Your cart is currently empty!
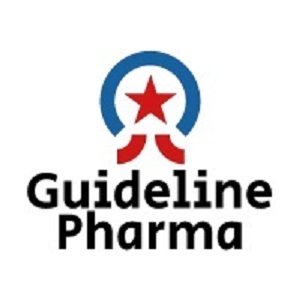
Good Documentation Practices
Good Documentation Practices
OBJECTIVE:
To lay down a procedure to describe the steps to be followed for good documentation practices; and ensure that each personnel receives clear and detailed description of the relevant job assignment to minimize the risk of misinterpretation and error.
PROCEDURE :
- Principle: Good Documentation constitutes an essential part of the Quality Assurance system and is related to all aspects of GMP.
- Mention time in hours in documents. For example afternoon 1:30 PM; write as 13:30 hours. Change the date after 24:00 hours.
- Write the date in the following manner
DD/MM/YY or YYYY
Where DD indicates the date
MM indicates month
YY or YYYY indicates the year
For example, write 1st January 2023 as 01/01/23 Sign all master documents and control documents using a blue ink ball pen only.
Enter information in records, logs, and documents using a blue ink ball pen only for all employees, except IPQA. Do not use a pencil for any entries or recording of data.
IPQA uses the black ink ball pen for the recording of data in process control during manufacturing and packing activity.
Do not overwrite to correct any error on a document. Strictly avoid the use of white ink to correct any error on a document. To correct any error on a document, strike off the error with a single line in such a manner that the original entry is readable. Write the corrected entry close to the original entry, sign, and date. Where appropriate, record the reason for alteration.
Design and prepare documents in an orderly fashion and in accordance with the standards in such a way that they are easy to check.
Appropriate and authorized persons must approve documents. Sign all documents with the same signatures as done in the specimen signature register
Follow the applicable change control procedure for changes in documents. If documents are required to be discontinued handle the same through change control.
Review documents regularly according to their defined review period and keep them up-to-date.
Where documents require the entry of data, make entries in clear, legible, indelible handwriting. Provide sufficient space for such entries.
Where space is void, cross it with a single line across the void space in such a manner that no entries can be made at a later stage, and write NA with the date & sign.
Complete the record at the time each action is taken in such a way that all significant activities concerning the manufacture of medicinal products are traceable.
Compile all the pages of records and documents along with necessary attachments in chronological order in the file.
Reproduced documents must be clear and legible. The reproduction of working documents from master documents must not allow any error to be introduced through the reproduction process.
Maintain records for the distribution of documents.
Protect documents against accidental and malicious damage. Store documentation and associated information in a safe and secure manner.