Your cart is currently empty!
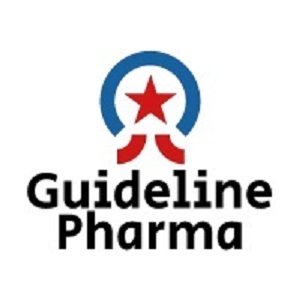
Interview Question & Answer Pharma QA
Interview Question & Answer Pharma QA
Process/activity | Reference Guideline/method |
Process validation | PV FDA JAN-2011 EMA 2012 Including(ICH Q8, Q10) |
Blend Uniformity & Content Uniformity (stratified sampling) | ISPE (December 2014) ASTME 2709/E2810 USP Chapter No: 905 |
Friability | USP chapter 1216 |
Disintegration | USP chapter 709 |
Hold Time Study | WHO Expert Committee on Specifications for Pharmaceutical Preparations: forty- ninth report. Geneva: World Health Organization; 2015: Annex 3 (WHO Technical Report Series, No. 992). |
Dissolution | USP chapter 711 |
Cleaning Validation | ICH Q3 C (R5) Health Canada –Draft Cleaning validation guideline (GUI0028) FDA guideline to inspections Validation of cleaning Process.(1993) PICS., APIC HSA JAN 2013 WHO Technical series 937, 2006 Annex 4, Appendix 3 |
AQL (Critical-0.010% & non-Critical-0.65%) | ISO 2859-1 General inspection level-iii British standard BS. 6001:1999-1 Level III |
PSD Test for QC | GTP no. – GTP/USP/016 |
BD Test for QC | GTP no. – GTP/USP/017,/028 |
Stability | ICH- Q1A R2 to Q1E |
MHRA/USFDA- PQR/APQR | EudraLex Volume 4 Health Science Authorities (HSA) PICS |
Transport Route Profiling & Qualification | WHO stand-TRS 961 annex 9 • Requalification: Change in route • Change in transport vendor • Change in transport conditions • Every five years (risk based suggestion) |
Quality Risk Management | ICH Q9 WHO Guidelines-TRS-981 ,Annexure-II |
ISPE :International society of Pharmaceutical Engineering
ASTME : American standards of testing and material
ICH :international council on harmonization
EMA :European medicinal agency
HSA :Health science Authority
SAP :System Application And Product in Data Processing(SAP R/3 4.7 Enterprise Edition is a software application used by companies around the world to run their businesses.)
SCM: : System Chain Management
RMG : Rapid Mixer Granulator
SMG : Saizoner mixer granulator
RLAF : Reverse Laminar Air Flow
LAF : Laminar Air Flow
VTS : Vacuum transfer system
HVAC : Heating, Ventilation and Air Conditioning
AHU : Air Handling Unit
HEPA : High Efficiency Particulate Air filter.
ULPA : Ultra-Low Penetration Air
VMP : Validation Master Plan
LOAEL : Lowest Observed Adverse Effect Level
NOEL : No Observable Effect Level
PDE : Permitted Daily Exposure
ADI : Acceptable Daily Intake
MAR: Maximum allowable residue
MACO : Maximum Allowable Carryover
PIC/S : Pharmaceutical Inspection Co-Operation Scheme
CTD : Common Technical Document
MSDS: Material Safety Data Sheet
BOPP: Biaxial Oriented Ploy Propylene
MPD : Master packing documents
CPV : Continues Process Validation
CPP : Critical Process Parameters
CQA : Critical Quality Attribute.
SUPAC : Scale –Up and Post approval changes
SUPAC IR : Immediate release
SUPAC MR : Modified release
Certification & Standards of ISO:-
ISO 9001:2015 – Quality Management System
ISO 14001: 2015 – Environment Management System:
ISO 45001:2018 – Occupational Health & Safety Management System
( International Council on Harmonization)
1989-WHO Conference of Drug Regulatory Authorities produced action plans for regulation of medical research
(US, JAPAN, Switzerland, Canada, Europe)
Q1 Stability | Q7 Good manufacturing practice (API) |
Q2 Analytical method validation | Q8 Pharmaceutical development |
Q3 Impurities | Q9 QRM |
Q4 Recommendation of pharmacopoeia | Q 10 Pharmaceutical Quality system |
Q5 Biotechnological products | Q11 Development and manufacture of drug substances |
Q6 specification test procedure and acceptance criateria | Q12 Life cycle management |
Q13 Continual Manufacturing |
TITLE 21–FOOD AND DRUGS CHAPTER I–FOOD AND DRUG ADMINISTRATION
DEPARTMENT OF HEALTH AND HUMAN SERVICES SUBCHAPTER C–DRUGS: GENERAL
PART 211 CURRENT GOOD MANUFACTURING PRACTICE FOR FINISHED PHARMACEUTICALS
Part-11 – Electronic records & signature Part-58 – Good laboratory practice (GLP) Part-210 -cGMP General
Part-211 -cGMP for finished product192 Batch Review (Investigations)
- 22(d) Responsibilities of QCU
- 110(a) In-Process Sampling/Testing
- 100(b) Adherence to Production Procedures
- 100(a) Production Procedures (Validation)
- 160(b) Laboratory Controls
- 165(a) Testing and Release
- 188 Batch Record Review
- 25(a) Personnel Qualifications
- 67(a) Equipment Cleaning and Maintenance
- 180 (e) APR
Requirements of APRs are found in 21 CFR 211.180 (e) and include:
- procedure
- Review Written of Every batch (or Representative) to determine the need for changes in specification or manufacturing or control procedures
- Review of complaints
- Review of recalls
- Review of returned and salvaged products
- Review of investigations
Subpart | Clause |
A. General provisions | – |
B. Personnel & Qualifications | 211.25 Personnel Qualifications. 211.28 Personnel responsibilities. |
C. Building & facilities | 211.42 Design and construction features. 211.44 Lighting. 211.46 Ventilation, air filtration, air heating and cooling. 211.48 Plumbing. 211.50 Sewage and refuse. 211.52 Washing and toilet facilities. 211.56 Sanitation. 211.58 Maintenance |
D. Equipment | 211.63 Equipment design, size, and location. 211.65 Equipment construction. 211.67 Equipment cleaning and maintenance. |
E. Drug product containers & closures | 211.80 General requirements. 211.82 Receipt and storage of untested components, drug product containers, and closures. 211.84 Testing and approval or rejection of components, drug product containers, and closures. 211.86 Use of approved components, drug product containers, and closures. 211.87 Retesting of approved components, drug product containers and closures. 211.89 Rejected components, drug product containers, and closures. 211.94 Drug product containers and closures. |
F. Production & process control | 211.100 Written procedures; deviations. 211.101 Charge-in of components. 211.103 Calculation of yield. 211.105 Equipment identification. 211.110 Sampling and testing of in-process materials and drug products. 211.111 Time limitations on production. 211.113 Control of microbiological contamination. 211.115 Reprocessing. |
G. Packaging & labeling control | 211.125 Labeling issuance. 211.130 Packaging and labeling operations. 211.134 Drug product inspection. 211.137 Expiration dating. |
H. Holding and Distribution | 211.142 Warehousing procedures. 211.150 Distribution procedures. |
I. Laboratory controls | 211.165 Testing and release for distribution. 211.166 Stability testing. 211.170 Reserve samples. |
J. Records & Reports | 211.180 General requirements. 211.182 Equipment cleaning and use log. 211.184 Component, drug product container, closure, and labeling records. 211.186 Master production and control records. 211.188 Batch production and control records. 211.192 Production record review. 211.194 Laboratory records. 211.196 Distribution records. |
K. Returns & Salvaged Drug products | 211.204 Returned drug products. 211.208 Drug product salvaging. |
Equipment | Step Of Calibration |
Analytical Balance
(Sartorius) | 1. Accuracy Test – 120.0000gm Capacity as per united state pharmacopeia. Theoretical weight A (gm.)/standard weight/tolerance 0.10%/observation. 10.0/20.0/50.0/100.0gm. 2. Repeatability test:- Theoretical weight 50.0gm/put 10 times once location/observation SD-………………. , D(least count)-0.0001gm/ repeatability :- 2XSD / (Theoretical weight)X100 Note: if the standard deviation obtained is smaller than 0.41d, where d is the scale interval ( i.e. least count), replace the standard deviation with 0.41d. in this calculate repeatability using following equation : 2X0.41d/ (Theoretical weight)X100 |
Friability (Electro lab) | 1. 04 Min./….Actual observation/ Tolerance limit 234-246Sec. 2. 25 Revolution-3times/ Actual observation/Tolerance limit 24- 26Rev./min. |
DT
(Electro lab) | 1. Temp. of water bath/Actual observation / Tolerance limit 37-39C 2. Temp. in beaker/ Actual observation L&R/ Tolerance limit 37±2C 3. No. of strokes/min./4times Actual observation L&R/ Limit 29-32 cycle./min. 4. Stroke heights/ Actual observation L&R/ Tolerance limit 55 ±2mm. 5. Baskets lower most position/ Actual observation L&R/ 25 mm. 6. Sieve Integrity/ Actual observation L&R/ 2.0mm ±0.2mm |
Hardness | |
Moisture Analysis (Mettler Toledo) | 1. 5.0 gm. talc powder/weight of water 0.200gm/%Moisture content /Acceptance Criteria=100 ±2% |
IP/BP TABLETS(Uncoated & Film coated) | Less than or equal 80 mg / 10% | More than 80mg to less than 250mg / 7.5% | More than or equal to 250mg / 5% |
(BP/USP)Capsules, Granules (Uncoated single dose) and Powder (Single dose) | Less than 300 mg (10 %) | 300 mg or more (7.5 %) | |
USP Tablets (Uncoated and Film Coated) | Less than or equal 130 mg / 10% | More than 130mg to less than 324mg / 7.5% | More than or equal to 324mg / 5% |
IP/BP Capsules | less than or equal to 300mg / 10% | More than 300mg / 7.5% | |
Capsules Shell (IP) | Moisture Content 12.5% (As per IP) / RH% 40-60%, Temp. 15-25 C |
Sr. No. | Types of air lock | Processing area | Air lock | corridor |
1 | Cascade | 15 pa. | 30 pa. | 45 pa. |
2 | Bubble | 15 pa. | 30 pa. | 15 pa. |
3 | Sink | 30 pa. | 15 pa. | 30 pa. |
Note- NLT-1.0 mm/hg , pa= Pascal
RLAF filters and its magnehlic gauge reading
- Pre-filter = 10microne- 2 to 8mm of WC
- Intermediate filter = 5 micron- 2 to 8mm of WC
- HEPA filter = 3 micron – 7 to 15mm of WC Where ,
as mm of WC = millimeter of water columns
- Impeller speed – Slow 60rpm/ fast 120rpm (As per Make and model)
- Chopper speed — Slow 1440rpm/ fast 2880rpm (As per Make and model)
- Ampere Load for end point determination — Low ampere reading- Less binding strength
High ampere reading- Strong binding strength (Impact on Dissolution)
- Torque Value for end point determination
- Banana breaking method for end point
Parameter:- Inlet temp., outlet temp., product temp., CFM
Challenge test:-SFM Challenge study (Broken bag detector test)
Metal detector test
Principle- Electromagnetic induction principle
Test piece- Tablet – Fe (0.3mm), NFE (0.3mm), SS (0.5mm), Plain Capsule – Fe (0.1mm), NFE (0.15mm), SS (0.20mm), Plain
AWC Principle – Compaction force principle
Main parameters- HCP, LCP, HEP, LEP, HSP, LSP, Reference value
Tablet compression machines are made in keeping in view the type of dies and punches will be used on them , The dies and punches and their setup on compression machine is called tooling , it is classified as B and D mainly .
The B tooling dies and punch can be further have specifications as BB and D tooling can also be dies and punches can be utilsed on B tooling machine which is called as DB
Mainly there are two standards, ad D and B , in US specification provided by Tableting Specification Manual (TSM )is followed where as in Europe European standard known as the EU, or “Euronorm” standard is.
There is not much difference in both the specifications but both are very different.
Difference between B and D tooling
Following is the key difference between D and B tooling for tablets compression
D tooling
Barrel Diameter is 1 inch
Head Diameter is 1 and ¼ th inch length is 5.25 inch Dies outer diameter is 0.945 and
BB Tolling
Barrel Diameter is 0.75 inch
Head Diameter is 1 inch length is 5.25 inch
Dies outer diameter is 30.16 mm
B tooling is same as BB only difference is that lower punch length is just 3 and 9/16th inch long.
D tooling dies and punches are usually have thick diameter or have greater diameter of their body as well as the tip of punches also dies have greater outer diameter compared to B type tolling which makes D type tolling dies and punches suitable for compression of big size
tablets as the tip of the pinches is border compared to B tooling dues and punches.
Many sub categories like DB, BB type tablets dies and punches are made depending up on the punches and dies requirement of product.
Following table will be useful in understanding the concept of tablet tooling and how they are classified as B and D tooling and BB and DB tooling.
Type Of Tooling | Punch Diameter. (in mm) | Die Diameter. (mm)/( inch) | Punch Length ( mm)/inch | Max. Tab. Size (mm) Round/Capsule |
‘B’ | 19 | 30.15 / 1.187 | 133.60 | 16/19 |
‘D’ | 25.4 | 38.1/1.50 | 133.60 | 25/25 |
‘BB’ | 19 | 24/0.945 | 133.60 | 13/14 |
‘DB’ | 25.4 | 30.15/1.187 | 133.60 | 19/19 |
Punch Set Life
Type of product | Punch set life |
Circular | 4 million tablets/set |
Other than circular | 2 million tablets/set |
Double layer | 2 million tablets/set |
Effervescent Tablet | 1 million tablets/set |
Height of the die
Type of tooling | Height of dies (mm) |
“D” Tooling | 23.82 ± 0.1 |
“B” Tooling | 22.22 ± 0.1 |
Outer diameter of dies
Type of tooling | Outer diameter of dies(mm) |
“D” Tooling | 38.10 ± 0.1 |
“B” Tooling | 30.16 ± 0.1 |
- Following definitions for direct terminology for tooling (Punches and dies).
- Head: The end of the punch that guides it through the cam track of tablet machine during
- Head flat(Dwell Flat): The flat area of the head that receives the compression force from rollers(in upper punches) and determines the weight and ejection height (in lower punches).
- Outside head Angle: The area gets in touch with the roller prior to head flat , while
- Inside Head Angle: This is the area, which pulls down the lower punches after ejection and lifts the upper punches after compression.
- Neck: The relived area between the head and barrel, which provides clearance for the
- Barrel: This area guides the punch (while going up and down) with reference to turret
- Stem: The area of the punch opposite the head, beginning at the tip and extending to the point
Where the full diameter of the barrel begins. If the chamfer is present the barrel usually reaches
Its full diameter just above the chamfer.
- Tip: This determines size, shape & profile of the
- Tip face: This area of punch is where the tablet is formed. Good surface finish is required here to bet quality tablets.
- Working length: This distance between bottom of the cup and the head flat is called as working
length which determines weight and thickness of the tablet.
- Overall length: Distance between top of the cup and the head
- Key Angle: The relationship of the punch key to the tablet shape. The keys position is Influenced by the tablet shape, take-off angle, and turret rotation.
- Domed Heads: Increases the dwell time and hence help to achieve the better tablet
- Dwell time – The time punches spends below the pressure roller while rotating in the
- Clearance:
Die bore dia – punch tip dia = Clearance.
- Hardness: Usually measured in HRC (Rockwell ‘C’ scale) and optimum readings are as
Follows:
STEEL HARDNESS OHNS O1 58-59
HCHC D2 59-60
HCHC D3 61-62
Normally the following combination is used.
- For punches AISI O1(OHNS)
- For dies AISI D3(HCHC)
- Highly abrasive product AISI D2(HCHC) punches
- Die: hardened steel (HCHC) mould to make the shape of a
Die Terminology:
- O.D.: The outside diameter of the die, which is compatible with the die pockets in the press.
- Die Height: The overall height of the
‘B’ Tooling-22.225 mm ‘D’ Tooling-23.820 mm ‘BB’Tooling-22.225 mm
- Die Bore: The cavity where the tablet is made. The Cavity’s shape and size determine the same form of tablet.
- Chamfer: Entry angle of the die
- Taper dies: dies with tapered bore on one or both They are used for easy ejection of tablets (mainly for double layered tablets.
- Die Groove: The groove around the periphery of the die, which allows the die to be fixed in the press.
- Lined (Insert) Dies: Dies fitted with a linear insert made from a much harder, more wear resistant
Material such as tungsten carbide and ceramic.
Made of tooling:- OHNS :- Oil harden non sticky stainless steel HCHC: – High chromium High Carbon
Punch standard: – Europe, Japan, TSM
• Cleaning verification:
- Determination of effectiveness of a cleaning process for a specific cleaning agent
• Cleaning validation:
- Assure the effectiveness and consistency of a cleaning process to remove residues and contaminants
• Why cleaning validation?
