Your cart is currently empty!
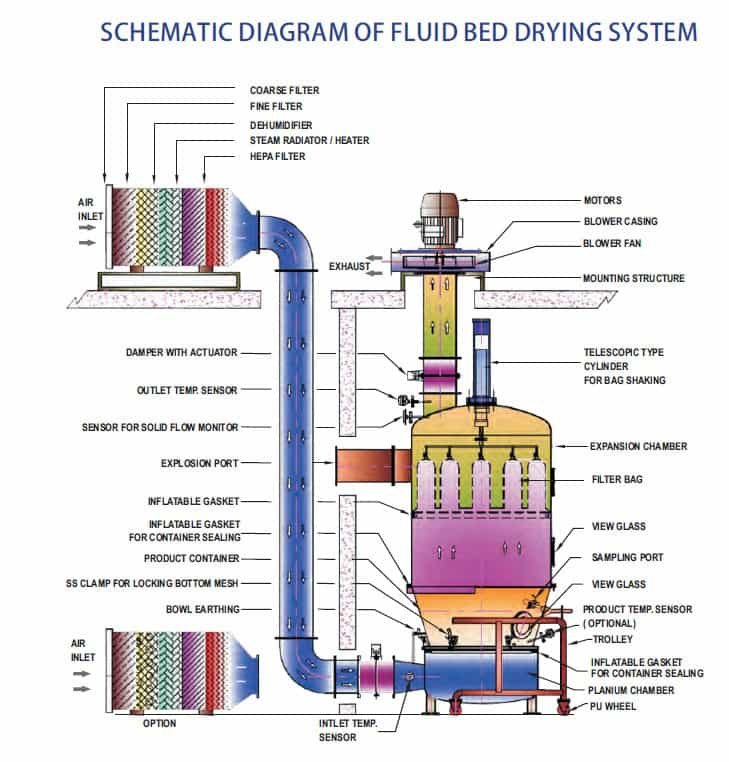
Operational Qualification of Fluid Bed Processor In Pharma
Operational Qualification of Fluid Bed Processor In Pharma
Operational qualification is the process of demonstrating that Fluid Bed Processor will function according to its operational specification in the selected environment. All the operation of Fluid Bed Processor t is verified by performing the test functions,• A conclusion is drawn regarding the operation of Fluid Bed Processor after the test functions are checked and all data has been analyzed. Verifies correct operation of critical components and operating ranges as defined by the specification and required performance.
- Control System
- Instruments
- Mechanical Features
- Operational Tests
- Empty Chamber Mapping
- Component Operation
Operational Qualification of Fluid Bed Processor protocol contains the following mentioned point
1.Purpose
2.Scope
3.Responsibilities
4.Procedure
5.Operational qualification tests
- Testing of Programmable Logic Controller’s Processor
- Verification of Man Machine Interface Screens – MMI
- Power & Emergency Failure Recovery Verification
- Emergency Operation Verification
- Verification of Alarms
- Operational Qualification Tests Status
6.List of Standard Operating Procedures
7. Data Analysis , Summary of OQ & Recommendations
8.Amendment record
9. Conclusion
1.PURPOSE:
To describe the Operational Qualification of Fluid Bed Processor, its accessories and to define the specification of the system in order to:
- To ensure that the equipment meets the Operational/Design limits as per user requirements.
- To Ensure that the equipment will be operationally qualified in accordance with good Manufacturing Practices.
2.SCOPE:
- The scope of Operational Qualification applies to the operational qualification of Fluid Bed Processor and its accessories to be installed.
3.RESPONSIBILITIES:
- It is the responsibility of the Manufacturer to prepare the Operational qualification protocol and identify the test parameters to be studied for qualifying the Fluid Bed Processor operationally.
- It is the responsibility of the client to check and approve the Operational qualification protocol.
- It is the responsibility of the Manufacturer to perform all the tests with respect to Operational qualification and compiling data in co-ordination with client.
4.PROCEDURE:
The following requirement / practices apply to FLUID BED PROCESSOR Operational Qualification activities:
- To verify the components design parameters.
- Review the preventive maintenance procedures, cleaning procedures and general operational procedure to ensure that they are comprehensive for reliable performance of the equipment.
5.OPERATIONAL QUALIFICATION TESTS:
The table below lists the tests to be performed as part of the Operational Qualification phase.
CRITICAL FEATURE |
Testing of Programmable Logic Controller’s Processor |
Verification of Man Machine Interface Screens – MMI |
Power & Emergency Failure Recovery Verification |
Emergency Operation Verification |
Verification of Alarms |
Testing of Programmable Logic Controller’s Processor
Rationale –
To verify the normal operation of PLC Processor by observing the processor module’s LED status indicator after turning on the PLC.
Test Equipment – None required.
Procedure –
- Turn panel power to ON position
- Turn PLC power to ON position
- Check that PLC Processor is in RUN Mode
- Document the following indicators located on PLC front panel
Acceptance Criteria – The processor should function as specified in the verification table.
Verification results –
Indicator | Specified | Actual |
Power LED | LED on when PLC power applied | |
Run LED | LED on when PLC is in RUN Mode | |
Error LED | LED on when PLC is in error | |
If actual result is not like expected result turn power to panel “OFF” and notify to engineer. Document any discrepancies on the operational qualification deviation report. |
Verification of Man Machine Interface Screens – MMI (PC Control)
Rationale – To verify that the screens displayed by the MMI according to the system requirements.
