Your cart is currently empty!
Sampling Plan in Cleaning Validation
Sampling Plan in Cleaning Validation: Ensuring Effective Contamination Control
Cleaning validation is a critical process in the pharmaceutical and healthcare industries to ensure that equipment, surfaces, and facilities are effectively cleaned and free from product residues, contaminants, and microbial agents. A well-designed sampling plan is an integral part of the cleaning validation process, allowing for representative sampling and accurate assessment of cleanliness levels. In this blog post, we will explore the significance of sampling plans in cleaning validation, their objectives, key considerations, and best practices for developing an effective sampling plan.
- Importance of Sampling in Cleaning Validation
- Assessing Cleanliness: Sampling is crucial for assessing the effectiveness of cleaning procedures. By collecting samples from critical surfaces and equipment, the presence of residual contaminants, active ingredients, detergents, or microbial agents can be detected. A robust sampling plan enables accurate measurement and analysis of the cleaning process’s efficiency and helps identify areas that may require improvement.
- Regulatory Compliance: Pharmaceutical and healthcare industries are subject to stringent regulatory guidelines and standards, such as those set by regulatory authorities like the Food and Drug Administration (FDA). Sampling plans help demonstrate compliance with these regulations by providing evidence of the cleaning validation process, ensuring product quality, and maintaining patient safety.
- Risk Mitigation: Effective sampling plans help mitigate risks associated with product contamination and cross-contamination. By ensuring representative sampling, potential sources of contamination can be identified and addressed promptly. This reduces the risk of product quality issues, adverse effects on patients, and regulatory non-compliance.
- Designing a Sampling Plan
- Sampling Locations: Identifying critical sampling locations is a crucial step in designing a sampling plan. These locations should represent the most challenging areas to clean, areas prone to product residues or microbial contamination, and surfaces that come into direct contact with the product. Examples may include product contact surfaces, equipment crevices, seals, and areas difficult to access during cleaning.
- Sample Size and Frequency: Determining the appropriate sample size and frequency is essential to ensure statistically valid results. Factors such as equipment size, surface area, and the nature of residues dictate the number of samples required. Statistical methods, such as Acceptable Quality Limit (AQL) or sampling plans based on confidence levels, can aid in determining the appropriate sample size and frequency.
- Sampling Techniques: Choosing the right sampling technique is critical to ensure representative samples. Various techniques, including swab sampling, rinse sampling, direct surface sampling, and air sampling, can be employed depending on the nature of the surface and the contaminants of concern. Each technique has its advantages and limitations, and the selection should be based on scientific rationale and industry best practices.
- Acceptance Criteria: Defining acceptance criteria for cleanliness levels is crucial to determine the adequacy of the cleaning process. Acceptance criteria should be based on scientific data, regulatory requirements, and product-specific considerations. It is essential to set appropriate limits for residues, contaminants, or microbial agents to ensure product quality and patient safety.
Validation in Pharmaceuticals: Ensuring Quality, Safety, and Compliance
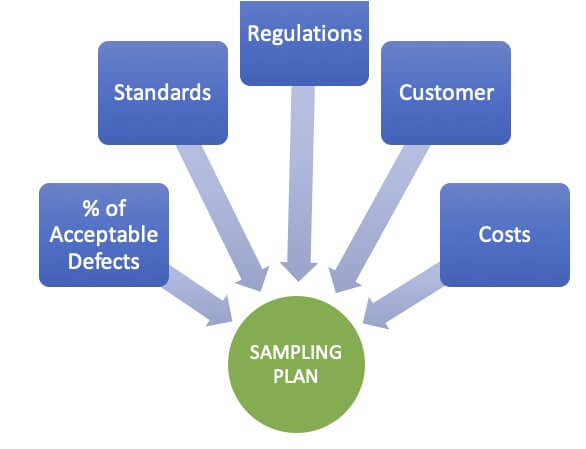
Best Practices and Challenges for Sampling Plan in Cleaning Validation
- Good Manufacturing Practices (GMP) and Industry Guidelines: Adhering to Good Manufacturing Practices and industry guidelines is essential for developing an effective sampling plan. These guidelines provide valuable insights into sampling methods, acceptance criteria, and statistical approaches. Following established best practices ensures regulatory compliance and facilitates industry-standard approaches to cleaning validation.
- Training and Expertise: Sampling plan execution requires skilled personnel with adequate training and expertise. Personnel responsible for sample collection should be trained in sampling techniques, handling of sampling equipment, proper documentation, and adherence to safety protocols. Regular training and refresher programs help ensure consistency and reliability in sampling practices.
- Interpreting and Reporting Results: Interpretation of sampling results requires a scientific and risk-based approach. Results should be thoroughly analysed, and any deviations or trends identified promptly. Accurate and detailed reporting of sampling results, along with appropriate documentation, ensures transparency, facilitates decision-making, and supports compliance with regulatory requirements.
- Challenges in Sampling: Sampling for cleaning validation may present challenges due to the nature of residues, surface characteristics, equipment design, and limitations of sampling techniques. Factors such as sample representativeness, detection limits, sampling errors, and equipment accessibility can impact the reliability of sampling results. It is important to address these challenges through careful planning, validation of sampling methods, and ongoing process improvements.
Conclusion of Sampling Plan in Cleaning Validation
Sampling plans are crucial components of the cleaning validation process in the pharmaceutical and healthcare industries. They enable the assessment of cleanliness levels, compliance with regulatory requirements, and effective contamination control. By carefully designing sampling plans, considering critical sampling locations, sample size, frequency, and appropriate techniques, pharmaceutical companies can ensure representative sampling and accurate evaluation of cleaning processes. Adhering to industry best practices, addressing challenges, and leveraging expertise in interpreting and reporting sampling results will ultimately enhance product quality, patient safety, and regulatory compliance in cleaning validation efforts.