- Assurance of quality and safety
- Product / batch integrity
- Regulatory requirement
- Customer requirement
- Protection from cross contamination
- Proper use of equipment
• According to 21 CFR part 211, subpart D:
- Equipment and utensils shall be cleaned, maintained and sanitized at appropriate intervals to prevent malfunctions or contamination that would alter the safety, identity, strength, quality or purity of the drug product beyond the official or other established requirement
- Written procedures shall be established and followed for cleaning
GMP Maximum Acceptance Criteria:
- Concentration which results in no more than 10 ppm of the active in the subsequent
DEFINATION:
- Clean hold time is defined as the time between the completion of cleaning and the initiation of the subsequent manufacturing operation.
- Dirty hold time is defined as the time between the end of manufacturing operation and the beginning of the cleaning process.
- Campaign Cleaning: Campaign cleaning shall be performed after a series of same product batches manufacturing with batch-to-batch cleaning procedure. Campaign cleaning shall be performed if 8 batches of same product have been processed or 3 days have passed, whichever is earlier.
- Batch to Batch Cleaning: A cleaning shall be performed, between batch and subsequent batch, where previous and next product is same.
- Cleaning Verification: The methodology verify that a cleaning method reduces the residues of previous product from the surface of the equipments as limit established during cleaning verification as well as control potential microbial contaminant.
- Maximum Allowable Residue (MAR): An acceptable transferred amount of residue from the previous product to next product.
SELECTION CRITIERA OF THE PRODUCT FOR CEHT & DEHT Study:
Based on the following criteria location of swab sampling for cleaning validation study has been identified in various equipment’s.
- Design of the equipment
- Location of the machine parts which is not possible to clean easily (Hard to clean area) Technical / Personal experience with the machine.
- Dirty hold time study and clean hold time study shall be performed for the selected
- The selection criteria for product are :
- Product likely difficult to remove during cleaning
- Probability of microbial proliferation is
- One of the following material having property of difficult to remove during cleaning and most likely to be used in formulation as binding material or modified release material.
- Crospovidone Property : Binding agent
- PVPK – 30 Property : Binding agent
- Hypromellose or HPMC Property : Modified release agent
- Hydrogenated castor oil Property : Modified release agent
- Following are the list of excipients, which are considered prone for microbial proliferation but not limited to.
- Maize Starch
- Lactose
- Micro crystalline cellulose
- Sodium starch glycollate
- Pre gelatinized starch
- Sucrose / Gelatin
- Natural or artificial or polymer substance
- Food grade color
RATIONALE:
- Intuitively, it makes sense to be concerned about both hold times. Dirty equipment is harder to clean the longer the hold time, and clean equipment has a greater chance of becoming soiled as hold time increases.
- Product formulation comprises the material/s, which may have properties such as sticky nature; stain formation etc. may difficult to clean with the holding time after usage. For example binding material and material which is used for modified release product may have the property which makes difficult to clean while equipment holding.
- Product, which contains the materials, which is prone to support microbial proliferation during dirty equipment holding is considered.
- The materials that are produced from organic or biological origin are more likely to support to microbial proliferation.
- It is not possible to have all the above listed materials contain in one product formulation. So, only one product which formulation contains one or more materials meeting above criteria i.e. Product likely difficult to remove during cleaning and Probability of microbial proliferation is high shall be selected to perform the dirty hold time study and clean hold time study.
SELECTION OF THE PRODUCT:
- Following are the details of materials used in product to be manufactured in Formulation Block 1.
Ø Selected Product details are:
Product Name: Risperidone Tablets USP 0.25mg
Difficult to clean material: Hypromellose 2910 (6cps)
Microbiologically active materials: Lactose, Microcrystalline cellulose, Sodium starch glycollate, Pre gelatinized starch.
Note: The amount to the Hypromellose 2910 (6cps), Lactose, Microcrystalline cellulose, Sodium starch glycollate, Pre gelatinized starch is as give below:
Sr. No. | Materials used | Selection criteria | % Amount used in formulation |
1 | Lactose | Probability of microbial proliferation is high | 76.85% |
2 | Micro crystalline cellulose | Probability of microbial proliferation is high | 7.39% |
3 | Sodium Starch Glycolate | Probability of microbial proliferation is high | 3.45% |
4 | Pregelatinized Starch | Probability of microbial proliferation is high | 7.88% |
5 | Hypromellose 2910 (6cps) | Modified release agent | 1.11% |
Total % of Amount used in formulation | 96.67% |
SELECTION OF THE EQUIPMETNS
SELECTION CRITIERA AND RATIONALE OF THE EQUIPMENTS:
- All the product contact manufacturing and packing equipments having criticality and complexity (by design) in cleaning shall be considered to establish the dirty hold time and clean hold time.
- A product is selected having critical and complex (by design) equipments to establish the dirty hold time and clean hold time because it is difficult to clean the critical and complex equipment.
- A product lying in above criteria can represent the other equivalent (identical by design) equipments installed in formulation block-1.
SELECTION OF THE EQUIPMETNS FOR A PRODUCT ………………..
Product Matrix train (A) :- There are all points below table
1.Product name | 2.Active ingredients | 3.Therapeut ic category | 4.Solubility in water | 5.ST D(m g) | 6.PDE(mg) | 7.Av.Wt .(mg) | 8.Batch size (In no.) |
9.LDD (mg) | 10.MLDD (mg) | 11.Batch size(kg) | 12. Formulation type | 13.MAR Value(mg):-TDD criteria Therapeutic Daily Dose Criteria = STD* SBS* 1000* 1000*SF/ MLDD | |||
PDE Criteria = PDE* SBS* 1000* 1000/ MLDD |
Where
LDD-Largest daily dose/ MLDD- Maximum Largest daily dose/ STD- Smallest therapeutic dose / PDE-Permitted Daily exposure / SBS- Smallest Batch size SF-Safety factor
Equipment Matrix train (B):-
1.Area | dispensing | Granulation | Compression/capsules filling | Coating | Blister/bulk Packing. |
2. Equipment name………………………………………………………………………….. | |||||
3. Cleaning SOP………………………………………………………………………………. |
Zone | Type of Climate |
Zone I | Temperate zone |
Zone II | Mediterranean/subtropical zone |
Zone III | Hot – Dry zone |
Zone IV a | Hot – Humid/tropical zone |
Zone IV b | ASEAN testing conditions hot/higher humidity |
Long Term Testing Conditions
Climatic Zone | Temperature | Humidity | Minimum Duration |
Zone I | 21ºC ± 2ºC | 45% RH ± 5% RH | 12 Months |
Zone II | 25ºC ± 2ºC | 60% RH ± 5% RH | 12 Months |
Zone III | 30ºC ± 2ºC | 35% RH ± 5% RH | 12 Months |
Zone IV a | 30ºC ± 2ºC | 65% RH ± 5% RH | 12 Months |
Zone IV b | 30ºC ± 2ºC | 75% RH ± 5% RH | 12 Months |
Refrigerated | 5ºC ± 3ºC | No Humidity | 12 Months |
Frozen | -15ºC ± 5ºC | No Humidity | 12 Months |
Accelerated and Intermediate Testing Conditions
Climatic Zone | Temperature | Humidity | Minimum Duration |
Accelerated Ambient | 40ºC ± 2ºC | 75% RH ± 5% RH | 6 Months |
Accelerated Refrigerated | 25ºC ± 2ºC | 60% RH ± 5% RH | 6 Months |
Accelerated Frozen | 5ºC ± 3ºC | No Humidity | 6 Months |
Intermediate | 30ºC ± 2ºC | 65% RH ± 5% RH | 6 Months |
Stability ZONE:-
Zone -I | Zone – II | Zone-III | Zone- IV |
United Kingdom | United States | Iran | Brazil |
N. Europe | Japan | Iraq | Ghana |
Canada | S.Europe | Sudan | Indonesia |
Russia | India | Philippines |
⚫ Guidance requirements USFDA; EU Annex 15 and EMA process
Approach to Process Validation
Process validation is defined as the collection and evaluation of data, from the process design stage through commercial production, which establishes scientific evidence that a process is capable of consistently delivering quality product. Process validation involves a series of activities taking place over the lifecycle of the product and process. This guidance describes process validation activities in three stages.
Stage 1 – Process Design: The commercial manufacturing process is defined during this stage based on knowledge gained through development and scale-up activities.
Stage 2 – Process Qualification: During this stage, the process design is evaluated to determine if the process is capable of reproducible commercial manufacturing.
Stage 3 – Continued Process Verification: Ongoing assurance is gained during routine production that the process remains in a state of control.
Validation work requires considerable resources such as:
Time: Work is subject to rigorous time schedules.
Money: May need specialized personnel and expensive technology.
People: Collaboration of experts from various disciplines.
Advantages of validation:
- During the process the knowledge of process increases
- Assures the repeatability of the process
- Assures the fluency of production
- Assures that the product is continuously according to the marketing authorisation
- Decreases the risk of the manufacturing problems
- Decreases the expenses caused by the failures in production
- Decreases the risks of failing in GMP
- Decreases the expenses of the every day production even though the validation itself will create expenses
REVALIDATION
- Change in Batch
- Change in location of product manufacturing
- Change in Major Equipment or major part of the equipment impacting the product
- Change in manufacturing
- If there is any change in the Regulatory
- Change in API
- As per review recommendation in
Validation Glossary:-
_ User Requirement Specification (URS)
_ Design Qualification (DQ)
_ Impact Assessment
_ Factory Acceptance Testing (FAT)
_ Installation Qualification (IQ)
_ Calibration
_ Site Acceptance Testing (SAT)
_ Operational Qualification (OQ)
_ Standard Operating Procedures (SOP)
_ Performance Qualification (PQ)
_ Process Validation (PV) Change Control.
Tier-1: SD should NMT 3.0%
Mean value of test results should NLT 95.0 % and NMT 105.0% of the labeled amount. (For 10 locations X 1 samples). Total 10 samples.
Tier-II: SD should NMT 5.0%
Mean value of test results should NLT 95.0 % and NMT 105.0% of the labeled amount. (For 10 locations X 3 samples). Total 30 samples. @@
If results are not within limit as per tier-I, then proceed for tier-ii and analyse the remaining 20 samples.
REMARKS (@@)- If SD between 3.1%-5.0% in BU Analysis test, Content uniformity should be performed as per Tier-II criteria only and send all 40 locations sample in compression stage for content uniformity (By stratified sampling method)
Die selection for BU:-
Volume = Mass/Densityx1000
For Examples- Avg. wt. = 200mg, 1x to 3x (200mg-600mg) i.e. 2x is 400mg hence Die volume (ml) = 400/0.5X1000
=0.8ml or 0.8cc
OPERATING PRINCIPLE:
Operating principle for sampling thief
- Sampling thief is supplied with inner shaft and outer shaft,
- Threaded knob is provided on outer rod to fit the appropriate split sampling dies to be use for sampling in inner shaft.
- Put the required dies in the inner shaft of thief and insert in to main body of thief, after this insert the thief into powder bed with specific angle in close condition and rotate the Inner thief with help of handle to open the dies in side material bed, After proper powder filling close the inner shaft with anti- direction and pull out the thief in close condition from powder bed.
- The different size of dies can be put in the inner shaft of sampling thief as per
- After removal of sampling thief from the powder bed remove the inner shaft and kept on PVC stands to hold the outer and inner shaft separately and retrieving the dies with a dies retrieval tool.
PERFORMANCE OF SAMPLING THIEF:
- PASSIVATION:
- Prior to start the performance qualification passivates the sampling rod and its parts as per Following procedure. The objective to passivate the above items is to remove the welding flux, Welding splatter and alloy containing carbon.
PROCEDURE OF PASSIVATION:
- Initially wash all above parts with potable water and then dip the Sampling rod
in 4 % W/V Citric acid solution for 1 Hrs. at room temperature. After completion of this Treatment remove all items from solution and wash with ultra filter water for 10 minutes and then purified water for 5 minutes. After completion of final wash send the rinse sample to QC for PH
Analysis as per Annexure -II. Dry the all parts. Record the procedure followed as below.
- Quantity of 4% W/V citric acid: Liter
- Passivation start time & date:
- Passivation end time & date:
- PH of rinse sample (Result) :
· Acceptance criteria:
PH of rinse sample should be between 5 to 7
PERFORMANCE VERIFICATION
- For performance qualification of sampling thief ensure cleanness of sampling thief as per SOP DFQA-13
- Perform the sampling in available material and record the detail
- Take Maximum and minimum available die size for checking performance of sampling
- Check for smooth insertion and ejection of die before starting
- Insert Die in die cavity and withdraw sample by using Maximum and minimum die size in triplicate.
ACCEPTANCE CRITERIA:
- Conical Knob shall be fixing properly
- Inner and outer Rod shall be rotate smoothly before and during
- Die shall be easily inserted and ejected before sampling and during
- Die pocket shall completely filled while sampling as per SOP DFQA-003 .
- Safety Lock of sampling device shall be work properly during
- Conical Knob shall remain as such in position during
- Die shall be easily inserted and ejected by using ejection block
Material: Anhydrous Lactose USP-NF/Blended granules Name of Material: AR No./B.NO :
Balance ID: Date of Calibration:
Bulk Density (If Applicable)
TABLE FOR MATERIAL WEGHT:
Sr. No. | Sampling thief | Position | Size of die (in cc) | Tare Weight of vial | Gross Weight of vial | Wt. of powder Blend (g) | Done By |
1 | 1600 mm | Top | Min) | ||||
Middle | Min) | ||||||
Bottom | Min) | ||||||
2 | 1600 mm | Top | (Max) | ||||
Middle | (Max) | ||||||
Bottom | (Max) |
Results: Complies/ Not Complies
Performance Qualification Parameters:
- Procedure of Passivation:
Sampling device shall be cleaned as per procedure below
- Dismantle both hollow pipes and insert holder, insert cover screw of sampling device and dismantle split dies.
- Inspect all parts of sampling device & dies for corrosion, if
- Flush all parts of sampling device & dies with Ultra filter water till removal of any extraneous matter.
- Prepare 4% w/v Citric Acid solution as per Annexure-II and kept the sampling device & dies in Citric Acid solution for 1 Hr.
- Drain the acid
- Clean the device, dies, inner and outside with sufficient quantity of ultra filter water and followed purified water.
- Collect the rinse samples of water and check the pH of water with pH meter as per Ref. Spec. No. RMS/016 (pH Limit- between 5.0 and 7.0).
- If pH found within the limit, follow point j) and
- If pH not found within the limit, follow point f) and onward; till the pH is found within the limit.
- Inspect all parts of device and dies, visually for removal of extraneous matter, if any repeat the point c) to g).
- Dry all parts of sampling device & dies at room temperature or using hot air
- Assemble sampling
- Quantity of 4% W/V Citric acid: Liter
- Passivation start time & date:
- Passivation end time & date:
- pH of rinse sample (Result):
Acceptance criteria:
PH of rinse sample should be between 5.0 to 7.0. Results: Complies/ Does Not Complies
. PERFORMANCE QUALIFICATION PARAMETERS VERIFICATION
1.0 Measurement of die volume through Water:
- For Sampling Thief (Triplicate Unit Dose Sampler) Determination of Acceptance range:
- Capacity of dies shall be checked by using water with known density as mentioned below and shall be recorded in Annexure-III.
- Record the density of water before
- Calibrated pipette shall be used for measurement water and calibration status shall be recorded in Annexure-III.
- Take known volume of water “A” (higher than volume of cavity) in calibrated pipette and Recorded in Annexure-III., (e.g. if volume of cavity is 0.2 CC than volume of water should be Higher than 0.2 ml.)
- Carefully fill water in cavity (up to neck) of die and ensure that water should not leak out or spill out from cavity.
- Remaining water in pipette “B” shall be recorded in Annexure-III.
- Calculate the filled water volume in cavity as
Volume of cavity = Initial water volume in pipette – Remaining water volume in pipette
C = A- B
e.g.
Standard volume of cavity is 0.2 CC.
Known volume of water taken is 0.50 ml = A
After filling water in cavity, remaining water in pipette is 0.30 ml = B
Then
C = A- B
C = 0.50-0.30 = 0.20 ml.
Thus
The volume measured of cavity C = 0.2 ml.
- Cavity of volume shall be recorded in Annexure-
- Perform the step 1.4 to 1.8 shall be repeated two times for each cavity of die.
- Calculate the mean of C and recorded in Annexure-III
- Perform step 1.4 to 1.8 shall be performed for each cavity of dies from 0.2 CC to
2.0 CC And recorded in Annexure-III.
B) For Sampling Thief (Single slot Unit Dose Sampler):
- Capacity of continuous single slot shall be checked by using powder material with known density.
- Record the density of selected powder material before its
- Fill the material in inner continuous single slot & record the same for ensuring the capacity of inner continuous single slot individually in Annexure – IV
- Inner continuous single slot shall be able to fill the respective quantity of selected material as per its design.
