Your cart is currently empty!
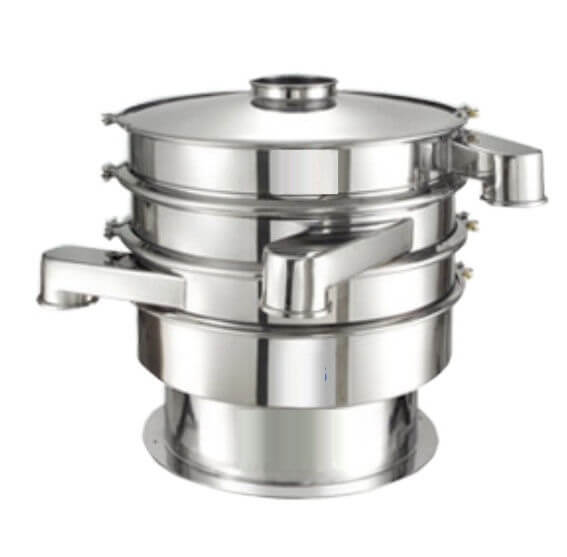
Vibro Sifter and It working principle
Vibro Sifter and It working principle
The Vibro Sifter works on the principle of gyratory vibrations. The material is separated based on its particle size. Once the motor gets energized, vibration is caused in the screen/sieve making the material travel across the sieves according to its particle size.
Highly effective for screening, scalping, de-dusting, and filtering your raw material, the machine is ideal for screening a wide range of materials, like wet, dry, coarse, fine, hot, or cold materials.
Circular motion helps the screening material to evenly distribute across the screen mesh. With the material spread evenly, you can utilize the screen to its optimum utility. This will evidently make your screening process faster and reduce your time consumption.
In three different planes, the development of vibration along the vertical axis utilizing a specially designed vibratory motor that meets various output requirements. It causes 100% rotary motion and causes dispersion stirring & amp; stratification of material to sift. Feed material flows in Horizontal movement along with a loop pattern on Vibroscreen.
Pneumatic sieving
For materials that need to be pneumatically conveyed, Compact Airswept Sieve which allows materials to be conveyed pneumatically from one location to the next within a production line. It is a popular choice within the food and pharmaceutical industries due to it being a completely enclosed operation, protecting the product and the operators.
Magnetic separator
Specifically designed to remove ferrous contamination, a magnetic separator with our vibro sifters. The magnetic separator is constructed from high-grade stainless steel.
Working Principle
The Vibro Sifter works on the ‘Gyratory Motion’ principle. and The mixture is placed in the center of the screen and then travels along a spiral path to the periphery while the fine particles pass through it. consequently, the material being screened is applied mathematically apart and no follow-up is exerted to separate the grosser particles. The sieving is done gently and with very little abrasion.
With the help of eccentric weights that are mounted on the upper and lower ends of the motion generator shaft of the machine, Vibro Sifter achieves the staggering high-intensity vibrations that it is famous for. The dual weights allow the machine to move in a circular motion, as the lower weights aim to tilt the machine to generate vertical vibrations and the top weights move to distribute the materials across the screen.
The vibro sifter machine is widely known as Vibro Sifter, Vibro Screen, Vibrating Screen, Lab Vibro Sifter, Pharmaceutical Sifter, Vibro Sieve, Vibro Sifter Machine, and Powder Sieving Machine.
Salient Features :
- Use For Gradation & Separation Of Dry Powder, Granules, And Semi Solids / Liquids.
- The sieves are suspended on a spring to avoid vibration on the floor.
- Easy Dismantling & Cleaning.
- Ball tray arrangement. (For choking of sieves).
- Rubber molded sieve.
Procedure for Operation & Cleaning of Vibro Sifter
Ensure that the equipment and the area are cleaned and released by the Quality Assurance department for processing.
Remove the ‘CLEANED’ label and Affix the “Equipment Status” label over the machine.
Check the tare weight of the In-process container along with the double poly bag inside and record the same on the container status label.
Check the integrity of the sieves for any type of damage, by looking at them and affixing them to the machine.
Place the In-process container underneath the discharge chute of the Sifter.
Switch ‘ON’ the main power supply.
Feed the material to be sifted into the hopper, with the help of a scoop. Collect the sifted material in the In-process container and also transfer the loosely stuck material from the machine by using a scrubber in the In-process container.
Once the in-process container is filled remove the in-process container and close the inner poly bag with a cable tie.
