Your cart is currently empty!
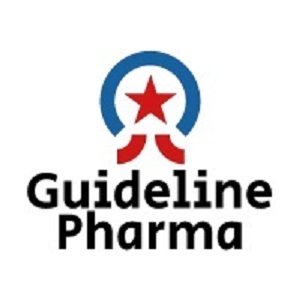
RESPONSIBILITY OF QUALITY ASSURANCE FUNCTIONS
RESPONSIBILITY OF QUALITY ASSURANCE FUNCTIONS:
Quality assurance can be defined as “part of quality management focused on providing confidence that quality requirements will be fulfilled.” The confidence provided by quality assurance is twofold—internally to management and externally to customers, government agencies, regulators, certifiers, and third parties. An alternate definition is “all the planned and systematic activities implemented within the quality system that can be demonstrated to provide confidence that a product or service will fulfill requirements for quality.”
- QUALITY ASSURANCE authority and responsibility of assessing and ensuring that all the products manufactured at site as per regulatory requirement.
- To monitor the entire manufacturing and quality control activities and to notify the management of any significant variation from the company standards which potentially affect the product quality.
- To ensure for each product there is an annual product quality review covering manufacturing activities, in order to provide assurance that product confirms to customers and regulatory requirements.
- To establish that manufacturing activities including any proposed changes are in accordance with regulatory requirement.
- Any changes which affect compliance with product standard should be approved by Head Quality Assurance before they are implemented.
- To review, suggest and ensure that plant is in validated state and confirms to regulatory requirements.
- Responsible for ensure the compliance of cGMP practices at all stages of production and control.
- Review of master documents and its control
- Review of production records and in process controls.
- Review of product specifications and test procedures.
- Responsible for Release/Reject of Finished Goods.
- Quality audits and quality manual
- Review of Stability studies
- Vendor Qualifications
- Training program
- Deviation and failure investigation
- Change control management
- Product complaints and recall
- Validations and Qualifications
- Calibration program
- Returned goods and their disposal
- Monitoring of Plant preventive maintenance
a pharmaceutical company api pharma api pharmaceutical company audit in pharmaceutical industry best pharmaceutical companies best pharmaceutical sales companies to work for big pharmaceutical companies biggest pharma companies in the world biggest pharmaceutical companies biggest pharmaceutical companies in the world biggest pharmaceutical companies in usa biopharma companies capa in pharma capa in pharmaceutical industry challenges in pharmaceutical industry change control in pharma clean room in pharmaceutical industry clean room requirements for pharmaceuticals cleaning validation in pharmaceutical industry cleaning validation protocol template current good manufacturing practices data analytics in pharmaceutical industry define pharmaceutical distribution of pharmaceutical products drug companies drug manufacturers drug manufacturing companies drug manufacturing process drug manufacturing process pdf drug packaging drug product manufacturing drugs company drugs manufacturing environmental monitoring in pharma environmental monitoring in pharmaceutical industry european pharma companies european pharmaceutical manufacturer fda guidelines for pharmaceutical industry formulation in pharma french pharmaceutical companies gmp certification gmp compliance gmp facility gmp guidelines for pharmaceuticals gmp manufacturing gmp pharmaceutical gmp pharmaceutical manufacturing gmp practices gmp production gmp rules in pharmaceutical industry gmp sop gmp validation gross to net pharma guidelines for stability testing of pharmaceutical products india pharma it in pharmaceutical industry largest pharma companies largest pharma companies in the world largest pharmaceutical companies largest pharmaceutical companies in the us largest pharmaceutical company in the world list of pharmaceutical companies list of pharmaceutical companies in usa list of quality control tests in pharmaceutical industry major pharmaceutical companies manufacturing companies manufacturing of pharmaceutical products manufacturing process in pharmaceutical industry marketing in pharmaceutical industry medical packaging companies medical pharmaceutical medical pharmaceutical companies medicine industry medicine manufacturing medicine manufacturing company medicine packaging method validation in pharma near me pharma company new product planning pharma opportunities in pharmaceutical industry packaging in pharmaceutical industry packaging of medicines packaging of pharmaceutical products packaging process in pharmaceutical industry pharma pharma analytics pharma audit pharma clean room pharma companies pharma companies in india pharma companies in uk pharma company pharma company near me pharma compliance pharma data pharma data analytics pharma data analytics companies pharma definition pharma development pharma distribution pharma distribution company pharma equipment pharma equipment manufacturers pharma excipients pharma factory pharma industry analysis pharma industry in india pharma industry jobs pharma industry overview pharma manufacture pharma manufacturing pharma manufacturing process pharma manufacturing software pharma market research pharma marketing pharma marketing agency pharma marketing company pharma near me pharma news pharma packaging pharma packaging companies