Material used for testing Purpose:-
Material Name | : | |
Quantity Required | : | |
Density of Material | : | |
Instrument Name | : | |
ID No. | : | |
Calibration Details | : |
Results: Complies/ Does not complies
Proposal for improvement in Process Validation Concept
STEPS
- Knowledge Acquisition
- Risk assessment with respect to Process understanding and Product knowledge
- Determine number of batches based on risk
- KNOWLEDGE ACQUISITION
- Development information
- Other prior knowledge
- Degree of process understanding by unit operation
- Process predictability and models (e.g. Rare reactions)
- Effects of scale change / scale down models
2. RISK ASSESSMENT
Potential factors to consider Source in current system at TPL
- Raw material variability Product Development Report
- Equipment capability Facility Assessment Report
- Previous experience with process performance Pilot batches, Optimization batch Finally assign the residual risk as follows:
Residual Risk Description
Severe (5) Multiple factors have high risk ratings
High (4) Few factors have high risk ratings or all have medium Moderate (3) Multiple medium risk factors or one high risk factor Low (2) Medium risk for a few factors; others are low
Minimal (1) All risk factors are low
3. DETERMINE NUMBER OF BATCHES
Three approaches described:
- Rationales and experience
- Target process confidence and process capability
- Expected coverage
Approach 2: Target Process Confidence and Capability:- –
By definition, Cpk of a capable process is ≥ 1.0
- For low residual risk processes, Cpk ≥ 0 at 90% confidence is set as “baseline”
- Degree of confidence should be greater for higher residual risk processes
As per FDA – ALCOA as per EU – CCEA
Sr. No | Terminology | Scope / Interpretation. | Reference / Remark. |
1 | Attributable | Who performed an action and when? If a record is changed, who did it and why? Link to the source data | Who did it? Source data |
2 | Legible | Data must be recorded permanently in a durable medium and be readable | Can you read it? Permanently recorded |
3 | Contemporaneous | The data should be recorded at the time the work is performed and date I time stamps should follow in order | Was it done in “real time’? |
4 | Original | Is the information the original record or a certified true copy? | Is it original or true copy? |
5 | Accurate | No errors or editing performed without documented amendments | Is it accurate? |
6 | Complete++ | All data including repeat or reanalysis performed if any on the sample. | 21 CFR211.194 |
7 | Consistent++ | Consistent application of data time stamps in the expected sequence. | Date time stamps |
8 | Enduring++ | Recorded on controlled worksheets, laboratory notebooks or electronic media. | Medium used to record data |
9 | Available++ | Available I accessible for review I audit for the life time of the record | For the life time of the record |
PROCESS | ||||
Sr. No. | Unit Operations | Sr .N | Critical Process Parameters | Critical Quality Attributes |
1 | Dispensing | 1 | Choice of balance | Quantity of material as per formula |
2 | Calibration status | Quantity of material as per formula | ||
3 | Daily checking of balance | Quantity of material as per formula | ||
4 | verification of material during dispensing. | Identity | ||
2 | Sifting | 1 | Size of the sieve | PSD |
2 | Geometrical mixing | BUA | ||
3 | Milling in comminuting mill | 1 | Size of the screen | PSD |
2 | Type / speed of the blade | PSD | ||
3 | Feed rate of material | PSD | ||
4 | Binder preparation | 1 | Granulation fluid mixing time | Uneven hardness |
2 | Granulation fluid mixing speed | Uneven hardness | ||
3 | Granulation fluid amount | Hardness, Friability, Dissolution | ||
4 | Granulation fluid temperature | Relative impurities | ||
5 | Wet Granulation | 1 | Granulation fluid addition rate | Hardness, Friability, Dissolution |
2 | Dry Mixing time | BUA | ||
3 | Wet Mixing time | Hardness, Friability, Dissolution | ||
4 | Impeller sped | Hardness, Friability, Dissolution | ||
5 | Chopper speed | Hardness, Friability, Dissolution | ||
6 | Ampere load | Hardness, Friability, Dissolution | ||
6 | Fluid bed drying | 1 | Supply air flow rate | PSD, LOD |
2 | Supply air dew point | LOD, moisture content | ||
3 | Drying Time | LOD, moisture content | ||
4 | Inlet temperature | LOD, moisture content, RI | ||
5 | Outlet temperature | LOD, moisture content | ||
7 | Sizing in OG | 1 | Screen size | Granulometry |
2 | Feeding rate of granules | Granulometry | ||
3 | Oscillation rate | Granulometry | ||
4 | Sizing time | Granulometry | ||
8 | Blending/Lubricatio n | 1 | Occupancy | BUA, Assay |
2 | RPM of blender | BUA, Assay | ||
3 | Blending time | BUA, Assay |
9 | Samling of granules | 1 | Selection of sampler | BUA, Assay |
2 | Sample container | Relative impurities | ||
3 | Sample storage | Relative impurities | ||
10 | Roller compaction | 1 | Selection of roller | Granulometry |
2 | Roll speed | Granulometry | ||
3 | Fed screw speed | Granulometry | ||
11 | Tray drying | 1 | Inlet air temp. | LOD, Moisture comntent, RI |
2 | Inlet dew point | LOD, Moisture comntent | ||
3 | Drying time | LOD, Moisture comntent | ||
12 | Compression | 1 | Turret RPM | Weight variation, Hardness, dissolution |
2 | Main compression force | Thickness, Hardness, dissolution | ||
3 | Pre-compression force | Thickness, Hardness, dissolution | ||
4 | Dwell time | Thickness, Hardness, dissolution | ||
5 | Feeder speed | Weight variation, Hardness, Thickness | ||
6 | Upper punch entry | Hardness, Thickness | ||
7 | Tooling type used | Hardness, dissolution | ||
8 | Verification of tooling before use. | Product mix-up | ||
13 | Coating suspension preparation |
1 |
Stirrer Mixing speed | Viscosity,apearance of tablets, disso. pattern in case of functional coating |
2 | Stirrer Mixing time | Viscosity, apearance of tablets | ||
3 | Milling time in colloidal mill. | Viscosity, apearance of tablets | ||
14 | Coating | 1 | Coating suspension spray rate | Weight gain, DT in GF |
2 | Atomization air pressure | appearance | ||
3 | Pan RPM | appearance | ||
4 | Pre heat time | appearance, RI | ||
5 | Inlet air velocity | appearance | ||
6 | Inlet air temperature | appearance, RI | ||
7 | Product bed temperature | appearance, RI | ||
8 | Gun to bed distance | appearance | ||
9 | Number of guns | appearance | ||
10 | spray nozzle diameter | appearance | ||
15 | Inspection | 1 | Sample inspection (decision for inspection) | appearant defects |
2 | Soring of rejected tablets/capsules | appearant defects | ||
16 | Extruder process | 1 | Scraper adjustment | PSD |
2 | Roller RPM | dissolution | ||
3 | Sieve size | PSD | ||
17 | Capsule filling in AF-40 | 1 | Room condition | brittlensee, stickiness |
2 | machine SPM | weight of capsule | ||
3 | ECS voltage set up | empty capsule in filled capsules | ||
4 | Locking plate adjustment | Locklength, denting, telescopic | ||
5 | Function of NFD | All cqa | ||
6 | powder tub vaccum | dissolution, DT, weight variation. | ||
7 | Air pressure in locking plate | Locklength | ||
8 | Metel detector | contaminated product | ||
18 | Capsule filling in SA-9 | 1 | Selection of table speed | weight variation, disso. |
2 | Auger speed | weight variation, disso. | ||
3 | Powder level in hopper | weight variation | ||
4 | Air pressure in locking plate | Locklength, denting, telescopic | ||
19 | Polishing of capsules | 1 | Polishing unit speed | appearance |
2 | Vacuum or DEX | unpolished capsules | ||
20 | Samling of tablets/capsules | 1 | Sampling method | Product OOS |
2 | Sample storage condition | Relative impurities | ||
21 | Storage of bulk | 1 | Storage container | LOD, moisture content, friability |
2 | Storage condition | Relative impurities, LOD, moisture content. |
👉□Importance of Annual Product Quality Review? (APQR) is prepared in pharmaceutical to review consistency of the products annually regarding their quality including the deviations, change controls and market complaints. It is used as an effective product quality improvement tool.
👉□Annual Product Review verifies the consistency of the existing manufacturing process. It also helps to determine the quality and process defects of the products. It determines the defects and possible improvements of the method and process. Trend of the yield, analytical results, (very important) manufacturing parameters of the products are also highlighted.
👉□It reviews the quality of raw material and packing material used for the product. Trend of these materials indicates the quality of the material and the supplier also. In-process and the finished product results are reviewed to determine the consistency of the product quality.
👉□Quantity of the final product is reviewed by the trending the yield of every batch. Out of specification helps to determine the process defects during the production of the specific product. Failure of batch is also included in APQR to determine the batch rejection of the product. Stability study and its trend help to determine the defects regarding the product stability.
👉□APQR helps to determine the need of re-validation of the process and effect of any improvement made previously. Corrective and preventive actions and their impact on product quality are also reviewed and determined.
👉□Annual Product Quality Review is a mandatory requirement of Good Manufacturing
Practice. FDA uses the term “Annual Product Review” (APR) while “Product Quality Review” (PQR) term is used in EU-GMP guidelines.
👉□According to 💻💾📀💿21 CFR 211.180 (e) all finished products should reviewed annually for the quality standards to determine the need of the change in specification or manufacturing of drug product. Market complaints and product recalls should also be
reviewed annually. view guideline
👉□PIC/S guidelines state to conduct and document periodic review of the pharmaceutical products annually. Starting and packing material, critical in-process controls, failed batch and their investigation, deviations and changes carried out in the process and analytical procedure should be included in Annual Product Review.
👉□Like other guidelines ICH Q7 too states that Quality Product Review should be conducted annually and reason for the corrective action should be documented and completed in time. view guideline
👉□APQR preparation is not mandatory in WHO GMP but all other regulatory agencies have given notification to prepare the APQR.💊💊💊🙏□💊💊💊
- 21 CFR 180
- PIC/S
- ICH – Q7
4. WHO – GMP: APQR Preparation is not mandatory.
APR US
PQR EUGMP
Comparative Evaluation of APQR with respect to US and Europe:
SR. NO. | Parameter | US | Europe | |
1 | Annual Product Quality Review (APQR)- In US and Europe | It is known as Annual product review (APR) / Product Annual Review (PAR) in US | It is Known as Product Quality Review in EU. | |
2 | The Regulatory authority for the preparation and documentation of APQR | USFDA CDER (Centre for Drug Evaluation and Research) | European Medicine Agency (EMEA) The committee for medicinal product for human used (CHMP) Pharmacovigilance Risk assessment committee (PRAC) Committee for Medicinal Products for veterinary use (CVMP) | |
Regulation and the Regulatory required to prepare the Annual product quality review | ||||
3 | The regulation required for the preparation of the APQR. | 21 CFR 211.180 (e) | EMEA – Part 1. Of the EU GMP Chapter -1. | |
4 | Study and review of all quality related data, returned product , if any complaints and recalls are there for the product and the investigation performed at that time during the review. | It is specified under the 211.192 | It is specified | |
5. | The review of adequacy of any other previous product process or corrective action of the equipment. | Not specified | specified |
6 | The qualification status of equipment and utilities use for product for e.g. HVAC, Water, compresses gases etc. | Not specified | specified |
7 | The study review of starting material used for the preparation of the product. | Not specified | specified |
8 | The review of any contractual agreement signed for that pharmaceutical product which is well define in chapter 7 | Not specified | specified |
9 | The evidence and information related to the salvaged products and review of the same. | specified | Not specified |
10 | The review and data related to the in – process control. | Not Specified | Specified |
11 | The review of Packing material use in preparation of product. | Not Specified | Specified |
12 | Critical insignificant deviations and non conformance observed | Not Specified | Specified |
13 | The review of data stability result of the product | Not Specified | Specified |
14 | The review of Any adverse trend fond during product development | Not Specified | Specified |
15 | The review of Marketing Authorization variation which is submitted, granted or refuse. | Not Specified | Specified |
16 | The data of post marketing commitment | Not Specified | Specified |
17 | The inclusion of review of export product only | Not Specified | Specified |
18 | The data of total no. of batches whether they are approve or reject. | Specified | Not Specified |
19 | The analysed data of the batches that fails to meet the specification should be include in the APQR report | Not Specified | Specified |
20 | The adequacy of any equipment corrective action taken or any previous corrective action taken ( from the previous PQR) | Not Specified | Specified |
DEFINATION:
PRODUCT QUALITY REVIEW (PQR):
Documented regular periodic or rolling quality reviews of all licensed medicinal products with the objective of verifying the consistency of the existing manufacturing process to highlight any trends and to identify product and process improvements or weaknesses for
|
|
|
licensed medicinal products the appropriateness of current specifications for both starting materials and finished products is included
PROCEDURE:
PQR shall be prepared for each product manufactured and tested in a calendar year from January to December.
The Final PQR shall be prepared before the end of first quarter of the next year i.e. 31st March.
Sr. No. | CONTENT |
1 | INTRODUCTION (Objective / Scope / Acceptance criteria) (Describe the objective mentioning evaluation of the product quality with respect to consistency of Quality attributes & Quality Monitoring System during the review period. period.) |
2 | Product Details – Product Name, Generic name, Strength,Label Claim, Description,Batch size, Shelf life, Product Category, Market, Primary Pack, Dosage Form, Batches manufactured, Batches manufactured but not released, Batched released in current review period, Batches carried forward from previous period, Total no. of batches, Test specification, SFG / FG Codes |
3 | Review of analytical results of batch release.- The tabulated & graphical presentation for the analytical results of all the batches manufactured in review period can be attached (if applicable). Pending Release Batches No. Released Rejected |
4 | Review of critical in process control–The tabulated presentation for all applicable critical in process control of all The batches manufactured in review period can be attached. |
5 | a) Review of API – Details of API supply chain are as follows in Table: (Details shall be mentioned for each API vendor) Name of Supplier / Vendor: Original Manufacturer: Sr. AR Manufacturer’s Storage Transport Any Discrepancy Any action Remarks No. No. batch number condition condition deviation on delivery for taken for in container/ discrepancy transport seal/ any other in delivery/ condition ( transport Yes/No) condition deviation |
6 | Review of primary packing material-
Sr. No. Primary packing material Vendor name |
- Review of Laboratory Errors– Any laboratory errors (like laboratory incidence) in Quality Control laboratory having impact on product analysis shall be reviewed and described in this section along with root cause and CAPA.
Sr. No. | LIR No. | LIR Date | B. No. | Product name/ Stage | Test | Root cause | CAPA |
- OOS/OOT batches and investigation– Any test results reported in QC as an OOS and OOT shall be reviewed and described along with root cause and CAPA. Any OOT value reported during analysis shall be reviewed and described.
Sr. No. | OOS/ OOT No. | OOS/OOT Date | Product name/stage | Batch no. | Details of OOS/ OOT | Root Cause | CAPA |
9 All product specific deviations taken irrespective of market-
Sr. No. | Deviation No | Date | B. No. | Details of Deviation | Category of deviation | Approved/ Rejected |
- Review of Change control– All Change Control Proposal related to product carried out to
the manufacturing processes (including packaging) and/or in Analytical Methods/ Specification and/or in equipments (like to like, like to unlike) shall be reviewed and described in this section.
|
During the review period the following change controls were reported. Details of changes are given below in Table:
Sr. No. | CCF No | Date of initiation | Details of Change | Category of change | Status | ||
Approved | Rejected | ||||||
Open | Closed | ||||||
11 Review of stability data-
Sr. No. | Year | Batch No. | Packaging | Reason | Stability type | Status | |
- Review of Market Complaints– Product specific Market Complaint received and investigated in he review period shall be reviewed and described in this section along with root cause and
Sr. No. | Date of Receipt | MC. No | Batch No. | Details of Complaint | Type of Complaint | CAPA |
- Product recall , reason and CAPA– Product specific Recall received and investigated in
the review period shall be reviewed and described in this section along with root cause and CAPA.
- Return goods and salvage– Describe the quantity of goods with reason of returning & it’s salvage details.
- Review of Water Quality (Purified water)- The Status during review Review shall
also be done for any abnormal trend in water quality, any values going above established limits. Mention the monitoring plant SOP reference
16 | Qualification status of critical equipments, stability chambers and utilities- Mention the primary and secondary equipments listed in batch records and utilities used for manufacturing and packing were of qualified status |
17 | Review of Environmental Monitoring– The Status during review period. Review of trend of environmental monitoring parameters shall be done for microbiological monitoring for viable/non viable count. Any out of specification result or significant observation made during environmental monitoring study and status of recommended action taken if any, shall be reviewed and described in this section. Mention the monitoring plant SOP reference. |
18 | Retention samples observation – Details of batch nos. examined and observations. Reference to be given of respective plant SOP. |
19 | Review of marketing authorization and variations to marketing authorizations/ ANDA (as applicable) Any existing/ new Marketing Authorization Variations submitted or Granted or Refused shall be described in this section along with outcome. |
20 | Review of Validation– Product specific, validation status shall be reviewed and described in this section whenever applicable |
21 | Review of importation COAs, transportation data logger– The details of importation COAs, transportation data logger and other relevant information shall be described in the report as per customer requirement and agreement |
22 | Sub-contracting of product – Provide details of all batches given for Sub-contracting during the review period. |
23 | Outsourcing contract evaluation:- Provide details of all out sourcing activities during the review period (As per customer requirement and agreement). |
24 | Post marketing commitments (as applicable)- All Post marketing commitments shall be reviewed for their fulfillment & status to be mentioned. |
25 | Review of Technical Agreement– All Technical Agreement shall be reviewed & updated. |
26 | Review of any previous pending CAPA– Product specific, previous pending CAPA (including recommendation in the previous year PQR) shall be reviewed and described in this section. |
27 | Review of recommendation of previous product review– Review the recommendation of previous product review for its compliance |
28 | Review of product related Regulatory Audit observation: In the review period if any regulatory has identify any concern related to product shall be described in this section along with action taken. |
29 | Any Other Study Data– Any other study like hold time, which has been carried out, will be mentioned along with outcome. |
30 | Summary with conclusion– Put all comments & conclude including the current year trends of OOS, deviations, market complaints as compared to previous year and evaluate the effectiveness of CAPA. |
33 | Recommendation and Corrective Action List shall be drawn for action plan and recommendation if required for each reviewed points. Describe all Recommendation and Corrective Action based on review if any. |
Interim PQR shall be prepared as trend of critical parameter on every four months i.e. January- April, May-August, September – December.
