Your cart is currently empty!
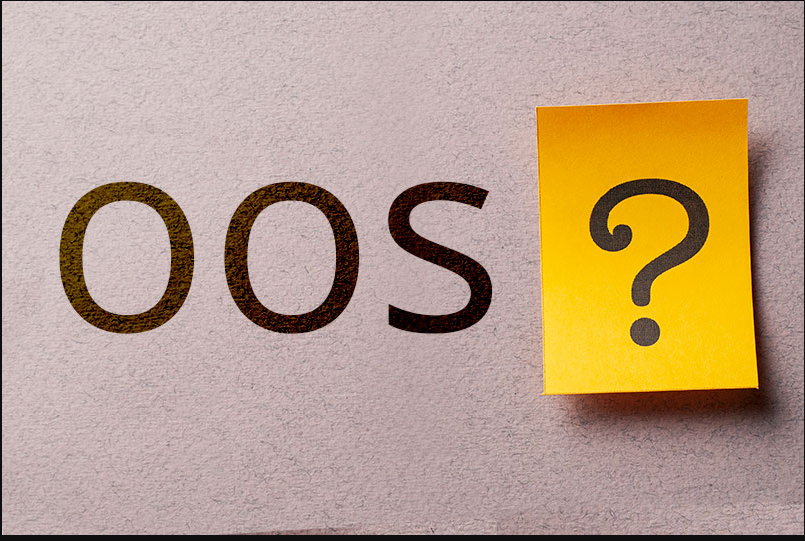
SOP for Out of Specification (OOS)
SOP for Out of Specification (OOS)
SOP for the procedure for handling, investigating, and reporting test results, which do not meet the specification.
This SOP is applicable to all out of specification results during the analysis of raw materials, packaging material, finished products, stability study samples, and any unusual results observed for test parameters
This SOP is not applicable that having lower or higher limits of raw materials, packaging material, finished product, stability study samples to the formulation.
SOP Procedure:
For Finished Products:
OOS results obtained are categorized into three general categories:
Laboratory Error.
Non-process-related or operator error.
Process-related or manufacturing error.
OOS results handling process is divided as follows:
OOS identification and reporting.
OOS investigation.
Phase-I Investigation: Investigation by the analyst and Section Head / Quality Control Head.
Phase-II investigation: Investigation and subsequent actions by Quality Control Head.
Conclusive error retest.
Inconclusive error retest.
Resampling.
Phase-III investigation: Investigation in production.
Corrective and preventive actions.
When an individual test result does not meet the specifications, it need not necessarily indicate that the batch has failed.
Action to be taken by Analyst (OOS Reporting):
When any OOS test result is obtained, inform the OOS to the section head along with the remarks.
All solutions and standards shall be preserved and properly stored for investigation.
An investigation by the Section head / Department head. (Phase-I Investigation):
The investigation of the OOS shall be started immediately by the section head or department head along with an analyst in consideration of the following points:
Carry out the assessment of the OOS result as soon as the result is reported.
Examine the test data sheet and accompanying attachments in order to find out whether the results can be attributed to laboratory errors.
Check whether the documented method has been followed in every detail. Check against specifications / SOP / MOA.
When instruments have been used, check whether they have been calibrated and were suitable at the time of use.
Determine that appropriate reference standards, solvents, reagents, and other solutions were used and that they meet quality control requirements.
Check all test preparations and check the raw data for any clear mistakes such as incorrect preparation, dilution, injection, or storage in inappropriate environmental conditions. Also check if the containers of a sample are incorrectly closed, improperly sampled, and improperly stored.
Investigate the other observations such as the use of different diluents, filters, reagents, etc.
Check for the loss of reagents or solutions during preparations.
Check for unusual or unexpected responses for standard or test preparations.
Check whether any deviations had been noted during the time of analysis and whether they were recorded in the TDS.
Record all the observations using a checklist for investigation of out of specification.
The laboratory head is responsible for a final decision as to the disposition or acceptance of the result.
Arrange for the re-examination of actual test preparations used by the analyst and to the extent possible, the glassware used in the original testing.
Evaluate the performance of the testing method to ensure that it is performing according to the authorized documents (Specification / SOP / MOP).
Section head shall investigate the suspected error and if the error found is genuine then the OOS result must be immediately invalidated after appropriate documentation.
In case no error is identified, results will be communicated to QA & further investigation shall be conducted upon approval from QA personnel.
QA responsible shall intimate Qualified Person where European batches are involved.
Action to be taken by Functional head / Department head. (Phase II Investigation):
The situation I: (Conclusive error retest):
If a clear error has occurred, arrange for the retesting of the second aliquot of the same sample solution or aliquot prepared from the same portion of the original sample by the same analyst in triplicate (In case of errors related to dilutions, instrument setting, single analysis to be performed.)
If all the three results of retesting are within the specification, average it, and substitute the average result for the initial test result (ensure that the averaged results are within the proven and acceptable range), but record it along with an explanation for the initial analysis failure (Genuine lab error – reversible error).
Invalidate and disregard the previous results on knowing the probable cause of the error.
Record the observations with signature. Retain all the data together.
Statistical Acceptance Criteria:
The percentage RSD of 3 replicate determinations shall not exceed the established precision for the test.
If the section head and analyst’s investigation is inconclusive then follow situation II.
Situation II: (Inconclusive error retest):
If the result of retesting is outside the specification and there is no clear error, arrange for the prompt retesting in 5 replicates by a 2nd analyst (with higher experience in testing) using the additional portion of the original sample.
