Your cart is currently empty!
Worst-Case in Cleaning Validation
Worst-Case in Cleaning Validation: Understanding the Importance and Implications
Cleaning validation is a critical aspect of pharmaceutical manufacturing and other industries where cleanliness is essential for product safety and quality. It ensures that equipment and surfaces are effectively cleaned, removing residues from previous batches and minimizing the risk of cross-contamination. Worst-case scenario analysis is an integral part of cleaning validation, aimed at identifying the most challenging conditions that could potentially compromise the cleaning process. This blog post explores the concept of worst-case cleaning validation, its significance, challenges in determining worst-case conditions, and best practices for successful implementation.
- The Significance of Worst Case in Cleaning Validation
Worst case analysis is crucial in cleaning validation because it helps ensure that cleaning procedures are robust enough to consistently achieve acceptable levels of cleanliness. Identifying worst-case conditions allows manufacturers to validate cleaning procedures under the most challenging scenarios, ensuring that even under these circumstances, residues are effectively removed.
By assessing worst-case scenarios, manufacturers can mitigate the risk of cross-contamination, product adulteration, and potential adverse effects on patient safety. Identifying and addressing worst-case conditions helps establish cleaning limits, determine appropriate sampling and analytical methods, and design cleaning procedures that are capable of consistently achieving the desired level of cleanliness.
Auditing in the Pharmaceuticals Industry
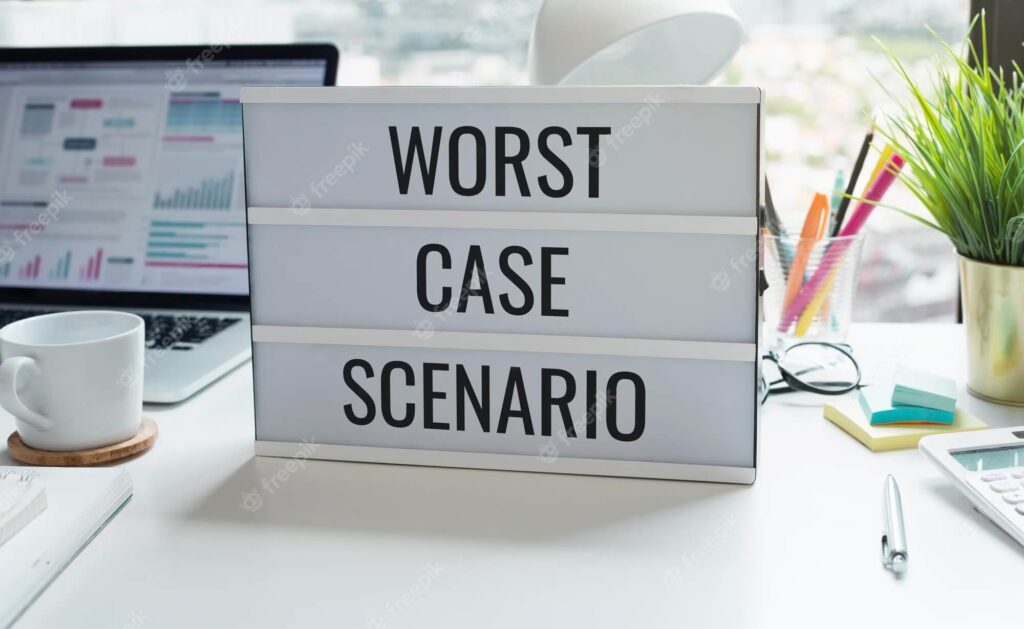
Challenges in Determining Worst-Case Conditions
Determining worst-case conditions in cleaning validation can be challenging due to the complex nature of manufacturing processes and the variety of residues and equipment involved. Several factors contribute to the difficulty of accurately identifying worst-case scenarios:
- Equipment and Surface Variability: Manufacturing equipment and surfaces can vary in terms of material, design, and accessibility. Analyzing worst-case scenarios requires considering the impact of different surfaces and equipment configurations on residue removal.
- Residue Characteristics: Residues can vary in their nature, such as being organic, inorganic, or a combination of both. Different residues may have varying solubilities and may adhere differently to surfaces, making it challenging to predict the most difficult residues to clean.
- Batch-to-Batch Variability: Each batch of a product may have unique characteristics that can influence the cleaning process. Variations in formulation, batch size, and production conditions need to be considered when determining worst-case conditions.
- Analytical Methods: The sensitivity and selectivity of analytical methods used for residue detection and quantification can affect the identification of worst-case conditions. The ability to detect low levels of residues accurately is crucial in determining the effectiveness of cleaning procedures.
Best Practices for Determining Worst-Case Conditions
While the identification of worst-case conditions can be challenging, several best practices can help ensure a robust and comprehensive approach to worst-case analysis in cleaning validation:
- Risk Assessment: Conduct a risk assessment to identify potential worst-case scenarios based on factors such as the toxicity of residues, shared equipment usage, product carryover potential, and patient risk. This systematic approach helps prioritize critical factors for worst-case analysis.
- Selection of Representative Residues: Choose residues that are representative of the range of residues expected in the manufacturing process. Consider factors such as solubility, detectability, and potential impact on product quality.
- Equipment and Surface Evaluation: Evaluate different equipment and surface materials used in the manufacturing process to determine their impact on residue adherence and removal. Consider the accessibility of hard-to-clean areas and the impact of surface roughness on cleaning effectiveness.
- Process Parameters: Assess process parameters such as cleaning agents, time, temperature, and mechanical action to determine their influence on residue removal. Establish worst-case combinations of these parameters based on scientific knowledge and experience.
- Sampling Locations: Identify the most challenging locations for residue detection. These areas may include crevices, dead spaces, and areas difficult to access during cleaning. Sample