Trend data for critical in process parameters, finished product, analytical parameters and process parameters shall be prepared and reviewed. Critical parameters such as,
For Tablets and Capsule: (As defined in release specification, but not limited to)
A. REVIEW OF ANALYTICAL RESULTS OF BATCH RELEASE
- Average Weight / Fill Weight
- Hardness
- Friability Test
- Disintegration Test
- Dissolution
- Related substances / Impurities/ Residual solvents (If applicable). Impurities are to be defined by RRT.
- Assay
- Microbial Assessment
- Any other product specific parameter
B. REVIEW OF CRITICAL IN PROCESS CONTROL
- Ampere load / Torque
- Total wet mixing time to achieve desired Ampere load
- LOD
- Total drying time to achieve desired LOD
- Average weight, uniformity of weight, net content
- Disintegration Test
- Friability
- Hardness
- Weight gain
- Critical process parameters of top/bottom spray granulation (eg. Spray rate, product bed etc.) Lock length (for capsule product)
- Sealing temperature
- Yield reconciliation at in-process stage and FG stage.
- Product specific parameters shall be reviewed from respective batch
Finish Product Tests includes (but not limited to), Assay, Water / Loss on Drying, Identification, Description, PH, Fill volume, related substances, Dissolution, etc.
Process parameters includes (but not limited to),
Blending time, mixing time, RPM of compression machine, details of yield reconciliation of total batches manufactured in the year.
Graphical representation for trend data of in process Parameters, Finished product analytical parameters and Process Parameters shall be made.Following statistical quality review shall be performed on critical parameters e.g.
- Minimum, Maximum & Mean value of analytical
- Standard Deviation
- Relative Standard Deviation
- Process Capability (CpK)
Process Capability (CpK) shall be carried out for critical analytical parameters e.g. Assay.
CpK= USL-X or X -LSL 3*SD 3*SD
Where LSL = Lower specification limit USL = Upper specification limit
X = mean
SD = Standard Deviation
This calculation helps to understand how close the process is producing outcomes compared to what the
specification is. Interpretation:
CpK < 1.0 i.e. process is not capable
CpK 1.00 to 1.33 i.e. product is barely manufactured CpK 1.34 to 3.00 i.e. process is good
CpK > 3.0 i.e. Process is excellent
Note: Minimum 10 batches are required to calculate the Process Capability (CpK).
Storage Period
All PQR is to be stored for the period of six years.
What is PQR :
Which name is using in MHRA/USA –PQR/APQR
Which guideline
EudraLex Volume 4
Health Science Authorities (HSA) PICS
If OOT found then
If any abnormal trend of the data observed during the compilation and review, it shall be commented in
the report, if required the investigation shall be done.
Introduction:-
- Things will go wrong from time to In the world of pharmaceuticals, we need to ensure that we have robust processes and procedure in place to deal with such situations.
When an unplanned event arises it must be handled through a proper CAPA
- Accordingly FDA’s Quality System Guide, recent Warning Letters and EU-GMP
Chapter 1 clearly emphasise the increasing relevance of a proper QMS management and CAPAs. ICH Q9 on Quality Risk Management and ICH Q10 on
Pharmaceutical Quality Systems empower us to handle issues that arise in our daily work on the basis of risk analysis and its CAPA.
- In any case a sound failure investigation is the key. Here it
is also important to know how to deal with human error based and non-human error based non-conformances.
- Effective root cause analysis is the key to identifying appropriate
Principles Of CAPA:-
- The CAPA and Complaints quality systems are two of the most important windows to compliance and the health of the quality system. They are frequently a focus area for external inspectors.
- Inspectors look at CAPA data to understand whether CAPAs are addressed
thoroughly and promptly. Investigations that are incompletely performed or open for an extended period of time are a red flag for a possible significant unresolved problem or an unresponsive management team.
Types of CAPA:-
- 1 Correction
- 2 Corrective Action
- 3 Preventive Action
- Correction:- Correction / Remedial Action–action to eliminate a detected nonconformity. Corrections typically are one-time A correction is an immediate solution
- Corrective action –action to eliminate the cause(s) of a detected nonconformity or other undesirable The corrective action should eliminate the recurrenceof
the issue.
- Preventive action–action to eliminate the cause of a potential nonconformity or other undesirable potential The preventive action should eliminate or prevent the occurrence of the potential issue.
Definition of SOP – Detailed written instruction to achieve uniformity of the performance of a specific function.
- Header (Company Name, , Subject, SOP No., Page No., Effective date, Review date)
- Footer (Prepared by, Checked by, Reviewed by & Format )
- Objective
- Scope
- Responsibility
- Accountability
- Definition
- Procedure
- Exhibit (attachment & list of cross referred sops/ documents)
- Abbreviations
- Controlled copy distribution
- Revision history
DEFINATION:
Risk Assessment: A systematic process of organizing information to support a risk decision to be made within a risk management process. It consists of the identification of hazards and the analysis and evaluation of risks associated with exposure to those hazards.
General Quality Risk Management Process :-
Initiate Quality Risk Management process –
- Risk Assessment :- Risk Identification
- Risk Analysis
- Risk Evaluation
- Risk Control :- Risk Reduction
- Risk Acceptance
- Risk Review :- Review Events
Quality Risk Management Methodology
- Basic risk management facilitation methods (flowcharts, check sheets )
- Failure Mode Effects Analysis (FMEA)
- Failure Mode, Effects and Criticality Analysis (FMECA)
- Fault Tree Analysis (FTA)
- Hazard Analysis and Critical Control Points (HACCP)
- Hazard Operability Analysis (HAZOP)
- Preliminary Hazard Analysis (PHA)
- Risk ranking and filtering
- Supporting statistical tools
Area classification :-
Non classified area | Classified area |
Black area | Grey area |
Dark grey area | Blue area |
Green area |
Non classified Areas :-
Black area
Non manufacturing areas, such as warehouse, administration and workshop comprises the black area.
Temperature and Relative Humidity should be controlled as per material characteristics in warehouse storage area.
Dark gray area
Areas where primary packaged products are handled, such as visual inspection of ampoules, vials, blisters and final packaging operations comprises the dark gray area.
Depending on the product temperature and relative humidity should be controlled.
Classified Areas
Gray Area
Areas where operations like sampling, dispensing, compounding and producing of solids, semisolids and liquids for oral use comprises of gray area.
These are areas where personnel could come in to direct contact with open materials (starting materials, intermediate product and open primary packaging material).
Blue Area
Parenteral bulk preparation takes place in blue area.
Green Area
Parenteral filling operation takes place in green area.
Area for solid dosage form
Cleanliness class: Class 100000 (unmanned)
Air changes: In working areas number of air changes per hour should be between 10 and 20. Air pressure: Working areas should be maintained as negative pressure with respect to adjacent areas. Pressure difference should be 10 to 15 pa.
Spot exhaustion: Local extraction at dust generating points by separate system is required. Temperature and Relative Humidity should be controlled As per requirement and should be monitored.
• US – ANDA | – FDA | – 18 months to 24 months |
• EU – CTD | – EU | – 1 years to 2 years |
• BRAZIL – Similar | -ANVISA | – 9 months to 12 months |
Generic | – 6 months to 9 months | |
• SOUTH AFRICA | – MCC | – 8 months to 1 years (EDL) |
• AUSTRALIA-CTD | – TGA | – 1 year to 2 year |
• New Zealand -CTD | – Med Safe | – 1 year to 2 year |
• TAIWAN | – MOH, Taipei | – 1 year |
• Mexico | – MOH | – 1 year |
SR. NO. | NAME OF THE REGULATORY AGENCY | WEBSITES |
1. | DCGI (India) | www.cdsco.nic.in |
2. | WHO | www.who.int |
3. | ICH | www.ich.org |
4. | PICs | www.picscheme.org |
5. | USFDA | www.fda.gov/drugs |
6. | Health Canada (Canada) | www.hc-sc.gc.ca |
7. | MHRA (UK)) | www.mhra.gov.uk |
8. | EMEA (Europe) | www.ema.europa.eu |
9. | EDQM (Europe) | www.edqm.eu |
10. | MCC (South Africa) | www.mccza.com |
11. | TGA (Australia) | www.tga.gov.au |
12. | ANVISA WHO (Brazil) | www.anvisa.gov.br/eng/index.htm |
1. Random Sampling:
Samples are taken at random from the whole population of the material.
The only requirement of such random sampling process is that all parts of population have the same chance of being sampled.e.g. Inactive R.M.
2. Systematic Sampling :
Samples are collected on the basis of a given geometric or time pattern i.e at regular intervals. e.g. Sampling of water
3. Representative Sampling:
In representative sampling, various layers are sampled & a composite sample is prepared eg.composite samples from the container sampled.
Room Grade | Class | Area | At-rest Condition | Operational condition | ||
Maximum number of particles permitted/m3 | Maximum number of particles permitted/m3 | |||||
0,5 mm | 5 mm | 0,5 mm | 5 mm | |||
A | 100 ISO class 5 | Aseptic Filling | 3 500 | £ 1 | 3 500 | £ 1 |
B | 1000 ISO class 6 | Background room conditions for activities requiring grade A | 3 500 | £ 1 | 350 000 | 2 000 |
C | 10000 ISO class 7 | Solution preparation | 350 000 | 2 000 | 3 500 000 | 20 000 |
D | 100000 ISO class 8 | Handling of components after washing/Non Sterile- Controlled area (OSD) | 3 500 000 | 20 000 | Not defined | Not defined |
- The minimum air charges for Grade B and Grade C areas shall not be less than 20 air changes per hour in a room with good air flow pattern and appropriate HEPA filters. For Grade A Laminar Air Flow work stations, the air flow rates shall be 0.3 meter per second +/- 20% (for vertical flows) and 0.45 meter per second +/- 20% (for horizontal flows).
- Differential pressures between areas of different environmental standards shall be atleast 15 Pascal (0.06 inches or 1.5 mm water gauge). Suitable manometers or gauges shall be installed to measure and verify pressure differential.
- The final change rooms shall have the same class of air as specified for the aseptic area. The pressure differentials in the change rooms shall be in the descending order from ‘white’ to ‘black’.
- Unless there are product specific requirements, temperature and humidity in the aseptic areas shall not exceed 27 degree centigrade and relative humidity 55%,
- All environment parameters listed under para 3.1 to 3.10 shall be verified and established at the time of installation and thereafter monitored at periodic intervals. The recommended frequencies of periodic monitoring shall be as follows:
- (a) Particulate monitoring in air – 6 Monthly
- (b) HEPA filter integrity testing (smoke testing) – yearly
- (c) Air change rates – 6 Monthly
- (d) Air pressure differentials – Daily
- (e) Temperature and humidity – Daily
- (f) Microbiological monitoring by settle plates and/or swabs in aseptic areas – Daily, and at decreased frequency in other areas.
- Note: The above frequencies of monitoring shall be changed as per the requirements and load in individual cases.
- 2. There shall be a written environmental monitoring program and microbiological results shall be recorded. Recommended limits for microbiological monitoring of clean areas “in operation” are as given in the table below :
Ø TABLE
Recommended Limits For Microbiological Monitoring Of Clean Areas “In- operation”
Ø
Grade | Air sample Cfu / m3 | Settle plates (dia. 90 mm. Cfu / 2 hr. | Contact plates (dia. 55 mm) cfu per plate | Glove points (five fingers) cfu per glove |
A | <1 | <1 | <1 | <1 |
B | 10 | 5 | 5 | 5 |
C | 100 | 50 | 25 | – |
D | 500 | 100 | 50 | – |
- HEPA FILTERS
High Efficiency Particulate Air filters are replaceable extended-media
dry-type filters in a rigid frame having a minimum particle collective efficiency of
- 97 percent for a 0.3 micron particle (standard grade)
- 90 percent for a 0.3 micron particle (low grade)
- 99 percent for a 0.3 micron particle (high grade)
and a maximum clean filter pressure drop of 2.54 cm (1″) water gauge when tested at rated air flow capacity.
- ULPA FILTER
Ultra Low Penetration Air filters are extended media dry filters in a rigid frame that have a minimum particle collection efficiency of 99.999 percent for particles greater than or equal to 0.12 micron in size.
Filter Testing Military standard 282
- Thermally generated particles of di-octyl phthalate (DOP) with average size of
0.3 micron. Nowadays poly-alpha olefin(PAO) or di octyl sebacate(DOS) have replaced DOP.
- Oil mist is produced upon heating these
- Efficiency is then measured S
Sodium flame test (Eurovent 4/4)
- An aerosol of sodium chloride is sprayed into the air then sucked through the filter
- The efficiency is
PRODUCT NAME/STRENGTH | CATEGORY |
Citalopram | Anti-Depressant |
Escitalopram | Anti-Depressant |
Lamotrigine | Anti-Epileptic |
Losartan | Ant-Hypertensive |
Montelukast | Anti-Asthamatic |
Premipexole | Anti-Parkinson |
Telmisartan | Ant-Hypertensive |
Carbamazepine | Anti-Epileptic |
Losartan & HCTZ | Anti-Hypertensive |
Donepezil | Anti-Psychotic |
Isosorbide Mononitrate(ISMN) | Anti-Anginal |
Risperidone | Anti-Psychotic |
Ivabradine | Anti-Anginal |
Dimethyle Fumarate(DMF) | Multiple Sclerosis |
Fenofibrate | Anti-Anginal |
Levetiracetam | Anti-Epileptic |
Indapamide | Ant-Hypertensive |
Lercanidipine | Ant-Hypertensive |
Mirtazepine | Anti-Depressant |
Rivastigmine | Anti-Cholinesterase |
Lamitor | Anti-Convulsant |
Pantoprazole | Anti-Ulcer |
Pioglitazone | Anti-Diabetic |
Zolpidem Tartrate | Hypnotic |
Macitentan | Anti-Hypertensive |
Risperidone | Anti-Psychotic |
Eslicarbazepine | Anti-Convulsant |
Vortioxetine | Anti-Depressant |
Quetiapine | Anti-Psychotic |
Minocycline | Antimicrobial Agent |
Apremilast | Psoriatic Arthritis |
Febuxostat | Anti-hyperuricaemic |
Batch size : 100000 units or at least 1 / 10 of commercial scale batch which ever is larger
API with required quality and characteristics
Batches for preliminary Stability Studies Final Formulation and Packs
Process Optimization/
Qualification/Evaluation(PE batch Process Optimization
/ Product Development Report
Scale – up / Pilot-scale Batches
Batches for stability
data generation
/ submission
Exhibit batch (Bio-batch : 1 / 10 of intended commercial scale)
Comparative Report of Exhibit vs. Process Validation batches
3 Validation batches – Commercial batches
Marketed Product
Major Change
( API, Process, Formula, Equipment, Packaging) – Change Control
Re-validation
1. What are user requirements?
- User Requirements Specification describes what users require from the System. User requirement specifications are written early in the validation process, typically before the system is It is written by the System Owner and End Users, with input from Quality Assurance. Requirements outlined in the URS are usually tested in the Performance Qualification. User Requirements Specifications are not intended to be a technical document; readers with only a general knowledge of the system should be able to understand the requirements outlined in the URS.
2. What is a validation plan?
- Validation Plans define the scope and goals of a validation project. Validation plans are written before a validation project and are specific to a single validation Validation
Plans can include:
Deliverables (Documents) to be generated during the validation process Resources/Departments/Personnel to participate in the validation project Time-Line for completing the validation project
3. What is an IQ document?
- Installation Qualifications are a collection of test cases used to verify the proper installation of a The requirement to properly install the system was defined in the Design Specification. Installation Qualifications must be performed before completing Operational Qualification or Performance Qualification.
4. What is an OQ Document?
- Operational Qualifications are a collection of test cases used to verify the proper functioning of a The operational qualification tests requirements defined in the Functional Requirements. Operational Qualifications are usually performed before the system is released for use.
5. What is a PQ Document?
- Performance Qualifications are a collection of test cases used to verify that a System performs as expected under simulated real-world The performance qualification tests requirements that were defined in the User Requirement Specification (or possibly the Functional Requirements). Due to the nature of performance qualifications, these tests are sometime conducted with power users as the system is being released.
6. What is a Validation Summary Report ?
- Validation Summary Reports provide an overview of the entire validation When regulatory auditors review validation projects, they typically begin by reviewing the summary report. The validation summary report should include:
A description of the validation project
All test cases performed, including if those test cases passed without issue All deviations reported, including how those deviations were resolved
7. What is a Change Request?
- Change Control is a general term describing the process of managing how changes are introduced into a controlled System. In validation, this means how changes are made to the validated system. Change control is required to demonstrate to regulatory authorities that validated systems remain under control after system Change Control systems are a favorite target of regulatory auditors because they vividly demonstrate an organization capacity to control its systems.
