Your cart is currently empty!
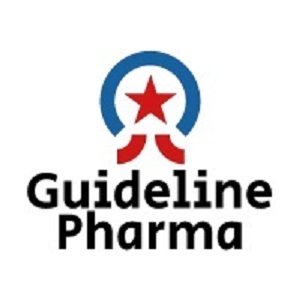
Product Quality Review
Product Quality Review
OBJECTIVE:
To lay down the Procedure for preparation of Product Quality Review.
PROCEDURE :
Product Quality Review (PQR) is a mechanism to ensure that data captured by the Pharmaceutical Quality System (PQS) is reviewed for trends. This tool can support a continuous improvement environment. PQRs are designed for the purpose of identifying and implementing recommendations for required improvements
Content of PQR
Summary of Product Quality Review
A brief summary of the PQR should be made for the batches manufactured in the current year even if only one batch was manufactured.
Batches manufactured
A review and number of all batches manufactured including failed batches/rejections during the review period for a specific product should be listed in the PQR. Gaps in batch numbering, e.g. due to validation lots pending approval or orders being canceled before any production commenced, should be explained in detail.
Raw materials from new sources (e.g. API, excipients, and packaging materials)
Raw materials (e.g. API, excipients, and packaging materials) should be listed if purchased from a new source for the manufacturing of the product concerned.
Analytical results (Critical in-process control results & critical analytical test results of finished products)
The comparison of the particularly applicable specifications and initial analysis results of all or of a representative number of batches that were produced during the defined review time frame should be included. These data should include all the critical quality parameters for a specific product and are to be reviewed.
Quality parameters examples for drug products are:
Critical In-process control result
Critical In-process control results should be collected from the Batch manufacturing record and Batch packing record during the following stages of manufacturing as applicable.
Granulation:
LOD, Blend Assay, and Yield at different stages of manufacturing of the product..
Compression/Encapsulation:
Average weight, Uniformity of weight, Hardness, Thickness, Disintegration Time, Friability, Dissolution ( if applicable ), Assay & Yield of compressed tablets or filled capsules.
Coating:
Average weight, Thickness, Disintegration Time, Dissolution, Assay, and Yield of coated tablets.
Liquid Orals
- pH
- Density
- Related Substances
- Assay (Active, Preservatives)
- Microbial Counts (Total Bacterial; Total Fungal, Pathogens)
- Batch yield
Critical analytical test results of the finished product
Critical analytical test results of the finished product should be collected from the Certificate of Quality as per product specification. This data may include as applicable.
Description, Average weight, Uniformity of weight, , Hardness, Thickness, Disintegration Time,Friability, and Dissolution of finished products.
- Assay
- Impurities (HPLC & GC)
- Content uniformity
- Microbial results
- Other critical parameters.
Deviations and Out of Specification:
A review of all investigations related to deviations and OOS should be performed including a review of the adequacy of previous corrective actions.
Change controls (Change of specifications and process revisions):
All change controls raised should be listed in the PQR. This list should include details of changes made in of specifications, manufacturing, and/or packing process revisions.
Review of any changes to the equipment used during manufacturing and packing of the product.
All information regarding the change of any equipment that was used during the manufacturing or packaging process of the particular product should be included in the PQR.
Stability review:
A summary of stability data of all batches on stability (follow-up stability program), which represents the manufactured batches for distribution. These data should be reviewed and compared with data from the previous year’s review to assure that no negative trend has developed and no stability failures occurred and that the expiry period is still appropriate.
Customer complaints
Any customer complaints received from the respective market during the time frame of the review should be listed in the PQR. The list should include the following details:
- Product Name & Batch Number.
- Nature of complaint
- Root cause.
- The conclusion made as a result of the investigation
Market Withdrawals, Recalls, and Regulatory Alerts
Any batches withdrawn or recalled, or regulatory alerts made from the respective markets during the time frame of the PQR should be listed along with the reason for the recall or withdrawal.
Returned / Salvaged drug products
A listing of any returned/salvaged drug products should be included. This should include the batch number and the reason for returning. If investigations were performed the result and the decision on the final use should also be listed.
Any returned products that are considered complaints should be evaluated as stated under the point of customer complaints.
Review of an annual visual examination of retained samples
Representative retention samples should be visually examined once a year.
Qualification status of relevant equipment and utilities (HVAC system, Water system, and Compressed air system)
Changes/ deviations to the qualification status of relevant equipment and utilities should be summarized.
Review of contractual arrangements
A review of contractual arrangements with contractors or suppliers should be included to confirm the agreements are up-to-date.
Trend analysis evaluation and graphical representation of analytical data
Statistical analysis should be performed to assess the batch uniformity and integrity of drug products. Since the process evaluation is performed, a graphical representation of parameters (i.e. Control and Acceptance criteria, etc.) will be useful to study the historical behavior patterns of the process and aid in the visual evaluation of out-of-specification values and/or trends that may translate into abnormal variations. Individual trends shall be analyzed and a conclusion shall be written.
Recommendations and conclusion
All data should be evaluated as a whole and these data should be summarized and recommendations for actions provided. The responsibility for coordination and supervision of follow-up measures is with the QA.
All batches manufactured in the calendar year or review period (January to December) should be included in the preparation of PQR.
All batches manufactured including rejected batches during the review period should be included in the PQR.
All PQRs should be conducted with the objective of verifying the consistency of process parameters and highlighting any trends.
The timeline for completion should not be longer than 3 months past the end of the calendar year.