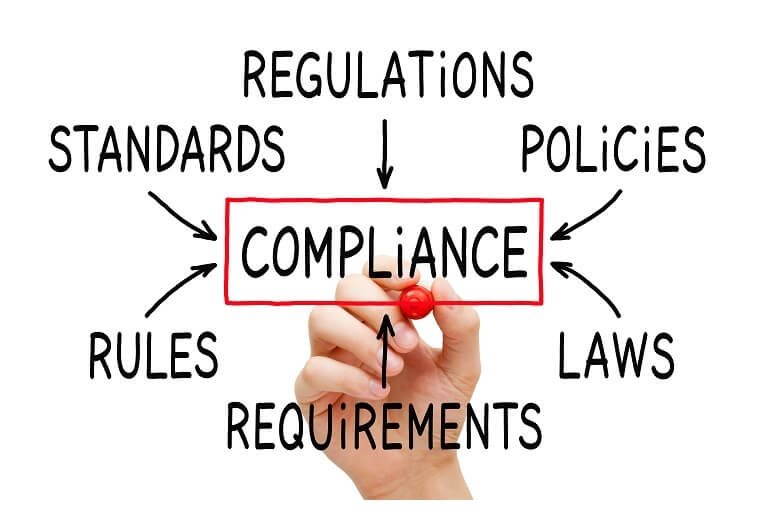
WHO INSPECTION & REQUIRED DOCUMENTS
WHO INSPECTION & REQUIRED DOCUMENTS
Objectives of a manufacturing site inspection
The overall intent of a manufacturing site inspection is to assess the safety, performance, and quality of the Manufacturing site. The specific objectives are to assess compliance of the manufacturer’s quality management system (QMS) and manufacturing practices with international standards in order to:
- Determine the effectiveness of the implemented QMS in meeting appropriate quality standards
- Verify the data supporting the claims presented in the submitted product dossier (and also those in the pre-submission form)
- Inspect the QMS according to the manufacturer’s own requirements.
The objective of the inspection influences the inspector’s planning, organization, method of work, and the format of the report that will be written after the inspection. Different types of inspections can be performed depending on the objective of the inspection.
Types of inspections identified in the WHO text include
- Routine inspection
- Concise inspection
- Follow-up inspection
- Special inspection
- Quality systems review.
Routine inspection
A routine inspection is a full review of all aspects and components of GMP within a facility. The inspector should also be aware of the licensing provision. Routine inspections may be announced or unannounced, depending on the history of the company, previous inspections, and the policy of the country.
It is appropriate to perform a routine inspection under the following circumstances:
- When there is an application for a new manufacturing license for a newly established manufacturer
- When a manufacturing license is due for renewal.If there have been significant changes such as new products or new product lines,
- Modification to manufacturing methods or processes, or changes in key personnel, premises, and or equipment.
- If the company has a history of non-compliance with GMP.If an inspection has not been carried out within the past 3–5 years.
Routine inspection
A concise inspection is the evaluation of limited aspects relating to GMP compliance within a facility. A limited number of GMP requirements are selected by the inspector to serve as indicators of overall GMP compliance by the manufacturer. The inspector also has to identify and evaluate any significant changes that could have been introduced by the manufacturer since the last inspection. Collectively, the selected indicators and identified changes indicate the manufacturer’s attitude towards GMP. Depending on the national practice, a company would normally not be warned in advance about a concise inspection.
A concise inspection is applicable under the following circumstances:
- Where a manufacturer has a consistent record of GMP compliance through routine inspections in the past.
- Where a sample of aspects can be taken as a good indication of the overall level of GMP compliance.
if the concise inspection uncovers evidence that the level of GMP compliance has fallen, a more comprehensive or full GMP inspection should then be performed soon after the concise inspection.
Follow-up inspection
A follow-up inspection is also referred to as a re-inspection or a re-assessment of the manufacturer. A follow-up inspection is performed specifically to monitor the result of the corrective actions of the manufacturer following a previous inspection. The manufacturer would not necessarily know in advance about the follow-up inspection. Depending on the nature of the defects and the work required, the follow-up inspection could be carried out between 6 weeks and 6 months after the original inspection had taken place. The inspection is limited to specific GMP requirements that have not been observed or that have been inadequately implemented by the manufacturer.