8. What is the formula for calculating number of air changes in an area?
- Number of air changes/hour in an area is
= Total Room Airflow In CFM x 60 Total Volume of room in cubic feet
For calculating Total Room Airflow in CFM, first calculate air flow of individual filter. Formula is given below.
Air flow (in CFM) = Avg. air velocity (in feet / Minute) x Effective area of filter
Then find Total air flow. Formula is
Total Air flow = Sum of air flow of individual filter.
Air flow Velocity can be measured with the help of Anemometer.
9. What is dead leg?
- A. A dead leg is defined as an area in a piping system where liquid can become stagnant and not be exchanged during flushing.
10. What is the recommended bio burden limits of purified water & WFI?
- Purified water has a recommended bio burden limit of 100 CFU/mL, and water for injection (WFI) has a recommended bio burden limit of 10 CFU/100 ml..
11. Brief about ICH stability guidelines?
- Q1A- Stability testing of new drug substance & products
Q1B- Photo stability testing of new drug substances & products Q1C-Stability testing of new dosage forms
Q1D-Bracketing & Matrixing designs for testing of new drug substances and products Q1E-Evaluation of stability data
Q1F-Stability data package for registration applications in climatic zone III & IV (Withdrawed)
12. What is a significant change in stability testing?
- A 5% change in assay for initial value.
- Any degradation products exceeds its acceptance
- Failure to meet acceptance criterion for appearance, physical attributes and functionality
- Failure to meet acceptance criteria for dissolution for 12
13. If leak test fail during in process checks what needs to be done?
- immediately stop packing process and check for
- Sealing temperature
- Verify for any possible changes like foil width, knurling
- Check & quarantine the isolated quantity of packed goods from last passed
- Collect random samples & do
- Blisters from the leak test passed containers shall allow to go further and rest must be de-blistered/de-foiled accordingly.
14. How many Tablets shall be taken for checking friability?
- For tablets with unit mass equal or less than 650 mg, take sample of whole tablets
corresponding to 6.5g.For tablets with unit mass more than 650mg,take a sample of 10 whole tablets.
15. What is the formula for calculating weight loss during friability test?
- %Weight loss = Initial Weight – Final Weight X 100
Initial Weight
16. What is the pass or fail criteria for friability test?
- Generally the test is run for once .If any cracked ,cleaved or broken tablets present in the tablet sample after tumbling, the tablets fails the test.If the results are doubtful ,or weight loss is grater than the targeted value ,the test should be repeated twice and the mean of the three tests determined .A mean weight loss from the three samples of not more than 1.0% is considered acceptable for most of the products.
17. What is the standard number of rotations used for friability test?
- 100 rotations
18. What is the fall height of the tablets in the friabilator during friability testing?
- 6 Tablets falls from 6 inches eight in each turn within the apparatus.
19. Why do we check hardness during in process checks?
- To determine need for the pressure adjustments on the tableting Hardness can affect the disintegration time. If tablet is too hard, it may not disintegrate in the required period of time. And if tablet is too soft it will not withstand handling and subsequent processing such as coating, packing etc.
20. What are the factors which influence tablet hardness?
- Compression force
- Binder quantity (More binder more hardness)
- Moisture content
21. Which type of tablets are exempted from Disintegration testing?
- Chewable Tablets
22. Which capsule is bigger in size – size ‘0’ or size ‘1’?
- ‘0’ size
23. What is the recommended temperature for checking DT of a dispersible tablet?
- 25 ±10C (IP) & 15 – 25ºC (BP)
24. What is mesh aperture of DT apparatus?
- 8 -2.2mm (#10) (2.0mm ±0.2mm)
25. What is the pass/fail criterion for disintegration test & Cleaning agent use for cleaning?
- If one or two tablets/capsules fails to disintegrate completely, repeat the test on another
12 additional dosage units. The requirement is meet if not fewer than 16 out of 18 tablets/capsules tested are disintegrated completely.&
26. What is the recommended storage conditions for empty hard gelatin capsules?
- 15 – 25ºC & 35 -55% RH
- Name any three tablet processing problems and explain it? A. Mottling, Capping and lamination.
Mottling–Unequal colour distribution of a tablet.
Capping–Partial or complete separation of a tablet top or bottom crowns.
Lamination– Separation of tablets into two or more layers.
28. Which method is employed for checking “Uniformity of dosage unit”?
- ) content uniformity
B.) Weight Variation
Weight variation is applicable for following dosage forms; Hard gelatin capsules ,uncoated or film coated tablets ,containing 25mg or more of a drug substance comprising 25% or more by weight of dosage unit.
29. What is the recommended upward and downward movement frequency of a basket- rack assembly in a DT apparatus?
- 29 – 32 cycles per
30. Why do we consider three consecutive runs/batches for process validation? Why not two or four?
- The number of batches produced in the validation exercise should be sufficient to allow the normal extent of variation and trends to be established and to provide sufficient data for evaluation and reproducibility.
- First batch quality is accidental (co-incidental),
- Second batch quality is regular (accidental),
- Third batch quality is validation(conformation).
In 2 batch we cannot assure the reproducibility of data,4 batches can be taken but the time and cost are involved.
31. Explain about revalidation criteria of AHU system?
- AHU system shall be revalidated periodically as mentioned in the regulatory AHU shall be revalidated in following cases also.
- When basic design of AHU is changed,
- When clean room volume is changed,
- When new equipment is installed
- When a construction is carried out, that calls for reconstruction of AHU
32. What needs to be checked during AHU validation?
- During AHU validation, following tests shall be carried out
- Filter efficiency test,
- Air velocity & number of air changes,
- Air flow pattern (visualization)
- Differential pressure, temperature and RH
- Static condition area qualification
- Dynamic condition qualification
- Non-viable count
- Microbial monitoring
- Area recovery and power failure
33. Position of oblong tablets to be placed in hardness tester to determine the hardness? Lengthwise / widthwise?
- Position of oblong tablets should be length wise because the probability of breakage is more in this position.
34. Explain in detail about qualification of pharmaceutical water system?
- Qualification of pharmaceutical water system involves three phases
- Phase -1
- Phase -2
- Phase -3
Phase -1 A
test period of 2-4 weeks should be spent for monitoring the system intensively. During this period the system should operate continuously without failure or performance deviation. Water cannot be used for pharmaceutical manufacturing in this phase. The following should be included in testing approach.
- Under take chemical & microbiological testing in accordance with a defined
- Sample incoming feed water daily to verify its
- Sample each step of purification process
- Sample each point of use
- Develop appropriate operating
- Demonstrate production and delivery of product water of required quantity and
- Use and refine the SOP’s for operation ,maintenance ,sanitization and trouble
- Verify provisional alert and action
- Develop and refine test failure
Phase -2
A further test period of 2-4 weeks. Sampling scheme will be same as Phase – 1.Water can be used for manufacturing process in this phase.
Approach should also
- Demonstrate consistent operation within established
- Demonstrate consistent production & delivery of water of required quality and
Phase – 3
Phase 3 runs for one year after satisfactory completion of phase-2.Water can be used for manufacturing process during this process.
Objectives & Features of Phase -3
- Demonstrate extensive reliable
- Ensure that seasonal variations are
- The sample locations, sampling frequencies and test should be reduced to the normal routine pattern based on established procedures proven during Phase -1 & phase – 2.
35. What is the difference between calibration and Validation?
- Calibration is a demonstration that, a particular Instrument or device produces results with in specified limits by comparisons with those produced by a reference or traceable standard over an appropriate range of measurements.
Where as Validation is a documented program that provides high degree of assurance that a specific process, method or system consistently produces a result meeting pre-determined acceptance criteria.
In calibration performance of an instrument or device is comparing against a reference standard. But in validation such reference standard is not using.
Calibration ensures that instrument or measuring devices producing accurate results. Whereas validation demonstrates that a process, equipment, method or system produces
consistent results (in other words, it ensures that uniforms batches are produced).
- Briefly explain about ICH climatic zones for stability testing & long term storage conditions?
A. ICH STABILITY ZONES
Zone
Type of Climate Zone I Temperate zone Zone II
Mediterranean/subtropical zone Zone III
Hot dry zone Zone IVa
Hot humid/tropical zone Zone IVb
ASEAN testing conditions hot/higher humidity.
37. What are the common variables in the manufacturing of tablets?
- Particle size of the drug substance
- Bulk density of drug substance/excipients
- Powder load in granulator
- Amount & concentration of binder
- Mixer speed & mixing timings
- Granulation moisture content
- Milling conditions
- Lubricant blending times
- Tablet hardness
- Coating solution spray rate
38. What is bracketing & matrixing in stability testing?
- Both Matrixing & Bracketing’s are reduced stability testing designs Bracketing
The design of a stability schedule, such that only samples of extremes of certain design factors (ex:strength ,package size) are tested at all time points as in full design. The designs assumes that the stability of any intermediate level is represented by the stability of extremes tested. Matrixing The design of a stability schedule, such that a selected subset of
possible samples for all factor combinations is tested at a specified time point. At a subsequent time point another subset of samples for all factor combination is tested. The design assumes that the stability of each subset samples tested represents the stability of all samples at a given time point.
There for a given time point other than initial & final ones not every batch on stability needs to be tested.
39. What is Regulatory Affairs?
- -Regulatory Affairs in a Pharmaceutical industry, is a profession which acts as the interface between the pharmaceutical industry and Drug Regulatory authorities across the world. It is mainly involved in the registration of the drug products in respective countries prior to their marketing.
40. What are the goals of Regulatory Affairs Professionals?
- Protection of human health Ensuring safety, efficacy and quality of drugs Ensuring appropriateness and accuracy of product information.
41. What are the Roles of Regulatory Affairs professionals?
- Act as a liaison with regulatory agencies Preparation of organized and scientifically valid NDA, ANDA, INDA ,MAA,DMF submissions Ensure adherence
42. What is a New Drug Application?
- The NDA is the vehicle through which drug sponsors formally propose that the FDA approve a new pharmaceutical for sale and marketing in the S. The data gathered during the animal studies and human clinical trials of an Investigational new drug become part of the NDA In simple words, “It is an application which is filed with FDA to market a new Pharmaceutical for sale in USA”
43. What is an Abbreviated New Drug Application (ANDA)?
- It is an application filed with FDA, for a S. generic drug approval for an existing licensed medication or approved drug. In simple words, “It is an application for the approval of
Generic Drugs “
44. What is a Generic Drug Product?
- A generic drug product is the one that is comparable to an innovator drug product in dosage form, strength, route of administration, quality, performance characteristics and intended use.
45. What is a DMF?
- A Drug Master File (DMF) is a submission to the Food and Drug Administration (FDA) that may be used to provide confidential detailed information about facilities, processes, or articles used in the manufacturing, processing, packaging, and storing of one or more human drugs. Important facts regarding DMFs It is submitted to FDA to provide confidential
information Its submission is not required by law or regulations It is neither approved nor disapproved It is filed with FDA to support NDA, IND, ANDA another DMF or amendments and supplements to any of these It is provided for in the 21 CFR (Code of Federal Regulations) 314. 420It is not required when applicant references its own information.
46. What are the types of DMF’s?
- Type I: Manufacturing Site, Facilities, Operating Procedures, and Personnel (No longer accepted by FDA)Type II: Drug Substance, Drug Substance Intermediate, and Material Used in Their Preparation, or Drug Product Type III: Packaging Material Type IV : Excipient, Colorant, Flavor, Essence, or Material Used in Their Preparation Type V: FDA Accepted Reference Information (FDA discourages its use)
Page 4 of 4
Australia (AS 1386): 0.035, 0.35, 3.5, 35, 350, 3500
Germany (VDI 2083): 1, 2, 3, 4, 5, 6
47. What is the difference between GMP & cGMP?
- GMP: GMP is the part of Quality assurance which ensures that products are consistently produced and controlled to the quality standards appropriate to their intended use and as required by the marketing authorization.
GMP are aimed primarily at diminishing the risks inherent in any pharmaceutical production.
Such risks are essentially of two types:
- Cross-contamination (in particular of unexpected contamination)
2. Mix-ups (confusion)
cGMP: Current Good Manufacturing Practices. This means any procedure / system adopted by the manufacturer which proves to be necessary and important for identity, strength and purity of a product.
48. What is the difference between Qualification and Validation?
- Qualification is equipment / instrument oriented but validation is process
49. What is the definition of Validation?
- Validation is the documented program that provides a high degree of assurance that a specific process, method or system will consistently produce a result meeting predetermined acceptance criteria.
50. What is the definition of Qualification?
- Qualification is the action of proving and documenting that any equipment or ancillary systems are properly installed, work correctly, actually leads the expected results. Qualification is part of validation, but the individual qualification steps alone do not constitute process validation.
51. What are the types of validation?
- Process validation, Analytical method validation, cleaning validation, facility validation, Utility validation & software validation.
52. What is the definition of the procedure?
- A. A documented description of the operation to be performed, the precautions to be taken, and measures to be applied directly or indirectly related to the manufacture of an intermediate / API (Reference: ICH Q7A).
53. What is preventive maintenance?
- It is periodic inspection and minor repairs of equipment as per schedule given in the This Enables smooth operation and long life of the equipment. It also avoids major breakdown of the equipment during manufacturing of the product.
There are two types of maintenance.
Preventive maintenance: Schedule maintenance before any break down of machinery which prevents the machine break down.
Breakdown maintenance: Maintenance was done after stopping machine breakdown. Weekly , Monthly, Quarterly, Half yearly and Yearly preventive maintenance.
54. What are the types of different training programs?
- Induction training
- Job oriented training
- cGMP training
- On-going training
55. What are the classifications of residual solvents?
- Residual solvents are classified into three class based on the possible risk to human health:
Class-I (Solvents to be avoided) Class-II (Solvents to be limited)
Class-III (Solvents with low toxic potential)
56. What is the difference between Responsibility and Accountability?
- Responsibility: Personnel directly associated with the implementation of the procedure Accountability: Person directly associated with the implementation of the system under which the procedure falls.
57. Write the names of the different countries regulatory body (Like for India, USA, UK, Australia, South Africa, Brazil, Hungary, Germany, Philippines etc.)
- India – Schedule M
United Status of America – USFDA (United state Food and Drug Administration)
Australia – TGA (Therapeutic Goods Administration)
United Kingdom – MHRA (Medicines & Health care products Regulatory Agency)
South Africa – MCC (Medicine Control Council)
Brazil – ANVISA (Brazilian Health Surveillance Agency or National Sanitary Surveillance Agency)
Hungary – PIC/S (Pharmaceutical Inspection Convention or Pharmaceutical Inspection Cooperation Scheme)
Germany – NIP (National Institute of Pharmacy)
Philippines – BFAD (Beaureu of Food & Drug)
58. What is the different types of Qualifications and write its flow?
- Qualifications are as follows: Design Qualification, Installation Qualification, Operational Qualification, and Performance Qualification.
URS/DS —–FAT—–SAT—–DQ—–IQ—–OQ— PQ
59. What is audit/inspection and Why quality audit? Write different types of audits/inspection?
- A planned and systematic examination and check of a system, procedure or operation in order to monitor compliance with and the effectiveness of established standards and to allow for improvement and corrective measures where required.
Quality audit because of:
- To assess the effectiveness of the quality management system
- Assessing conformance
- Investigating problems
- Continual improvement of performance
- Assessing for Registration
- Reducing cost of operation
- Legal requirement
Types: 1. Study/test based inspection
- Facility based inspection
- Process based inspection
60. Why nitrogen gas used in the manufacturing area at room temperature and why not other gas?
- Because of nitrogen is chemically less reactive and does not react with other elements at ordinary temperature. It is due to strong bonding in its molecule.
- What are the different types of cleanings? A.There are three types of cleanings:
- Batch to Batch cleaning
- periodically cleaning
- Product change over cleaning
62. What is expiry date & re-test date?
- Expiry date: The date place on the container / labels of an API designated the time during which the API is expected to remain within established shelf life specifications if stored under defined conditions and after which it should not be used.
Re-test date: The date when a material should be re-examined to ensure that it is still suitable for use. The period of time during which the drug substance is expected to remain within its specifications and therefore, can be used in the manufacturing of the drug product, provided
that drug substance has been stored under the defined conditions.
63. What is deviation & its types?
- Deviation is departure from the approved instructions /established There are two types of deviation and given below:
Controlled / planned deviation: Any deviation from documented procedure opted deliberately for temporary period to manage unavoidable situation or improving the performance of the operations, without affecting the quality & yield of drug substance and safety of the operations shall be termed as controlled / planned deviation.
Uncontrolled / unplanned deviation: Any deviation occurred in unplanned or uncontrolled manner such as system failure or equipment breakdown or manual error shall be termed as uncontrolled / unplanned deviation.
64. What is change control and its types?
- Change control is a system that control change by
- Identifying ownership of the change
- Allowing for review and approval of the
- Preventing changes that could adversely affect product quality or conflict with registration or regulatory requirement.
- Providing an assessment of change and monitors the impact of
Level 1 (Minor): Are those that are unlikely to have any detectable impact on the quality attributes of the product.