After completion of the sifting Switch ‘OFF’ the machine by pressing the ‘RED’ Button.
Record the process details in the “Equipment Sequential Logbook”.
Remove the “Equipment Status” label and affix the ‘TO BE CLEANED’ label on the machine.
CLEANING :
Type A Cleaning:
Cleaning Activity:
Check and ensure that all the production activity is completed.
Switch “OFF” disconnect the electrical power supply and cover the electrical panel with a poly bag.
Remove the “EQUIPMENT STATUS” label and affix the “TO BE CLEANED” label over the equipment.
Remove the loosely adhered powder from the machine using a dry lint-free duster, collect it in a poly bag, and affix the “NON-RECOVERABLE REJECTION” label.
Check and ensure the availability of the following accessories for cleaning:
- Nylon brush.
- Nylon Scrubber/ duster.
- Clean lint-free duster.
- Clean LDPE bags
Procedure For Dismantle Of Vibro Sifter Parts:
Unlock the upper clamps of the sifter assembly.
Remove the upper lid, and gasket and place them on the pallet.
Unlock the middle clamps of assembly and remove the deck and sieve of sifter and place it on pallet & transfer it to the washing area.
Check the integrity of the sieve by visually inspecting it.
Unlock the lower clamps and remove the charging port and gasket.
Remove the loosely adhered powders to the inner and outer surface of the equipment using lint free duster and collect the waste material in a poly bag and destroy it.
Procedure for Cleaning Of Dismantled Parts:
Wash all the dismantled parts one by one using a lint-free cloth with running potable water.
Remove the adhered powder which is not easily removable, using a nylon brush/duster/ scrubber, and final cleaning with purified water.
Clean the upper lid, clamps, deck, charging, and discharging port using a lint-free cloth followed by potable water till visually clean and final cleaning with purified water.
Clean the sieve gently using nylon brush if required and wash it using a sufficient quantity of purified water.
Visually check the cleaning, If cleaning is not satisfactory then repeat the cleaning procedure till visually clean.
Dry the cleaned dismantled part by using Dry lint-free cloth/compressed air.
Visually check the integrity of the sieve for any damage or torn after cleaning. Transfer the dry & clean dismantle part to the clean room.
Cleaning Procedure For Non dismantle part of Equipment:
Remove the “TO BE CLEANED” label from the equipment.
Wipe the total surface of the equipment using a lint-free cloth/duster.
Wipe the equipment with a wet lint-free duster/cloth dipped in purified water followed by dry lint-free cloth till visually clean.
Visually inspect the cleanliness of the equipment surface and other parts to ensure all previous
product traces are removed and cleaned properly.
Reassemble of Dismantle Parts:
- Assemble all the cleaned and dried dismantled parts one by one using proper tooling.
- Fix the charging port on the machine and tighten it with gaskets and clamps.
- Place the deck on the charging port and tighten it with gaskets and clamps.
- Place the upper lid on the deck and tighten it with gaskets and clamps.
- Ensure that all the assembled parts have been tightened properly.
- Cover all openings using poly bag/stretch wrapping.
- After completion of the cleaning, record the cleaning details in the “Equipment Sequential Logbook ”.
- After the verification of cleanliness by the production personnel, affix dully filled ‘CLEANED’the status label on the equipment.
Validity of “Type-A cleaning: After completion of five consecutive batches or completion of 108 Hrs. whichever is earlier.
Type B Cleaning:
Check and ensure the area activity is completed before starting the cleaning.
Switch “OFF” and Isolate the electrical power supply.
Remove the “EQUIPMENT STATUS” label and affix the “TO BE CLEANED” label on the equipment.
Remove the upper lid by opening the clamps and gaskets and cleaning using a dry lint-free duster.
Remove the deck and sieves by opening the clamps and gaskets and cleaning using a dry lint-free duster.
Clean the inner and outer surfaces of the charging port using a dry lint-free duster.
Ensure the visual cleanliness of the equipment.
After the verification of cleanliness by the production personnel, affix a dully filled ‘CLEANED’ status label on the equipment.
After completion of the cleaning, record the cleaning time in the “Equipment Sequential Logbook”.
Validity of “Type-B cleaning: After batch to batch change over for the same product having
the same strength, same color, and same flavor.
NOTE: Hold time for uncleaned Equipment shall be not more than 72 hours and for cleaning
Equipment the hold time shall be 5 days from the date of cleaning of that Equipment.
Do not proceed until QA releases the Equipment and area for further processes.