Your cart is currently empty!
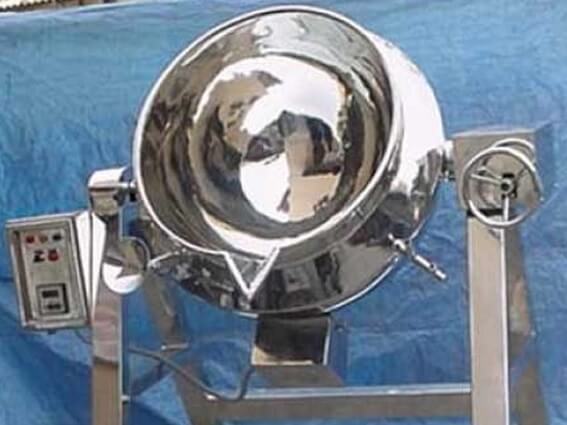
Paste Kettle
Paste Kettle
A paste Kettle (starch paste kettle) including a tilting paste kettle is designed for paste preparation. Starch Paste Kettle confirms cGMP norms and comprises a jacketed hemispherical bowl with all necessary steam accessories.
The design principle of this kettle is the jacket for passing steam in order to melt down the product to make a paste. This kettle has a unique tilting arrangement for discharging the product.
The tilting paste kettle is designed for ointment, cream,, and paste preparation. It has a universal application resulting in uniform melting. This tank is designed to meet the missing needs of a wider range of products under varied operating conditions in the chemicals, Foods, Cosmetics, and Pharmaceutical industries. Range of Jacketed paste kettle from 10 liters small paste kettle to 250 liters industrial paste kettle. Due to its application of working with starch, it is also called a starch melting machine or starch mixing machine.
Design of Paste Kettle
A hemispherical shape container ensures that the heating of the starch paste is uniform and covers more surface area. The tilting type arrangement ensures ease in unloading the paste in another container or vessel. The starch is put in the kettle and water is added to it till desired thickness of the paste is achieved. The kettle is jacketed and heated till the starch melts and a thick paste is achieved. This paste can be agitated either manually or with the help of an anchor-type agitator which will constantly agitate the paste so that there will be no lumps formation. Temperature can be set to the desired degree by adjusting the thermostat and the temperature can be seen in the dial thermometer.
Features of Paste Kettle
- GMP Model.
- All contact parts are made of Stainless Steel 316 materials.
- Hemispherical design for proper mixing paste.
- The jacket with steam/thermic fluid heating arrangement.
- The motor and gearbox assembly is mounted on the top side, so no hindrance to machine operation.
- A tilting arrangement for the kettle for discharge for starch paste.
- Insulation to the jacket in order to avoid heat loss.
- Anchor-type impeller design for proper mixing of paste.
- Bottom discharge with flush bottom ball valve hence no chance of residual paste.
- Mechanical tilting with hand wheel arrangement.
- Teflon scrappers for homogenous mixing of paste.
- The detachable agitator can be easy for cleaning and sterilization.
Operation Procedure:
Ensure that the equipment and the area are cleaned and released by the Quality Assurance department for processing. Affix the “Equipment Status” label over the machine.
Pour the required quantity of water into the vessel specified in the Batch record.
Switch ‘ON’ the machine by pressing the main switch to turn “ON’’ the heater by pressing the heater knob and setting the temperature according to the need. Follow the process details as per Batch Record.
Pour the prepared slurry of the starch (as mentioned in the Batch record) into the paste kettle through the inlet.
After completion of paste formation stops the heating by pressing the main switch and turn “OFF’’ the heater by pressing the heater knob.
Unload the slurry/paste by tilting it with the help of the rotator wheel.
Pour the purified cold water & leave the paste kettle for 30 minutes at room temperature for cooling.
Turn ‘OFF’ the display panel by pressing the panel knob.
Record the process details in the “Equipment Sequential Logbook”.
Remove the “Equipment Status” label and affix the “TO BE CLEANED” label on the machine.
Cleaning:
Type A Cleaning:
Cleaning Activity:
Check and ensure that all the production activity is completed.
Switch “OFF” and disconnected the electrical power supply and cover the electrical panel with a poly bag.
Remove the “EQUIPMENT STATUS” label and affix the “TO BE CLEANED” label over the equipment.
Remove the loosely adhered powder from the machine using a dry lint-free duster, collect it in a poly bag, and affix “NON-RECOVERABLE REJECTION”
Check and ensure the availability of the following accessories for cleaning:
- Nylon Brush.
- Nylon Scrubber/duster.
- Clean lint-free duster.
- Clean LDPE bags
Procedure For Dismantle Of Paste Kettle Parts:
- Unlock the upper clamps of the paste kettle assembly.
- Remove the upper lid.
- Remove the loosely adhered powders to the inner and outer surface of the equipment using a wet lint-free duster and collect the waste material in a poly bag and destroy it.
Procedure For Cleaning Of Dismantled Parts:
- Wash all the dismantled parts one by one using a lint-free cloth with running potable water.
- Remove the adhered powder which is not easily removable, using a nylon brush/duster/ scrubber.
- Finally, rinse all dismantled parts using a sufficient quantity of purified water. If cleaning is not satisfactory then repeat the cleaning procedure till visually clean.
- Dry all washed parts with lint-free cloth/compressed air and transfer to a clean room.
Cleaning Procedure For Non-Dismantle parts of Equipment:
- Remove the “TO BE CLEANED” label from the equipment.
- Remove the adhered powder which is not easily removable, using a nylon brush/duster/ scrubber.
- Clean the non-dismantled parts of the equipment with a wet lint-free duster/cloth dipped in purified water. Visually inspect the cleanliness of the equipment surface and other parts to ensure all previous product traces are removed. If cleaning is not satisfactory then repeat the cleaning procedure till visually clean.
- Dry all washed parts with lint-free cloth/Compressed air and transfer to a clean room.
Reassemble Of Dismantle Parts:
- Assemble all the cleaned and dried dismantled parts one by one using proper tooling.
- Fix the charging port on the machine.
- Place the upper lid on the deck and tighten it.
- Ensure that all the assembled parts have been tightened properly.
- After completion of the cleaning, record the cleaning details in the “Equipment Sequential Logbook”.
- After the verification of cleanliness by the production personnel, affix a dully filled ‘CLEANED’ status label on the equipment.
Validity of “Type-A cleaning”: After completion of five consecutive batches or completion of 108 Hrs. whichever is earlier.
Type B Cleaning:
- Check and ensure the area activity is completed before starting the cleaning.
- Switch “OFF” and disconnect the electrical power supply.
- Remove the “EQUIPMENT STATUS” label and affix the “TO BE CLEANED” label on the equipment.
- Remove the upper lid and clean using a dry lint-free duster.
- Clean the inner and outer surfaces of the charging port using a dry lint-free cloth.
- Remove the not easily removable materials using a nylon brush/duster/ scrubber.
- Ensure the cleanliness of the equipment.
- After the verification of cleanliness by the production personnel, affix dully filled ‘CLEANED’ the status label on the equipment.
- After completion of the cleaning, record the cleaning time in the “Equipment Sequential Logbook”.
Validity of “Type-B cleaning: After batch to batch change over for the same product having the same strength, same color, and same flavor.
NOTE: Hold time for uncleaned Equipment shall be not more than 72 hours and for cleaned equipment, the hold time shall be 5 days from the date of cleaning of that Equipment.