pharma production pharma quality assurance jobs pharma regulatory pharma software pharma software companies pharma solution pharma solutions pharma supply chain pharma supply chain management pharma tech pharma testing Pharmaceutical pharmaceutical analysis pharmaceutical analytics pharmaceutical and medicine manufacturing pharmaceutical business pharmaceutical business plan pharmaceutical clean room pharmaceutical clean room definition pharmaceutical companies pharmaceutical companies in india pharmaceutical companies in usa pharmaceutical companies near me pharmaceutical containers pharmaceutical courses online pharmaceutical development pharmaceutical distribution pharmaceutical distribution companies pharmaceutical distribution system pharmaceutical engineering pharmaceutical environmental monitoring pharmaceutical equipment pharmaceutical equipment list pdf pharmaceutical equipment manufacturers pharmaceutical excipients pharmaceutical factory pharmaceutical formulation pharmaceutical formulation development Pharmaceutical Industry pharmaceutical industry analysis pharmaceutical industry companies pharmaceutical industry in india pharmaceutical industry jobs pharmaceutical industry overview pharmaceutical industry report pharmaceutical management pharmaceutical manufacturers in india pharmaceutical manufacturing pharmaceutical manufacturing companies pharmaceutical manufacturing equipment list pharmaceutical manufacturing industry pharmaceutical manufacturing pdf pharmaceutical manufacturing plant pharmaceutical manufacturing software pharmaceutical market pharmaceutical market analysis pharmaceutical market research pharmaceutical market size pharmaceutical marketing pharmaceutical marketing agency pharmaceutical marketing companies pharmaceutical marketing examples pharmaceutical marketing examples pharma manufacture pharmaceutical marketing plan pharmaceutical marketing research pharmaceutical packaging pharmaceutical packaging companies pharmaceutical packaging equipment market pharmaceutical packaging materials pharmaceutical packaging requirements pharmaceutical preparation manufacturing pharmaceutical process pharmaceutical process development pharmaceutical process validation pharmaceutical products pharmaceutical project manager pharmaceutical quality assurance pharmaceutical quality assurance pdf pharmaceutical quality control pharmaceutical quality management system pharmaceutical quality system pharmaceutical raw material pharmaceutical regulations pharmaceutical research companies pharmaceutical sales training pharmaceutical sampling guidelines pharmaceutical software pharmaceutical software companies pharmaceutical solutions pharmaceutical stability testing pharmaceutical storage pharmaceutical suppliers pharmaceutical supply chain pharmaceutical supply chain management pharmaceutical technology pharmaceutical testing pharmaceutical training pharmaceutical warehouse pharmaceutical warehouse requirements pharmaceutical water system pharmaceutical work pharmacy industry process development in pharmaceutical industry process validation sop product development in pharmaceutical industry product manager pharma project management in pharmaceutical industry qms in pharma qms in pharmaceutical industry QUALITY ASSURANCE QUALITY ASSURANCE FUNCTIONS quality assurance in pharmaceutical industry quality assurance in pharmacy quality assurance pharma quality assurance sop pdf quality control in pharmaceutical industry quality control pharma quality control tests in pharmaceutical industry pdf quality management in pharmaceutical industry quality management system in pharma quality management system in pharmaceutical industry pdf raw material testing in pharmaceuticals regulatory compliance in pharmaceutical industry regulatory guidelines for pharmaceuticals research and development in pharmaceutical industry research and development in pharmaceutical industry ppt RESPONSIBILITY OF QUALITY ASSURANCE FUNCTIONS risk management in pharmaceutical industry role of qa in pharmaceutical industry role of quality assurance in pharmaceutical industry ppt roles in pharmaceutical industry sampling in pharmaceutical industry secondary packaging pharmaceuticals sop for quality control sop in pharmaceutical industry sop in quality assurance sop list sop pharmacy sop quality sop store sops in pharmacy stability conditions in pharma stability studies of pharmaceuticals stability testing of pharmaceutical products sterile manufacturing sterility test in pharmaceutical industry sterility testing of pharmaceutical products sterility testing of pharmaceutical products pdf supply chain in pharmaceutical industry supply chain management in pharmaceutical industry tech transfer pharma technology transfer in pharma technology transfer in pharmaceutical industry technology transfer in pharmaceutical industry pdf the pharmaceutical industry top 10 biopharma companies top 10 pharma companies top 10 pharma companies in world top 10 pharmaceutical companies top 10 pharmaceutical companies 2022 top 10 pharmaceutical companies in usa top 10 pharmaceutical companies in world 2022 top 5 pharmaceutical companies top biopharma companies top pharma companies top pharma companies in usa top pharmaceutical companies top pharmaceutical companies in usa top pharmaceutical manufacturing countries in the world types of validation in pharmaceutical industry us pharmaceutical industry validation in pharmaceutical industry pdf validation in pharmaceutical industry ppt working in pharmaceutical industry