If required, arrange for analysis of the previously approved material simultaneously for confirmation of reanalysis.
Involve Quality Assurance and Production to look at the quality trend of other batches for the same test to have an idea of whether the results of the earlier batches are within the proven and established range.
If the results of retesting (5 replicates) by the 2nd analyst are individually within the specification, substitute the average of these results for the initial test results of the 1st analyst (ensure that the average results are within the proven and acceptable range) and consider them for any decision on batch release, after investigating the cause of the failure of initial results. (Genuine lab error – reversible error).
Invalidate and disregard the previous results on ascertaining the cause of the error (sample integrity being biased), and document the investigation with the signature.
If the results of retesting (5 replicates) by the 2nd analyst are outside the specification, report all the results.
It may still be possible that the sample is biased and has laid to the failing results. Retain all the data together.
Statistical Acceptance Criteria:
The percentage RSD of 5 replicate determinations shall not exceed the established precision for the test.
Re-sampling:
Situation III: (Investigation of sampling procedure and sample integrity Homogeneity and representative portion)
When the initial test and retest on the same sample produce the OOS results, determine whether it is possible that the original sample was non-representative of the whole lot and requires re-sampling.
Before the re-sampling activity, it shall be conclusively proved that the original sample was non-representative, and also the sampling procedure shall be thoroughly reviewed.
Re-sampling is performed under the authority of the quality control head and quality assurance if the investigation reveals that the integrity of the sample is affected, in such a situation a portion of the fresh sample from the warehouse/manufacturing department is subjected to reanalysis by an experienced analyst in 5 replicates.
If the results (5 replicates) are in conformance to the specification individually, the batch may be released (ensure that the average results are within the proven and acceptable range) Investigation into sampling error is to be documented. Retain all the data on retesting and re-sampling together.
Situation III is not applicable to the content uniformity and dissolution test.
If in a situation where re-sampling does not meet specifications it is not reversible classification. Retesting for OOS stops here, which has to go for a full-scale investigation into manufacturing or processing through Quality Assurance and Production /Process Development?
Statistical Acceptance Criteria:
The percentage RSD of 5 replicates determination shall not exceed the established precision for the test.
Handling out-of-specification results in production (Phase III Investigation):
On receipt of the OOS report from Quality Control, review the report to know the details of the rejection.
Involve the Production and Process Development Department in the investigation.
Review the Quality trends for the product in order to know the extent of deviation from the regular manufactured batch.
Review the batch record and another supporting document for the following:
Authorized changes, if any.
Deviations from the standard process.
Quality of the input materials (whether released on any authorization).
Yields in comparison with regular approved batches.
Time delays, if any.
Change in facility/equipment, if any.
Breakdown of the equipment.
Calibrations of equipment where necessary.
Improperly validated process.
Production operator error.
Improperly functioning equipment/services
Improperly functioning components like pressure gauge/temperature gauge.
Extend the investigation to other batches.
Get any additional testing done in consultation with process development on the product if necessary.
Based on the review of the above data ascertain the reason for the failure.
Record the observation and findings.
Indicate the proposed action for the batch and the action plan for future batches.
Get the investigation report signed by Production, Quality Assurance, Process Development, and G.M formulations.
Based on the proposed action suggested following the Change Control Procedure
Corrective measures/actions to be taken:
Re-training to the 1st analyst to perform the test, if a laboratory error has occurred and the same shall be documented.
If the testing procedure/sampling procedure needs updating, it shall be done promptly with due analytical method validation and all concerned shall be informed.
Refer flow sheet of OOS LOGIC TREE for guidance.
For Raw Materials, Packaging Materials, and Stability study samples:
Follow the above steps.
If the result of retesting is outside the specification and there is no clear error, arrange for the prompt retesting in duplicate by the same analyst using the additional portion of the original sample.
If required, arrange for analysis of the previously approved material simultaneously for confirmation of reanalysis.
If the results of retesting in duplicates by the same analyst are individually within the specification, substitute the average of these results for the initial test results. (Ensure that the average results are within the proven and acceptable range) and consider them for any decision on batch release, after investigating the cause of the failure of initial results. (Genuine lab error – reversible error).
Invalidate and disregard the previous results on ascertaining the cause of the error, and document the investigation with the signature.
If the results of retesting (Duplicates) by the same analyst are outside the specification and if the previously approved material is found to be complying with the specification values & the reanalysis results are comparable to the initial analysis, then report all the results and it shall be concluded that the OOS is due to the product failure & not a laboratory error.
All OOS Investigations shall be completed within 30 working days unless otherwise justified.
Maintain a record of all OOS in the log book.
OOS No. Shall be given as OOS/XX/YY where OOS is for Out of specification, XX is for S. No, and Y is for the current year.
In the case of products manufactured for Europe distribution, a Qualified Person (QP) shall decide further CAPA and batch disposition-related decisions.
If no probable root cause / assignable root cause is identified, based on the original/initial results of the product and retest results of the sample Head – QA / designee or Qualified Person (QP) where Europe batch is involved shall decide the batch disposition decision.
In such circumstances, the efforts put into investigation shall be precisely documented, where feasible most probable root cause to be assigned, and appropriate corrective and preventive action to be defined.
Product disposition statement shall be recorded either by Head – QA or Qualified Person (In case of Europe product) in the investigation summary report.
The investigation shall be concluded 45 days from the date of initiation.
Respective batch and other affected batches or products if any, shall be quarantined until the decision is drawn by Head-QA / QP in the case of Europe.