Level 2 (Major): Are those that are likely to have a significant impact on the Quality Attributes of the product.
The type of reasons for change control:
- Regulatory requirement
- GMP implementation / enhancement
- Quality improvement
- Capacity enhancement
- Introduction of new product in existing facility
- Cost reduction
- Automation
- Aging of facility
- To manage the unavoidable situation
- Market requirement
65. What is contamination and cross-contamination?
- Contamination: The undesired introduction of impurities of a chemical or Microbiological nature, or of foreign matter, in to or onto a raw material, intermediate, or API during production, sampling, packaging or repackaging, storage or transport.
Cross-contamination: Contamination of a material or of a product with another material or product.
66. What is Batch number and batch?
- Batch Number: A unique combination of numbers, letters, and/or symbols which identifies a batch (or lot) and from which the production and distribution history can be determined
Batch: A specific quantity of material produced in a process or series of processes so that it is expected to be homogeneous within specified limits. In the case of continuous production, a batch may correspond to a defined fraction of the production. Batch size may be defined either by a fixed quantity or the amount produced in a fixed time interval.
67. What is quarantine?
- The status of materials isolated physically or by other effective means pending a decision on their subsequent approval or rejection.
68. What is definition of critical process parameters?
- A. A process parameter whose variability has an impact on a critical quality attribute and therefore should be monitored or controlled to ensure the process produces the desired quality
69. What is the difference between theoretical and expected yield?
- Theoretical yield: The quantity that would be produced at any appropriate phase of production, based upon the quantity of material to be used, in the absence of any loss or error in actual production.
Expected yield: The quantity of material or the percentage of theoretical yield anticipated at any appropriate phase of production based on previous laboratory, pilot scale, or manufacturing data.
70. What is OOS?
- Out of Specification (OOS) results are those results, generated during testing that do not comply with the relevant specification or standards or with the defined acceptance
71. What is OOT and define?
- “OOT” stands for Out Of It means any test results obtained for a particular batch that is markedly different the results of the batches in a series obtained using a same validated method.
72. What is CAPA?
- CAPA is the Corrective Action & Preventive
Corrective Action: Action taken to eliminate the causes of an existing non-conformity, defect or other undesirable situation to prevent recurrence. [Actions taken after the occurrence of a defect or problem to stop the same from recurrence].
Preventive Action: Action taken to eliminate the causes of potential non-conformity, defect or other undesirable situation to prevent occurrence. [Actions initiated before the occurrence of a defect or problem to prevent the same occurrence].
73. What URS, DS, FAT, SAT, DQ, IQ, OQ, PQ?
- URS:
DS:
FAT:
SAT:
DQ:
Installation Qualification (IQ): Establishing a high degree of confidence that the equipment as installed is consistent with manufacture’s requirements and specifications.
Operating Qualification (OQ): Establishing a high degree of confidence that the equipment as installed is able to consistently operate within established limits and tolerances.
Performance Qualification (PQ): Establishing a high degree of confidence, with appropriate testing that the equipment, under normal operating conditions, will consistently produce a quality product.
74. Difference between validation & testing?
- Both are not same. Testing is defined as the identification of errors (difference between expected & actual results) in a Validation is defined as documented evidence that a system performance as expected. Validation includes testing but it is more – for instance, checking the documents for completeness & correctness.
75. What is the difference between instrument & equipment?
- Instrument: A device that takes a physical measurement and displays a value or has no control or analytical functions. e.g.: Stop watch, timers & thermometer.
[A device <chemical, electrical, hydraulic, magnetic, mechanical, optical, pneumatic> used to test, observe, measure, monitor, alter, generate, record, calibrate, manage or control physical properties, movements, or other characteristics].
Equipment: A device or collection of components that perform a process to produce a result. [The collective analytical measurement instruments in conjunction with firmware, assembled to perform a mechanical process]
76. What is HVAC?
- HVAC system function is to condition (heating & cooling), replace (makeup, fresh air, oxygen replacement), and pressurize (contaminant) and clean (filter) the air in the environment to meet the required operational conditions.
To achieve this objective, electrical, mechanical & electronic components are arranged in several configurations such that they produce the expected results.
77. What is the meaning of Q, S, E, M in the ICH?
- “Q” stands for Quality; “S” stands for Safety, “E” stands for Efficacy and “M” stands for
Multi dispensary.
78. How many types of raw material and packing material?
- Raw materials are classified into two Those are as follows:
- Key raw material
- Other raw material
Packing materials are classified into two types. Those are as follows:
- Primary Packing material
- Secondary Packing material
79. Define the Key raw material/ starting material & primary packing material? Key raw material/starting material:
- Starting material shall be defined as that which is
- Incorporated as a significant structural fragment of the API / Drug Intermediate and
- Having significant effect on the Quality and Yield of the
- Starting material shall be identified in
Primary Packing material: Packing material, which come in direct contact with the API/Intermediate are considered as Primary packing material.
80. How will you prevent cross-contamination between two different products manufactured in the one production block?
- By maintaining the proper pressure differential between the rooms with two Air handling units
(if re-circulation) / one Air handling unit (if 100% fresh air)
81. What is limit of Temperature and relative humidity in the pharma area?
- Temperature: 25±2˚C & Relative Humidity: 50±5%
82. What is the difference between dedicated and non-dedicated equipments?
- Dedicated equipment: It is used solely for the production of a single product or product line. Concerns over cross-contamination with other products are markedly reduced. Dedicated equipment’s must be clearly identified with the restrictions of use in order to prevent potential errors during cleaning and preparation.
Non-dedicated equipment: Where the same piece of equipment is utilized for a range of products formulations. The prevent of cross-contamination between products becomes the main objective in the cleaning validation effort. Clearly, cleaning non-dedicated equipment’s represents a more significant obstacle to overcome.
83. Which instrument is used for the measuring of RPM?
- Techo meter is used for the measurement of
84. Why three batches consider for the validation?
- Because of First one is for information, Second one is for confirmation and Third one is for evidence.
85. If one batch is failed during the validation, then what will you do for completion of validation?
- When a quality parameter fails with respect to the specification, a deviation report shall be raised and the investigation shall be conducted immediately for the identification of failure.
- If the reason for failure is identified, one more consecutive batch shall be considered for the validation run by taking preventive actions to avoid those failures (If necessary revise the MPCR and BPCR).
- If the reason is unidentified, another three consecutive batches shall be taken for Validation
86. What are specifications of Purified water as per any pharmacopoeia? A.
Tests | Ph. Eur. |
Description | Clear, colorless liquid |
Acidity /Alkalinity | The solution is not colored red/The solution is not colored blue. |
Oxidisable substances | The solution remains faintly pink |
Chlorides | The solution shows no change in appearance for at least 15 min |
Sulphates | The solution shows no change in appearance for at least 1 hour |
Ammonium | Maximum 0.2 ppm. |
Calcium and magnesium | A pure blue colour is produced. |
Residue on evaporation | Maximum 0.001 per cent |
Aluminum | Maximum 10 ppb, |
Nitrates | NMT 0.2 ppm |
Heavy Metals | NMT 0.1 ppm |
Conductivity (At 25˚C) | NMT 5.1ms.cm-1 |
Total viable aerobic count | NMT100 CFU /ml |
Pathogens : E. coli Salmonella Pseudomonas Staphalococcus aureus | Absent Absent Absent Absent |
- Write the different types of fires, which are generally used in the pharmaceutical industry?
- Chemical fire
- Electrical fire
- Metal fire
- General fire
- Gaseous fire
- Chemical fire
88. What is ISO 9001, ISO 14001, ISO 18001, ISO 22001?
- ISO 9001 : Quality Standard Management
ISO 14001 : Environmental Standard Management
ISO 18001 : Safety & Health Standard Management ISO 22001 : Hazop Standard Management
89. What is HACCP?
A.HACCP : Hazard Analysis Critical Control Point
90. What is OHSAS?
A.OHSAS : Occupational Health & Safety Assessment Series
91. What is calibration?
- The demonstration that a particular instrument or device produces results within specified limits by comparison with results produced by a reference or traceable standard over an appropriate range of measurements.
92. What is the efficiency of the High Efficiency Particulate Air (HEPA) filter?
- This type of air filter can remove at least 97% particles in air up to 0.3μm in diameter.
93. Do you have any idea about schematic diagram of HVAC system? A.-Fresh Air
-Filtering of Air with Pre filter
-Cooling & Heating coil
-Filtering of Air with Fine filter
-Filtering of air with HEPA filter, If required
-Suction of air through return ducts from the process area using some pre filters as –per requirements
-Air is exhausted to atmosphere after filtration wherever required
-Portion of air then passes through a dehumidifier wherever dehumidifier is required
-In the mixing chamber, return Air & Fresh air get mixed
-Process repeats from
94. If two different products are manufacturing in two modules of one production block, then will you accept the common air handling unit for both pharma area? Write “Yes” or “No” with reason?
- No, because of cross-contamination (if re-circulation of return air) Yes, if 100% of fresh air is circulated through the respective area.
95. Why blending validation is required? What quality parameters of product are considered for validation and what parameters of equipment are to be considered during validation?
- Because of to provide sufficient documented evidence to assure that the blending operation of product is capable of repeatedly and reliably producing a homogeneous material to meet established specifications when operated under defined standard
The following Quality parameters are to be considered, but not limited:
- Loss on Drying / Water content
- Bulk density / tapped density
- Residual solvent
- Particle size
The following parameters are to be considered for the equipment during validation, but not limited:
- Blender capacity
- RPM of the blender
- Occupancy of the blender
- Number of individual batches to be taken for each blend
- Mixing time
96. What is the formula for calculation of “Air changes per hour” during HVAC validation?
- Total CFM of the blower/Filter x 60 Air changes per hour=
Total room volume
97. What is mean by “4M”?
- “4M” means Man, Machine, Method and Material
98. If supposed your pharma area is class 100000, then what is the maximum light and sound level as per guidelines ?
- The light & sound level limits are given below for class 100,000 / ISO 8:
Light Level : Not less than 300 Lux Sound
Level : Not more than 80 decibels
99. Write the classification of contaminants in clean rooms? Substance:
- Physical : Dust, Dirt, Grit, Fiber, Lint & Fly ash
Chemical : Organic compound, Inorganic salts, vapor, mist, fume & smoke
Biologic : Bacteria, Fungus, Spore, Pollen, Virus, Human skin & cells
Energy:
Energy : Thermal, Light, Electromagnetic (EMI), Electrostatic (ESD), Radiation & Electrical
100. What is the name of the instrument, which is used for measuring of vacuum (in Tars) during high vacuum distillation?
- Macleod gauge
101. What is mean by “Clean-in-Place” and “Clean-out-Place”?
- Clean-in-Place: The cleaning of large pieces of equipment may be performed in the equipments permanent Generally, in a configuration very similar to that in which it is utilized for production. This procedure widely known as Clean-in-Place (CIP)
Clean-out-Place: The smaller items are frequently transported to a designated cleaning or washing area where the cleaning procedures is performed. This practice is known as clean- out -place (COP)
102. For which areas do we have SOPs?
- We have SOPs for the following areas:
- Quality Assurance
- Quality Control
- Production
- Personnel
- Warehouse
- Safety & Environment
- Engineering
- Estate Management
- Info tech
103. Why do we conduct trainings?
- It brings awareness and helps us in becoming
104. What is personal hygiene?
- Each personal should:
- Wear clean uniform
- Take bath daily
- Report illness or injury
- Be medically fit
- Develop good hygiene habits
105. What is in-process control?
- Checks performed during production in order to monitor and, if necessary to adjust the process and / or to ensure that the intermediate or API conforms to its specifications.
106. What is critical process parameter?
- A. A process parameter whose variability has an impact on a critical quality attribute and therefore should be monitored or controlled to ensure the process produces the desired
107. What is mean by the word “Quality”?
- Quality is basically customer’s satisfaction through
108. Define stability study and its necessity?
- Stability study is defined as “stability testing is to provide evidence how quality varies
with time
under influence as: temperature, humidity & light”
- Establish re-test period for drug substance
- Establish shelf life for drug product
- Recommended storage conditions
109. What do you mean by “Reference standard” and “Working standard”?
- Reference Standard: A substance that has been shown by an extensive set of analytical tests to be authentic material that should be of high purity. This standard may be obtained from an officially recognized source or may be prepared by independent synthesis or by further purification of existing production material.
Working Standard: A substance of established quality and purity, as shown by comparison to a primary reference standard, used as a reference standard for routine laboratory analysis
110. What is abbreviation of CTD?
- “CTD” means Common Technical This is addressed in the ICH guidelines in the section of “M” and in the part of “M4”
111. What do you mean by market complaint?
- Any communication, written or verbal, received regarding the quality, packing directly from any traders or product manufacturer and marketing staff or any other such complaints shall be considered as a Market Complaint
112. What is maximum time period for the sending of the final response to concerned customer regarding the market complaint?
- Within 30 days or as specified in the Market compliant SOP
113. Describe the categories of the market complaints?
- Market complaints are categorized into three types and are as follows:
Critical: Complaints related to suspected contamination, adulteration and mislabeling. Major: Complaints related to the product not meeting its pre-determined critical specifications and damage to primary packaging.
Minor: Complaints related to the product not meeting non-critical quality attributes, or damage to secondary packaging or shortages etc.
114. What are the types of non-compliances in the internal audit?
- Non-compliances shall be categorized as follows:
Critical: Those findings that warrant stoppage of any further operations in the facility until the corrective actions have been completed.
Major: Those findings that require immediate corrective action plan and compliance although operations can be continued.
Minor: Those findings that require corrective action plan as agreed between the Auditee department Head and Quality Assurance.
115. What do you mean by “worst case”?
- A condition or set of conditions encompassing upper and lower processing limit and circumstances, within standard operating procedures, which poses the greatest chance of product or process failure when compared to ideal conditions. Such conditions do not necessarily induce product or process failure.
116. What do you mean by “performance qualification”?
- The performance qualification documents describes the procedures for demonstrating that a system / piece of equipment can consistently perform & meet required specifications under routine operation and where appropriate, under worst case situations.
117. How will you close a market complaint?
- (a) If satisfactory response obtained from complainant against our written reply
- If the material is recalled
- If no response obtained from the complainant after 90 days (or specified in SOP) from date of our written reply.
118. What is the difference between specification and Limit?
- Specification: A document giving a description of a starting material, packaging material, intermediate, bulk or finished product in terms of its chemical, physical & possibly biological characteristics. A specification normally includes description clauses & numerical clauses, the latter stating standards & permitted tolerances.
Or
Lists of detailed requirements with which the products/ materials used or obtained during manufacture have to conform. They serve as a basis for quality evaluation.
Limit: The point, edge or line beyond which something cannot or may not be proceed. The boundary surrounding a specific area, bounds.
- What are the possible causes for “Out of Specification”? The following are the possible causes for out of specification:
Test analysis error in QC Lab.
Lab equipment malfunctioning or off-calibrated Production equipment malfunctioning or off-calibrated Operator/human errors.
120. What is the definition of document control?
- Document control ensures that documents are reviewed for adequacy, approved for release by authorized personnel and distributed to and used at the location where the prescribed activity is performed.
123. What is the difference between controlled copy and un-controlled copy?
- Controlled copy: A controlled copy is a formal copy of the latest, correct issue of a document; an identified issue of a document to an individual or location of The controlled copy is officially tracked, updated & destroyed to assure that it is current.
Uncontrolled copy: An informal copy of a document for which no attempt is made to update if after distribution; the document is marked “uncontrolled” and the user determines if the document is active prior to use.
121. What do you mean by re-validation?
- A. A repeat of the process validation to provide an assurance that changes in the process/equipments introduced in accordance with change control procedures do not adversely affect process characteristics & product quality.
122. What are the system suitability parameters in the method validation?
- Tailing factor, Theoretical plates, Relative Standard deviation (RSD), Resolution, Retention time (RT), Relative retention time (RRT), Capacity factor.
123. When to qualify & validate?
- Any aspect of, including significant change to the premises, the facilities, the equipment or the process, which may affect the quality of the product, directly or indirectly, should be qualified and validated.
124. What are the advantages of Swab sampling?
- – Dissolves & physically removes sample
- Adaptable to a wide variety of surfaces
- Economical & widely available
- May allow sampling of a defined area
- Applicable to active, microbial & cleaning agent
125. What are the advantages of Rinse sampling?
- – Adaptable to on lime monitoring
- Easy to sample
- Non-intrusive
- Less technique dependent that swab
- Applicable for active, cleaning agents & excipients allow sampling of a large surfaces
- Allows sampling of unique (e.g. porous)
126. What are the different climate zones in the world?
- World is divided into the Five climate zones and are given below: Zone Name Conditions
- Temperate 21° C / 45% RH
- Subtropical & Mediterranean 25° C / 60% RH
- Hot & Dry 30° C / 35% RH
IVA Hot & Humid 30° C / 65% RH
VB Hot & Very Humid 30° C / 75% RH
127. What is a DMF?
- A DMF is a package of proprietary information filed voluntarily by a company with the FDA. If it held by them in confidential closed files until such time as an FDA reviewer requests a review of the DMF.
128. What are the types of DMF?
- There are four types of DMF. They are referred to by their numbers in Roman numerals: Type-II: DMF is for companies who supply drug substances, drug products, intermediates & material used in their manufacture.
