Your cart is currently empty!
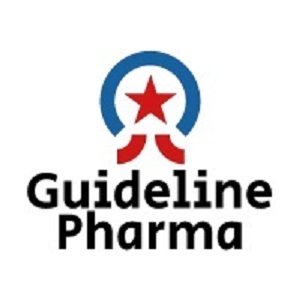
Deviation Control
Deviation Control
OBJECTIVE:
To lay down the procedure to describe the steps to be followed in case of planned/unplanned deviation from the standardized activity, or standard procedure.
PROCEDURE :
Deviations are of two types: Planned & Unplanned.
Planned Deviation: Any Deviation in the procedure, process, equipment, or standard batch size which is planned, documented, assessed for its impact on product quality, and authorized in advance, with the agreement of all concerned is termed as planned deviation.
Unplanned Deviations (Unforeseen Deviations): While carrying out day-to-day activities, there are chances of unplanned deviations and events to occur. These deviations are unforeseen, accidental and shall occur due to several reasons:
- Equipment failure/breakdowns/malfunctioning
- Power Supply failures / Interruption
- Accident/ Mishap in the plant.
- Breakdown in support services/ utilities
- Any other unforeseen situation (e.g: Production process parameters, HVAC system, Water system, equipment/instrument calibration, environment control, storage conditions, analytical test procedures, etc.)
Any deviation needs to be authorized by Head QA in writing.
For any deviation, intimate QA with an intimation slip for issuance of the Deviation Control Form.
QA to issue the form with a serial number as DV/XX/YYY, where
- DV- denotes Deviation,
- XX – two last digits of the year,
- YYY – Serial number.
The initiating department has to write the description of the deviation. QA should give immediate action to be taken on the deviation. The initiator department should give the root cause for the deviation & justification of the same.
The form has to be forwarded to QA where the Head of QA looks into it through risk assessment to evaluate the impact of deviation on the quality of other products.
The QA Head also looks into the regulatory aspect of it & based on it gives acceptance to the deviation.
The QA Head should discuss with the initiator department’s head the requirement of any CAPA to avoid the recurrence of the same and decision for disposition to be taken.
All of the above has to be recorded in the Deviation Control form with respective signatures.
The investigation of the deviations shall be completed within 30 calendar days. If not completed, then an interim report justifying the delay is to be prepared every 30 days until the investigation is closed.
The original Deviation Control form remains with QA & a copy was given to the initiator department to attach it with the concerned records (if required).