Special inspection
There are a number of circumstances in which special visits or inspections may be necessary. A special inspection is undertaken to do spot checks. Spot checks could focus on one product, a group of related products, or specific operations e.g. mixing, or labeling.
The manufacturer may or may not be aware in advance of the inspection, depending on the reason for it.
If there have been complaints about a specific product that suggest there may be defects, then a special inspection could be performed to investigate the quality defects of the product. It is unlikely that the company would be warned in advance in this case.
- If there has been a product recall, this can also trigger an inspection, as would adverse drug reactions.
- The inspection would focus on the specific product or aspect of production that is suspect.
- An application for marketing authorization or an export certificate may also trigger such an inspection.
- A special inspection could also be performed to gather specific information or to investigate specific operations of the manufacturer.
- Opportunity is used to advise the manufacturer on specific regulatory requirements.
Quality systems review.
The purpose of a quality systems review is to review the manufacturer’s quality system and to describe whether that has been shown to operate satisfactorily. The quality systems manual is a document describing the quality systems and the standards to be observed. It also includes the entire operational process, the quality management policy, and the quality assurance approach of the manufacturer. The manual reflects the process of implementation of the quality policy, keeping records, quality control, and other quality assurance activities. This type of review is similar to that which is carried out when a manufacturer is applying for accreditation, e.g. international standards (ISO 9000).
Frequency of Inspections
- Depends on the type of inspection
- Inspectorate resources (e.g. workload, number of inspectors)
- New facilities – before licensed
- All companies – regular schedule – ideally annual
- large companies
- several visits over a period, e.g. 5 years
- validity of manufacturing license or GMP certificate
Duration of Inspections
The length of an inspection is determined by a number of factors, including the type of inspection to be performed, the number of inspectors, the size of the company, and the purpose of the inspection or visit. An inspection can be performed over a period of a few days to several weeks. The time taken will also depend on the size of the inspection team. One or more inspectors can perform the inspection and the inspector(s) may request a specialist to accompany them during the inspection. Depending upon the area or specific aspects to be inspected, a specialist could provide specialist support to the inspection team.
The duration of Inspections Depends on
- The type of inspection
- Inspectorate resources (e.g. workload, the number of inspectors)
- Size of the company
- Purpose of the visit
- Days to weeks
- Number of inspectors including specialist support
Documents required for CD Submission to WHO
S.No. | Documents Name |
1 | Application for grant of COPPs |
2 | Name of the applicant with address |
3 | Copy of Manufacturing License |
4 | List of approved products for COPPs |
5 | List of products applied for issuance of COPPs & their composition |
6 | Site master file |
7 | Stability study evaluation |
8 | Process validation Report |
9 | Analytical method validation |
10 | List of technical staff, their qualification, experience and approval status |
11 | List of equipment and instrument |
12 | List of SOPs and STPs |
13 | Manufacturing Plant layout |
14 | Schematic diagram of the water system |
15 | Schematic diagram of HVAC system |
16 | Product summary sheet |
17 | List of Reference standards |
18 | Certificates of Analysis for three batches of each product |
DOCUMENT MANAGEMENT
S No. | DOCUMENT NAME | Numbers |
1 | Site Master File | |
2 | Quality Manual | |
3 | Quality Policy | |
4 | Validation Master Plan | |
6 | Process Simulation Study | |