Type-III: DMF is for companies who supply packaging (container closure system) for human drugs & biologics.
Type-IV: DMF is for companies who supply excipients
Type-V: DMF is for companies who supply clinical services, sterile manufacturing etc.
Type-I: Is an obsolete number once used for a category that no longer exists because it was found to easily fit into and overlap with the other four categories.
129. What are the possible reasons for the Non-conformities?
- The following are the possible reasons, but not limited:
- Management attitude
- Ineffective documentation
- Lack of trained personnel
- Lack of co-ordination / co-operation within or among
130. What do you mean by Critical Quality Attributes?
- A. A critical quality attributes is a physical, chemical, biological or microbiological property or characteristic that should be within an appropriate limit, range, or distribution to ensure the desired product quality.
131. What do you mean by Non-conformity?
- Non-conformity is non-fulfillment of a specified or implied requirement of the quality management system or of a quality work product.
132. Describe the method of testing for checking of MOC of SS material (Molybdenum test)?
- Procedure:
- Put one drop of electrolyte solution of molybdenum test kit on clean metal surface, which is to be tested.
- Switch on the detector and touch the metal tip of the detector on metal surface & carbon point in electrolyte solution.
- Do not pass the current for more than 3 to 4 seconds
- If the red color appears and is stable for more than 2 seconds then it can be concluded that MOC of the part being tested is SS-316.
- If the solution remains colorless or green color appears then it can be concluded that MOC of the part being tested is SS-304.
- If the black color appears & is stable for more than 2 seconds then it can be concluded that MOC of the part being tested is SS-302.
133. What is the solubility data as per any Pharmacopoeia?
- Approximately volume of solvent in ml per gram of solute at 20° to 30° C
Very soluble : Less than 1
Freely soluble : From 1 to 10
Soluble : From 10 to 30
Sparingly soluble : From 30 to 100
Slightly soluble : From 100 to 1000 Very slightly soluble : From 1000 to 10000 Insoluble / practically soluble : More than 10000
Example: Very soluble means one gram of solute substance will require less than 1 ml of solvent.
134. What do you mean by reconciliation?
- A. A comparison, making due allowance for normal variation, between the amount of product or material theoretically & actually produced/used.
135. What is the Batch production and control record (BPCR)?
- BPCR are prepared for each intermediate and API and include the complete information relating to the completion of each significant step in the Batch production.
136. What is the Master production & control record (MPCR)?
- To ensure the uniformity from batch to batch, master production instructions for each intermediate and API are prepared, dated and signed by one person, immediately checked, dated and signed by a person in the quality unit.
137. What are the different types of safety factors used in the pharmaceutical industries?
- 1/10 to 1/100th of normal daily dose = Topical products 1/100 to 1/1000th of normal daily dose = Oral products
1/1000 to 1/10000th of normal daily dose = Inject able & Ophthalmic products 1/10000 to 1/100000th of normal daily dose = Research, investigational products.
138. What are the contents of Annual product quality review (APQR)?
- 0 Introduction
- Number of Intermediates and APIs batches produced
- Review of out put for all Isolated Intermediates and Finished Products
- Review of Critical Quality attributes of In-process, Isolated Intermediates and Finished Products.
- Summary of changes made during the year with respect to equipment, Process, Specifications, and Methods, Raw materials and others.
- List of Deviations and a brief description of deviations and action
- List of customer complaints; Return goods and Recalled goods along with description and actions taken
- Number of Reprocessed and Reworks batches in all stages during the year- 2009
- Review of Key starting materials and Primary packing materials and
- Review of Bio burden on product (for minimum of 3 batches)
- Review on Stability studies and Summary
- List of Out of specifications for Finished products
- Review on Retained samples quality (Finished product)
- Review on Validation packages (Process, Equipment, Procedure)
- Status of Drug Master File (if any),Drug Master File new updates
- Details of special training provided to employees in case of Deviations or Complaints received regarding a particular product
- Summary
139. What do you mean by customer satisfaction?
- Customer’s perception of the degree to which the customer’s requirements have been
fulfilled
Any customer wants three things:
- Good product
- Timely feedback
- Timely supply
140. What is the QMS?
- It is the quality management system to direct and control an organization with regard to
141. What do you mean by pre-determined acceptance criteria?
- The criteria assigned, before undertaking testing to allow evaluation of test results to demonstrate compliance with a test phase of delivery requirement.
142. What is Master validation Plan (VMP)?
- A document providing information on the company’s validation work It should define details of and timescales for the validation work to be performed. Responsibilities relating to the plan should be stated.
143. What do you mean by product recall?
- Products recall means removal or withdraw of marketed material due to violation in laws & regulations as per regulatory authorities or not conforming to the customers’
144. What do you mean by residual solvent?
- These are the traces of the solvents left during the manufacturing of drug substances or drug products. Residual solvents are not completely removed by practical manufacturing
145. How can we avoid contaminations in warehouse?
- Contamination can be avoided by:
- Proper segregation / identification of different RMs
- Following good house keeping procedures
- Having dedicated sampling tools for each RM
- Segregated rejected materials
- Segregated storage of penicillin RMs
- Separate sampling booth/enclosure for RMs
146. What is retention sample & why retention sample is preserved?
- A. A part of the sample which is representative of the released batch of a finished product preserved beyond its shelf life.
It is preserved for future reference / reanalysis in cases of market complaints or development
work or any other clarification about the released batch.
147. What will happen if cGMP are not followed?
- Non-compliance to cGMP may lead to:
- Poor quality of product / services
- Batch failure
- Market complaints and product recalls
- Company’s reputation affected
- Business will be affected
- Regulatory action
- Injuries or accidents
- Equipment failures
148. What are the safety systems in the plant?
- Some of the safety systems used in the plant are:
- Eye washer, safety showers
- Fire extinguishers
- Fire hydrants
- Face shields
- Goggles
- Helmets
- Nose masks
- Safety shoes
- Safety belts
- Hand gloves
- Training on safety rules and use of safety
149. Would you like to recommend any precautions while operating the equipment?
- Following precautions are recommended:
- Make sure that each equipment is numbered and its log is
- Check whether the equipment is cleaned as per SOP
- Always follow product changeover procedure during product changeover
- Take care of safety rules
- Monitor operating conditions
150. Write the different parts of 21 CFR and details of different subparts of 21 CFR 211?
- 21 CFR Part 11 : Electronic records, Electronic signatures, Electronic copies of electronic record.
21 CFR Part 58 : GLP for Non-clinical Laboratory studies regulation.
21 CFR Part 210 : cGMP in manufacturing, processing, packing / holding of drug. 21 CFR Part 211 : cGMP regulations for finished pharmaceuticals.
21 CFR Part 820 : GMP regulations for Medical devices.
151. What is clean zone and clean room?
- Clean zone: A defined space in which the concentration of air borne particles is controlled to meet a specified air borne particulate cleanliness class
Clean room: A room in which the concentration of air borne particles is controlled and contains one or more clean zone.
152. What is As-built clean room (facility)?
- A. A clean room (facility) that is complete and ready for operation, with all services connected and functional, but without equipment or operational personnel in the
153. What is At-rest clean room (facility)?
- A clean room (facility) that is complete and ready for operation, with all services functioning and with equipment installed and operable or operating, as specified, but without operating personnel in the facility.
154. What is Operational clean room (facility)?
- A. A clean room (facility) in normal operation, with all services functioning and with equipment and personnel, if applicable, present and performing their normal work functions in the facility. Some other terms used in the clean rooms:
155. What is unidirectional and non-unidirectional air flow?
- Unidirectional air flow: Airflow having generally parallel steam lines, operating in a single direction, and with uniform velocity over its cross section; previously referred to as
“laminar” air flow
Non-unidirectional air flow: Air flow which does not meet the definition of unidirectional air
flow, previously referred as “Turbulent or Non-Laminar” air flow.
156. Describe about the Purified water system and validation?
- The purified water system consists of following pre-treatment before final production of purified water.
- Pre-Treatment
- Reverse Osmosis (RO) Unit
- Electro De-ionization (EDI) System
- Ultra filtration,
Pre-Treatment:
Raw water is supplied from the APIIC (Andhra Pradesh State Industrial Infrastructure Corporation Ltd.) (Manjeera water) and is stored in raw water tank, then the raw water is chlorinated thereafter. The chlorinated water is then transferred to the Pressure sand filter to remove the suspended solids and sodium Meta-bisulphite is dosed in the filtered water to neutralise any trace of residual chlorine present in the filtered water and to ensure complete de-chlorination. This de-chlorinated is water passed through the softener to reduce the hardness and then passed through cartridge filter to remove the suspended solids, which may escape from up-steam units.
Reverse Osmosis (RO):
The filter water is fed to the Reverse Osmosis Plant, and the water passes through three RO units. The RO is a process for removing dissolved mineral salts, organic molecules and certain other impurities from water by forcing water under increased pressure to pass through a semi permeable membrane, from that RO system, water is fed to the EDI system. Electro De-ionization (EDI) System: Electro deionization (EDI) is a common sense evolution of conventional ion exchange technology. In EDI, just as in conventional ion exchange, cations and anions in the feed water are exchanged for
hydrogen and hydroxyl ions in the ion exchange resins, producing de-mineralized water. The key operational difference is that with EDI, the ion exchange resin is regenerated continuously, while with conventional ion exchange, chemical regeneration is performed intermittently. Continuous regeneration in EDI is achieved electrochemically by means of ion conducting membranes and an imposed electric current. The hydrogen and hydroxyl ions necessary for regeneration are formed in-situ, without the addition of chemical reagents, by means of the familiar water dissociation reaction, sometimes called water splitting:
H2O H+ + OHWith
EDI, feed water is fed through ion exchange resin in the diluting chambers bordered by anion- and cation-conducting membranes. At the same time, electrodes at each end of the unit impose an electric potential which drives the water splitting reaction and causes the ions in the ion exchange resins to migrate to the selectively permeable membranes, where they are transported into the adjacent concentrating chambers. Once in the concentrating chambers, the ions are carried away by the concentrate flow. Note that just as in conventional ion exchange, EDI benefits from the excellent mass transfer and de-ionizing characteristics of modern ion exchange resins.
ULTRA FILTRATION SYSTEM:
The EDI permeate water passed through the series of seven ultra filtration membranes and will take care of bacteria, pyrogens, Total Organic Carbon (TOC) etc. and is collected in Purified water Storage Tank. From this storage tank the purified water is passed through UV lamp. This water is again circulated and collected through return loop.
=Raw Water Raw Water Storage Tank Sodium hypo chlorite dosing Pressure
. Sand Filter
Reverse Osmosis Unit Micron Cartridge Filter Softener De – Chlorination Pre-Treatment Plant
EDI System EDI Permeate Water Storage Tank ULTRA FILTRATION (7 UF)
Purified water Plant
USER POINT UV TREATMENT STORAGE TANK
The validation of purified water generation shall be done in three phases. The purpose and sampling plan is described as below:
The initial phase (phase-I) typically begins only after successfully completion of operational qualification.
The water generated during the second phases will be used for the manufacturing as long as the water meets the specifications.
PHASE- I
During this phase daily samples were taken and analysed for chemical and microbiological quality. Sampling should be after each step in the treatment process and from each point of use. The incoming feed water will also be tested to verify the compliance with the specifications. The phase-I shall be performed for a minimum period of 30days.
At the end of this phase alert and action limits will be established. These alert and action limits will be used during phase-II and beyond.
The data obtained during phase-I should be used to develop the SOP and confirm that, the operational SOPs are adequate.
Alert and Action limits shall be calculated based on the phase-1 study.
PHASE- II
This phase is to demonstrate that the system consistently operates within predetermined operating ranges and delivers the water of the required quality (as specified) when operated in accordance with the SOPs.
The sampling plan will be the same as phase -I, and this activity will continue for 30 days after completion of phase-I.
PHASE- III
This phase will be continued for 10months to verify the extended performance of system procedures on the quantity and quality of water despite possible seasonal variations of feed water. At the end of this phase the performance qualification is considered as completed and on going monitoring
will be established a continuous record of water quality. This activity is under progress. During this phase purified water samples are collected daily from minimum one point of use, covering all points in a week.
157. What are the classifications of clean rooms?
Generally clean rooms are classified in to the following types as per different guidelines:
Schedule M: Grade A, Grade B, Grade C, Grade D
USFDA (US 209E): Class 1, Class 10, Class 100, Class 1000, Class 10000, Class 100,000
WHO 2002: Grade A, Grade B, Grade C, Grade D
EU GMP: Grade A, Grade B, Grade C, Grade D
ISO 14644-1: ISO-3, ISO-4, ISO-5, ISO-6, ISO-7, ISO-8, ISO-9
Britian (BS 5295): Class C, Class D, Class E or F, Class G or H, Class J, Class K
Australia (AS 1386): 0.035, 0.35, 3.5, 35, 350, 3500
Germany (VDI 2083): 1, 2, 3, 4, 5, 6
158. Which are used for cleaning agent in Pharmaceuticals industries. ?
- Floor Cleaning agent -0.25%/MH, 5%/GAL & 1.0%/GHC
Drain & Sinks use -2.5%/TC
Return riser, Plastic screen Strip, Glass (Windows &door)- 0.25%/MH Where- MH= Microclean-H, GAL=Germiclean Antiseptic Liquid
GHC=Germiclean Hospital Concentrate, TC=Torcilocid Concentrate
159. What is the leak Seal test Method. ?
- Hold Time – Time period of sample, kept in negative (Vacuum).
Initial delay – Time taken to reach the 100mm of Hg /133mbar.
Retention time – Time after which sample is exposed to atmospheric pressure.
Leak seal test for– Blister, Strip, Pouch pack & Bulk pack container.
Front view of Leak Seal test Apparatus– Lid of Desiccators
- Tap with rubber tube
- LCD display
- Control penal
Rear view of Leak Seal test Apparatus – Main switch ,inlet, fuse, main socket, print interface.
2-3 Drops of 5% W/V of methylene blue received from QC For Leak test. Morpholene Test for PVDC Layer identification (Yellow stains Observed) Vacuum : 000mm/mbar 060 s
Set : 381mm/mbar 060 s
Blister, strip, Pouch packing – 381mm of Hg /15 inch of Hg Bulk packing container – 508mm of Hg/ 20 inch of Hg The screen will be shown as :- Vacuum(mm/Hg) = -381
Hold Time (Sec.)= 060 Initial delay (Sec.)= 015 Retention time (Sec.)= 060
160. Which challenge test of metal detector of CVC M/C. ?
- Ferrous – 00mm , Non ferrous – 1.5mm, Stainless steel – 2.00mm
164. Which Test for the Steel SS 316L/304 identification?
- Molybdenum test
- Drop of the molybdenum reagent on the steel part
- Pass the current 9Ω
- If the pink or redish colour develop for more the 15 sec –SS 316L
- If the pink colour disappear with in 15 sec –SS 304
161. what is limit test of Microbial test ?
- Arobic Microbial Count – NMT 1000 cfu/g.
- Combined yeasts / Moulds count – NMT 100 cfu /
- Pathogens / Escherichia coli – Must be Absent
162. What is documentation?
- All the written production procedures, instructions and records, quality control procedures and recorded test results involved in the manufacturing of a medicinal product. What is the clean room?
- Clean rooms are defined as especially constructed, environmentally controlled enclosedspaces with respect to airborne particulates, temperature, humidity, air pressure, air flowpatterns, air motion, vibration, noise, viable (living organisms) and lighting.
Particulate control includes:
Particulate & microbial contamination Particulate concentration & dispersion
164. What is the difference between drug substance and drug product?
- Drug substance (API): Any substance or mixture of substances intended to be used in the manufacture of a drug (medicinal) product and that, when used in the production of a drug,becomes an active ingredient of the drug product. Such substances are intended to furnish
pharmacological activity or other direct effect in the diagnosis, cure, mitigation, treatment, or prevention of disease or to affect the structure and function of the body (Reference: ICH Q7A).
Drug product: The dosage form in the final immediate packaging intended for marketing (Reference: ICH Q7A).
- What is the difference between intermediate and drug substance (API)? Intermediate: A material produced during steps of the processing of an API that undergoes further molecular change or purifications before it become an API (Reference: ICH Q7A).
API: Any substance or mixture of substances intended to be used in the manufacturing of adrug (medicinal) product and that when used in the production of a drug, becomes an API ofthe drug product. Such substances are intended to furnish pharmacological activity or otherdirect effect in the diagnosis, cure, mitigation, treatment or prevention of disease or to affect the structure & function of the body (Reference: ICH Q7A).
166. Which Guideline follow for preparation of SMF?
- PIC/S and EU Guideline (Eudralex Volume-4).
Preparation: SMF is Prepared by Quality Assurance and Reviewed by Plant Head and Authorised by Head QA.
Contents of SMF:
- General Information
- Personnel
- Premises and Equipment
- Documentation
- Production
- Quality Control
- Contract Manufacture and Analysis
- Distribution, Complaints and Product
- Self Inspection
Review Period; Any changes after approval of SMF shall be recorded in Annexure-II for keeping a track of changes taken place. All such changes shall be collated and amended in the next revision.
Site Master File shall be revised at end of every calendar year or as and when required through change control management system.
