Your cart is currently empty!
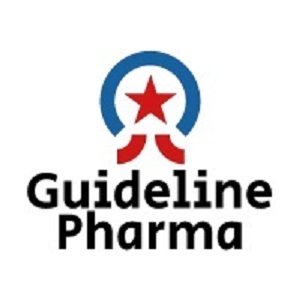
Corrective and preventive action
Corrective and preventive action
OBJECTIVE :
To lay down a standard procedure for corrective and preventive action(s) system related to product quality/system attributes.
PROCEDURE :
Definitions:
Corrective action:
Action is taken to eliminate the root cause of an existing non – conformity, defect, or other undesirable situation in order to prevent a recurrence.
Preventive Action:
Action is taken to eliminate the root cause of potential nonconformity, defect, or other undesirable situations in order to prevent occurrence.
In case of any deviation (wherever applicable) or any abnormality as mentioned in the scope, the concerned department will inform the QA department to issue the CAPA form.
Each department shall record the details of product/quality attributes identified from any of the above sources in CAPA form.
All product quality/system attributes shall be identified and analyzed. The source of product and quality problems could be the following but not limited –
- Incidents
- Technology transfer document
- Deviations (planned / Unplanned)
- Annual product review
- Product complaints
- Change controls
- Out of Specification results
- Out of trends
- Risk assessment
- QC Stability reports
- Product recalls
- Warehousing
- Batch Failure
- Returned goods
- Self-Audits
- Other non – conformances
- Regulatory audit and commitments
- Audit by the contract giver
QA Department should allot the CAPA No. and record the same in CAPA Log.
QA person makes an entry into the log and allows CAPA control number which is made up as follows:
CYY/XX/XXX
1st character is C, which is an abbreviation for CAPA.
2nd and 3rd characters are numerical which indicates the last digit of the current year.
4th character is “/”
5th and 6th characters are department codes
7th character is “/”
8th, 9th, and 10th characters are sequential numbers commencing from 001 for each department.
e.g. C23/PD/001 indicates CAPA belongs to the Production department whose sequential number is 001 of the year 2023.
Classify the relevant events based on their potential impact.
Major event:
An event, which may have an impact on product quality or on the information, has been disclosed to regulatory authorities.
An event, which may affect multiple products or multiple lots of the same product.
An event may implicate already released product batches.
Repeated occurrences of the same minor events.
A major cGMP violation.
Minor event:
An event, with no or low impact on product quality.
An event, with no impact on the information, has been filed with the authorities.
A procedural deviation where other supporting data exists.
An easily correctible issue by the originating department.
Record immediate remedial action, corrective actions, Investigation details, root cause identification, and evaluation of remedial action on other sources followed by preventive action and their evaluation.
Based on the type of non – conformance, QA Head shall designate a team based on knowledge and skills, for carrying out the investigation.
Carry out the investigation to identify the root cause and its impact on the product quality and other products/systems and record in CAPA form.
Appropriate statistical and non-statistical techniques shall be used to analyze the impact on product quality / other systems.
Document all suggested corrective action(s) and preventive action(s) along with the target completion date and responsibility.
The root cause should be identified on a fact-based & whenever possible supported with data.
The impact of the event should be identified on all the factors evaluated.
Timelines for CAPA procedures:
In case of Major events, the activity or product should not be taken before completing the CAPA procedure. The timeline for completing the major event is 15 days.
In the case of Minor events, the timeline for completing the minor event is 30 days.
QA person shall verify all suggested corrective action(s) and evaluate preventive action(s) which are implemented in a timely manner and documented appropriately.
All the CAPA-related events should be regularly trended.