7 | Approved Vendor List (RM) | |
8 | Approved Vendor List (PM) | |
9 | Medical Examination Records | All employee |
10 | Appointment letters of key personnel | All key personnel |
11 | Manufacturing presentation | |
12 | Outside testing agreement | |
13 | Equipment preventive maintenance schedule/report | |
14 | SOPs Warehouse | |
15 | SOPs Engineering | |
16 | SOPs HR | |
17 | Internal Audit Report | Report -I Report -II |
18 | Training records | |
19 | Quality Assurance | Calendar – Training Log – Training Records |
20 | Quality Control | Calendar – Training Log – Training Records |
21 | Microbiology lab | Calendar – Training Log – Training Records |
22 | Production (Injection) | Calendar – Training Log – Training Records |
23 | Production (Dry Syrup & Capsule) | Calendar – Training Log – Training Records |
24 | Warehouse | Calendar – Training Log – Training Records |
25 | Engineering | Calendar – Training Log – Training Records |
26 | HR | Calendar – Training Log – Training Records |
27 | Organization Chart of Plant | |
28 | Organogram of Quality Assurance | |
29 | Organogram of Quality Control | |
30 | Organogram of Microbiology lab | |
31 | Organogram of Production (Injection) | |
32 | Organogram of Production (Dry Syrup & Capsule) | |
33 | Organogram of Warehouse | |
34 | Organogram of Engineering | |
35 | Organogram of HR | |
36 | Vendor Qualification | – |
37 | Annual product quality review | For all the products that will be applied for WHO |
38 | Process validation protocol / report | |
39 | Hold time study | |
40 | Stability data record | |
41 | Cleaning validation | |
42 | Master formula record | |
43 | Product development record | |
44 | Analytical method validation | |
45 | Bulk product specification | |
46 | Semi-finished product specification | |
47 | Finished product specification |
AREA QUALIFICATION
S No. | AREA QUALIFICATION |
1. | Room Data sheet |
2. | General Plant layout |
3. | Pressure zoning layout (Floor wise) |
4. | Equipment Placing Layout |
5. | Man Movement layout (Floor wise) |
6. | Material Movements Layout (Floor wise) |
7. | Environment Monitoring plate location Layout |
8. | Area Layout with drain Point |
9. | AHU GA Drawing |
10 | AHU Ducting layout |
EQUIPMENT QUALIFICATION (INJECTION) – URS/DQ/FAT/SAT/IQ/OQ/PQ
SNo. | Equipment’s |
1. | Dispensing Booth |
2. | Vial Washing Machine -I |
3. | Tunnel |
4. | Filling Machine |
5. | Sealing Machine |
6. | Bung Processor |
7. | Optical Inspection Machine |
8. | Vial Washing Machine – II |
9. | Labelling Machine |
10 | Mobile LAF |
11. | LAF |
12 | Pass Box |
13. | Garment Cubicle |
14 | Filter Integrity Tester |
15 | LBPC |
EQUIPMENT QUALIFICATION (DRY SYRUP & CAPSULE) – URS/DQ/FAT/SAT/IQ/OQ/PQ
SNo. | Equipment’s |
1. | Dispensing Booth |
2. | Bottle Washing Machine |
3. | Vibro Sifter |
4. | Multi- Mill |
5. | Filling & Capping Machine |
6. | Induction Sealing Machine |
7. | Labeling Machine |
8. | Fluidized Bed Drier |
9. | Blender |
10 | Capsule filling Machine |
11. | Capsule Sorting Machine |
12 | Blister Packing Machine |
13. | Optical Inspection Machine |
UTILITY QUALIFICATION – URS/DQ/FAT/SAT/IQ/OQ/PQ
SNo. | Equipment’s |
1. | Water System Validation (Two Phase complete – third phase ongoing) |
2. | WFI Validation- all three Phase (Two Phase complete – third phase ongoing) |
3. | Pure Stem Qualification |
4. | Compressed air Qualification |
5. | Nitrogen Plant validation |
6. | AHU Qualification |
7. | Temperature Mapping of Storage area |
8. | Passivation Report of water System |
9. | Slop Certificate of pipework |
10 | Certificate of MOC |
OTHER DOCUMENTATION
S No. | DOCUMENTATION NAME |
1 | Pest Control records |
2 | Contract Agreement of Pest Control |
3 | Contract Agreement of Waste material Disposal |
4 | Fire Fighting Training Record |
5 | Pre-filter and return filter washing and cleaning records of AHU |
6 | AHU – Operation, Cleaning, and Maintenance log |
7 | Preventive Maintenance program |
8 | Calibration program |
9 | Cleaning records of the area |
10 | Cleaning records of Equipment |
11 | Job Responsibility of Key Personnel |