Storage Period; Site Master File shall be store by QA department for 10 years.
167 . What is QM?
A.The quality manual is a statement of the Company’s Quality Policy and Quality Objectives
of the organization.
Which Guideline follow for preparation of QM.
Eudralex Volume 4 (Chapter – 1 Pharmaceuticals Quality System), ICH Q8, Q9 and Q10, Schedule M.
Contents of QM.
Introduction, Scope, Basics of Quality Management System Quality Policy, Quality Objective Quality Risk Management Policy Company Profile, Organization, Regulatory Basics Documentation For The Quality Management System
Document Structure Production of Quality Management System AccompanyingQualityManagement System
Design/Project Management, Qualification and Validation
Maintenance, Health requirements, Personnel hygiene requirements, including clothing Complaints, Product Recall, Customer Management
Product Documentation, LabelingAnd Packaging Control Product Quality Review, References
Review Period. Every Two Years
Storage Period. Perpetual
168. What is Definition of MARKET COMPLAINTS. ?
- A complaint is any expression of dissatisfaction with a product or service marketed. Any written/ genuine verbal communication received directly from any customer, retailer, distributor, healthcare professional, regulatory agency, patient (Consumer) or field staff,
regarding the safety, identity, strength, purity, efficacy, quality, shortages or any other such complaints shall be considered as a Market Complaint.
Critical Complaint:
A complaint that strongly indicates the purity, identity, safety or efficacy of a product may have been compromised and has the potential to cause a life threatening or serious health situation.
Major Complaint:
A complaint that indicates the purity, identity, safety or efficacy of a product may have been compromised, but does not present as a life threatening or serious health risk.
Minor Complaint:
A complaint that is neither critical nor serious
TIME LINES FOR INVESTIGATION:
Investigation shall be completed within 7 working days for critical complaint and 30 working days for Major/Minor (or as per Technical Agreement requirement or Regulatory Agency requirement where appropriate) and same shall be sent to marketing department immediately after investigation.
169. What is Definition of PRODUCT RECALL: ?
- Removal or correction of marketed products for the reasons relating to deficiencies in quality, safety or efficacy, including labeling considered to be in violation of the laws.
Wholesale Level: All distribution levels between the manufacturer and retailer.
Class I Recall: Notification and acknowledgement of receipt of recall notification within 24hrs.
Class II Recalls: Notification and acknowledgement of receipt of recall notification within 48 hours.
Class III Recalls: Notification and acknowledgement of receipt of recall notification within 5 days.
Mock recall shall be done to evaluate the effectiveness of arrangements periodically to recall the products from EU / US / Australia / other export markets and domestic markets. Mock recall is applicable only to markets where product is already marketed.
Frequency of Mock Recall shall be once in two years or as per MA Holder / Contract giver requirement.
- Which types of Air Sampling for micro? Active Air sampling by Air sampling Passive Air sampling by settle plate
Frequency: For Settle Plate: Once in a Month (Every first week of the month cover all the sampling point)
For Air sampling: Twice in a Month (Fortnightly) For Surface Monitoring: Once in a Month.
171. Difference between Settle Plate and Air sampling. ?
- Settle Plate – Passive Particle Air Sampling – Active sampling
Which Guideline follows: ISO 146441
Re-Qualification Frequency: 1 year ± 30 Days
172. What is Qualification ?
|
- Establishing documented evidence which provides a high degree of assurance that a specific process will consistently produce a product meeting its pre-determined specifications and quality attributes.
FAT (Factory Acceptance Test) vendor Visit |
SAT (Site Acceptance Test) |
IQ (Installation Qualification) |
OQ (Operational Qualification) |
PQ (Performance Qualification) |
173. What is compressed Air and why required ?
- Compressed air system is designed to supply oil free (Non–lubricated) compressed air to the various use points.
Make – Chicago Pneumatic. Capacity – 275 CFM (2 Nos Method for Compressed air test kit for air detector tube Testing parameter for detector tube of different test.
- Parameter for Water vapour
- Parameter for oil
- Parameter for Oxygen
- Parameter for Carbon
- Parameter for Carbon
- Parameter for Nitric oxide and Nitrogen
- Parameter for Sulfer
174. What is EQUIPMENT CLEANING PROCEDURE?
- Type C Cleaning
Criteria:-At the end of the shift when the same batch is to be continued on next day.
Type A Cleaning
Criteria:-1. Between batches of same product.
2.Between batches of lower strength to higher strength of the same product.
Type B Cleaning Criteria:
- Between batches of different
- Between batches of higher strength to lower strength of the same
- Change in colour irrespective of product and
- After any maintenance work relating product contact
NOTE:
By any circumstances if the cleaned equipment is not used within 48 hrs then the equipment shall be cleaned as per product change over cleaning prior to use.
- During continuous production/campaign production on the equipment, the equipment shall be cleaned as per product changeover cleaning after manufacturing of 10 batches
or 10 days which ever is earlier.
174. DIFFRENCE BEWTWEEN CHANGE CONTROL AND DEVIATION? A.
Change Control | Deviation |
It is permanent change forever. | It is particular change in Equip., Process, and Vendor. |
Always required back up data other wise not closed. | Back up not required. |
- DIFFRENCE BEWTWEEN SOP AND PROTOCOL?
SOP(s) Procedures are followed in routine for consistent work performance and quality out put of the product. | Protocols Procedures are documented for one time study to qualify or validate area/ equipment/ process/ system under study |
176. Which SOURCE OF DUST, DIRT & MICROBES ARE ? A.
Man Material Machine Environment
177. LINE / AREA CLEARANCE ?
- To ensure that there are no items, packaging components, residues of previous product & any other unwanted material on the line
Implications GMP Violation Mix-ups
Contaminations Cross contaminations Product Failure Market complaints
178. CONTAMINATION, CROSS CONTAMINATION AND MIX – UP? A.
CONTAMINATION :
In any product, presence of a substance other than product manufacturing formula is called contamination.
CROSS CONTAMINATION :
Contamination of one product to another is called cross contamination.
MIX – UP :
Undesirable mixing of material, product/ batch, unintentionally or accidently is called Mix- up.
179. Which TYPES OF PASS BOX ?
- Dynamic Pass Box
- Static Pass Box
DYNAMIC PASS BOX
For Material transfer from unclassified area to classified area. This Pass box having HEPA filter and UV Light
Frequency of Validation is every six month Test:
- Air Velocity
- Filter Integrity
- Particle count
STATIC PASS BOX
For Material transfer from classified area to classified area.
180. What are two types Methods for granulation ?
- Wet granulation method: In this granulation binder solution is used.
- Dry Granulation: Granulation is achieved with the help of mechanical compaction or
181. What is Definition of Tablets ?
- Definition of Tablets
Tablets can be defined as Solid Pharmaceutical Dosage form containing drug substances with or without suitable diluents and prepare either by compression or molding methods.
- There are various types of Tablets and abbreviations used in referring them are as
- Compressed Tablets (CT)
- Sugar-Coated Tablets (SCT)
- Film-Coated Tablets (FCT)
- Enteric-Coated Tablets (ECT)
- Multiple Compressed tablets (MCT)
- Layered Tablets, 5.2 Press-Coated
- Controlled Release
- Tablets for Solution / Dispersible
- Effervescent
- Compressed Suppositories or
- Buccal and Sublingual
- Vaginal
182. Why is Coating required ?
- The application of coating to Tablets, which is an additional step in the manufacturing process,
increases the cost of the product; therefore, the decision to coat a tablet is usually based on one or more of the following objectives
- To mask the taste, odour, and appearance of the
- To provide physical and chemical protection for the drug from atmospheric effects, temperature, humidity and light.
- Functional coating (Control release, enteric coat, sugar syrup coat).
- To protect the drug from the gastric environment of the stomach with an acid-resistant enteric
coating.
- To incorporate another drug or formula adjuvant in the coating to avoid chemical incompatibilities or to provide sequential drug release
- To improve the Pharmaceutical elegance by use of special colours and contrasting printing,
which improves the appearance of the product.
Types of Coating:-
- Sugar Coating
- Film Coating
- Compression Coating
- Sugar coating gives excellent appearance to the
- Sugar Coating process involves following steps:
- Sub
- (Smoothning)
- Finishing(Colour coating)
- Polishing
Defect of tablets during coating: Cracking , Twinning, Peeling, Logo Bridging,Sticking
183. What is DT time of Different Tablets. ? A.
Sr.no. | Type of tablet | Limit |
1. | Uncoated tablets | Not more than 15 min |
2. | Coated tablets | Not more than 60 min |
3. | Effervescent tablets | Not more than 05 min |
4. | Soluble tablets | Not more than 03 min |
5. | Dispersible tablets | Not more than 03 min |
6. | Orodispersible tablets | Not more than 03 min |
7. | Enteric coated tablets | In 0.1 M HCL for 2 hrs – No crack and In phosphate buffer solution pH 6.8 with NMT 60 min |
8. | Chewable tabs. | NA |
- How many types of DISSOLUTION? Types of dissolution test apparatus:
- Basket apparatus
- Paddle apparatus
- Reciprocating cylinder apparatus
- Flow- through cell
185. CONTENT OF ACTIVE INGREDIENT ?
- 1) Assay of Active
2) 20 tabs: – Limits 90% to 110%
186. UNIFORMITY OF WEIGHT/WT VARIATION ?
- 20 tabs, calculate wt. NMT 2 deviate, none twice the limits.
189. FRIABILITY TEST ?
- This test is additional to check crushing strength of tablet by this test one can check Capping & /or Lamination. USP limit is 0.5 to 1%. Rotation: – 25 rpm or 100 rotations in 4 min.
4 USP 36 – 905 UNIFORMITY OF DOSAGE
- UNIFORMITY OF CONTENT OR CONTENT UNIFORMITY ?
IP: – Active less than 10mg or 10%, BP: – Active less than 2 mg or 2%, USP: – Active less than 25mg or 25%.
-10 tabs limit NMT 1 tab deviate 85 – 115% & none outside 75 – 125% of the Avg. value/IP/BP/USP (Relative Standard Deviation less than or equal to 6%),
- If 2 or 3 individual values are outside the limits 85 – 115% of the value, & none outside 75 – 125% repeat for 20 tabs.
- Complies when 30 tabs NMT 3 of the individual values are outside the limit 85 – 115% of the Avg. value, and none outside 75 – 125%.
191. Which types defect of Tablets during Compression. ?
- Capping , Sticking, Picking, Mottling,
192. DIFFRENCE BEWTWEEN MOISTURE CONTENT AND LOD? A.
Water Content determined by the Karl fisher method and it consists of only i.e moisture content. The results does not contain other volatile matter concept the water.
Loss on drying (LOD) is determined by heating the sample bellow its melting point in an oven and it includes all volatile matter including water content and solvent.
Loss on Drying is an unspecific analytical technique removing not only water but all other volatie impurities like alcohal etc.from a sample.
The degree of drying is dependent on, Temprature
Drying time
LOD or Moisture content of pharmaceuitical products can include both bound (e.g. water of hydration ) and free water. In case there are addional traces of other volatile impurities present , like alcohl: LOD ma be higher than water content . in other cases, LOD may be lower than water content ,as bound crystalwater may not be removed by heating
%LOD = %water content – %Water molucule in API
193. What is the types of coating parameter. ?
- 1. Pan RPM (Pan speed)
- Inlet Air Temperature(°C)
- Exhaust Air Temperature (°C)
- Tablet Bed Temperature (°C)
- Inlet Air Flow (CFM)
- of Cycles
- Spray Rate (gm/min.)
- Atomization Air Pressure (Kg/cm²)
- Pattern Air Pressure (Kg/cm²)
Some Machines Type :- Auto coater , Pan size(Inch) , Nos. of spary gun (Nos.) , Nozzle diameter (mm.) , Types of baffles , Distance between gun to bed of tablets (cm) , Pan on time , pan off time.
194. Manufacturing Environment — A critical factor for product quality ?
- Temperature
- Humidity
- Light
- Air movement
- Pressure differential
- Microbial contamination
- Particulate contamination
195. Air cleanliness class (As per ISO 14644-1) ?
- ddf
EU-Guidelines Annexure-I
• FILTERS : Filters can be broadly classified as:
- Sieving filters
- Dynamic filters
- Electrostatic filter
(A) PREFILTER /PRIMARY FILTER:
- Normally placed in supply and return air line
- Protects fine & absolute filters
- Normally 10 to 20 micron down to 90 to 95%
- Pressure differential : 5 to 20 mm
MOC : synthetic non woven washable material
§ (B)INTERMEDIATE FILTER:-
Normally placed between primary and fine filter
§ Protects fine & absolute filters
- Normally 3 to 5 micron down to 95 to 99 %
- Pressure differential : 10 to 20 mm
MOC : synthetic non woven
- (C) FINE FILTERS : Normally located before air supply
§ Gives clean air & protects HEPA wherever applicable
- Efficiency of 99 % down to 1 micron
§ Pressure differential 6 mm to 25 mm
MOC : Synthetic non woven or Micro Layer fiber Glass
- (D) HEPA FILTERS : Terminally fitted in the supply duct
or in AHU supply / return air line
- Efficiency normally 99% down to 0.3 micron
- DOP penetration : 01 %
- Efficiency = 100 – penetration
- Pressure differential = Installation 15 to 20 mm
= Disposal 25 to 75 mm
MOC : Micronics Glass Fiber
Very Fine Glass Fiber filament ( 1 to 100µ diameter, 0.2 to 40 mm long)
- What is Procedure of challenge test Primary & Bulk (CVC Bulk line) ?
- Challenge test / Initial checks for sensor (PRIMARY AREA):- 1.Desiccant inserter Machine
- cotton/Rayon inserter Machine
- Rotary Capper / Inline Capper Machine:
- Missing Liner / Foil Sensor
- Loose/Cross cap (For inline Capper machine)
- Fallen Bottle (For Rotary capper )
4. Induction Cap sealer :
- Missing liner/ foil Sensor
- Fallen Bottle
5. Challenge test procedure for Metal detector:
- For Ferrous – 2mm Ferrous (for Countec) & 1.0mm (for CVC)
- For Non-Ferrous- 5mm
- For Stainless steel (SS)- 0mm
CHALLENGE TEST PROCEDURE AT SECONDARY AREA:
1. Pharmacode/Barcode/OCR on automatic Labeling machine:
- Put one extra bar on
- Merge two bar on
- Labeled bottle with out
- Merge two
- Merge 2D code
2. Track and trace system (optel):
- Merge bottom 2D
- Merge 2D code on Manual Aggregation 1:
- Less bottle in inner/case. Manual Aggregation 2:
- Less bottle in inner/case
3. Initial checks for sensor
- Label sensor
- Rejection verification sensor
4. Action in case of splice detection in printed label roll:
- Which types of dismantling parts of Blister ?
- Hopper , Linear vibrate plate , De-Dusting tray , De-Dusting hose pipe , Bowl disk , Insert , Channel / rotary Swipe brush/brush feeder box , Feeding zone guide track , forming unit(upper & lower) , Blister guide track , Sealing plate (upper & lower) , Sealing & cooling guide track , Performing unit , Punch index guide track , Punching unit , Pack guide assembly
, Pin hole detection unit (Alu.-Alu.) , Pin hole guide track (Alu.-Alu.) , Plug plate (Alu.-Alu.) De-Blistering parts: Blister entry guide , Product collection tray , Product recovery guide , Upper & Lower roller & Acrylic guards.
- Which are the challenge test of blister?
A. (PRIMARY AREA)
Camera challenge test:
- To check empty pocket
- To check broken tablets/Capsules
- To check overlapping tablets/capsules
- To check black particles tablets/capsules
- To check different colour tablets/capsules
Checkweigher challenge test :
- One blisters / strips more in carton
- One blisters / strips less in carton
- Insert missing in carton
- Double insert in carton
Leak test for blister/strip:
Rejection verification sensor:
- To check rejection verification sensor
Challenge test for PVDC:
- Take out Blank sample and pour few drops of morpholine Solution, if yellowish brown colour appears then confirm PVDC layer is present on either side.
Challenge test procedure for pinhole. Challenge test procedure for splice Detection:
- For Lidding foil
- For Base foil
Challenge test procedure for Pharmacode on foil:
- Extra Bar on foil
- Marge two bars on foil
(SECONDARY AREA)
Challenge test :
Pharmacode on carton:
- One extra Bar on carton
- Marge two Bars on cartons
Pharmacode on Leaflet / Insert / Booklet:
- One extra Bar on Leaflet / Insert / Booklet
- Marge two Bars Leaflet / Insert / Booklet
Stack level Sensor Challenge test:
- Remove the one blister against standard fill value from autocartonator bucket before stack level sensor.
Challenge test for Leaflet / Insert presence :
Challenge test for Empty cartons:
Challenge test for Track and trace machine:
- Smudge Data Matrix
- Smudge characters
- Unprinted cartons rejection
- Continuous carton
Calculate the limit as per blow formula and take that as a upper and lower limit. For example.
If the least component average weight is 0.9gm and checkweigher accuracG K of Pharma – Copy (2)y is 0.2gm for
that upper & lower limit as:
= Average weight of least component + checkweigher accuracy
2
= 0.9+0.2
2
= 0.55gm
Lower & upper limit – ±0.55gm