Test Required – None Required
Procedure –
Access the MMI and verify that all of the functions on each of the screens listed below confirm to the Manual.
Record the results for each verification on test data sheets.
Acceptance Criteria – The system shall operate as per design specification.
Results: MMI screen verification
Simulate | Procedure | Excepted Result |
Start Up Screen | This screen will displayed whenever the PC controls system starts | Operator station will Display the Start Up screen at the startup. |
Password Check For Operator Supervisor Maintenance | Enter the incorrect password and correct password to each access level. Check whether it is logging or not. Check each access level in similar fashion after log out from the current access level. | System should login only with correct password.
System should not login with incorrect password. |
Menu Screen | Press any of the command buttons on the screen and check whether that particular screen opens. | Particular screen should open irrespective of the current security level in which user has logged. |
Flow Diagram Screen | Try to set the PD Filter, PD Product and ATM Air Value | Operator will get a small popup screen to set the values. |
Process Parameter Screen | Change the m/c. parameters like min/ max and set point values and accordingly check the result of the process functioning | The machine will operate according to the set values. |
Alarm Screen | Click the alarm button from any screen | The alarm screen will activate. |
Machine Setting Screen | Try to Inflate the container | The container will inflate according to the given instruction |
Process Controls Screen | 1) Press Process ON 2) Press Heater ON 3) Press Spray ON/ | 1) The machine will start 2) The Heater will ON 3) The Spray will start. |
Power & Communication Failure Recovery Verification
Rationale –
To verify that in the event of a power loss or communications failure, the equipment /PLC will stop in safe condition and the operating parameter will not be lost or corrupted.
Test equipment – None Required.
Procedure for main power fail test –
- Operate the equipment in automatic mode or as directed in the User Manual.
- Record three of the configurable operating parameters in the main power fail test table of results (below).
- Record the displayed date and time in the main power & Communication fail test table of results (below).
- While the equipment/PLC is operating, shut down the power to the main control panel. Record if the equipment/PLC stops in a safe and secure condition.
- Wait for 3 minutes then restore power to the equipment/ PLC.
- Restart the equipment/ PLC. Record whether the equipment/PLC starts normally, and note any adverse condition.
- Verify that the parameters recorded in the step 2 are unchanged after the power failure.
- Record the displayed date and time after the power failure.
Acceptance criteria –
- At step 4, the equipment/PLC shall stop in safe and secure condition.
- At step 6, the equipment/PLC shall restart normally, with no problems or adverse conditions.
- At step 7, the configurable parameters remain unchanged and the date and time are correct.
Main Power and Communication Failure Test Results
Test | Results | |
Configurable Parameters before shut down.
| Parameter 1: _______________ Parameter 2: _______________ Parameter 3: _______________ | |
Main Power Shut Down | Equipment/PLC stops in a safe and secure condition. | |
Main Power Restored | Equipment/PLC can be restarted with NO problems or adverse conditions. | |
Configurable parameters after shut down. | Parameter 1: _______________ Parameter 2: _______________ Parameter 3: _______________ | |
Date and time as displayed | Before shut down: | After shut down: |
Emergency Operation Verification
Purpose – To deactivate the equipment in the event of an emergency stop.
Test equipment – None Required.
Procedure –
- With the emergency stop pressed in, try to cause movement of an operating function.
- With the equipment in operation, activate (press in) the emergency stop.
Acceptance Criteria –
- The equipment will be inoperative.
- The operation will ramp to a complete stop in four seconds or less.
Fail safe Results –
Emergency Stop | |||
Test | Acceptance Criteria | Meets Spec. (Yes / No) | Initial / Date |
With the emergency stop pressed in, try to cause movement of an operating function. | The equipment will be inoperative. | ||
With the equipment in operation, activate (press in) the emergency stop. | The operation will ramp to a complete stop in four seconds or less. |
Verification of Alarms.
Rationale – To verify alarms function and respond according to the system design.
Test equipment – None Required.
Procedure –
- Place the equipment into normal operation mode.
- Trigger each alarm outline in the table below.
- Verify that the specified alarm response is obtained and the correct alarm is displayed on the MMI Screen.
- Once the alarm has been activated, resolve the problem and reset.
- Verify that the equipment returns to normal operation mode.
Acceptance criteria –
- The alarms function and respond according to the system design.
Results: Verification of Alarms
Alarm Verification | ||
Simulation | Procedure | Excepted Result |
PD HEPA Inlet > MAX | Set the actual limit more than the set value | This alarm will generate and process will trip. |
Inlet Temp. > Maximum | Set the Inlet temp. max. value to lower than actual | This alarm will generate. |
Product Temp. < Minimum | Set the product temp. below the Min. level | This alarm will generate and process will stop. |
Exhaust Temp. > Maximum | Set the Exhaust temp. max. value to lower than actual | This alarm will generate and process will not start |
Earth Continuity Detected fault | Try to start the machine with improper earthing. | This alarm will generate and process will not start |
SFM Detected | Start the process without filter bag | This alarm will generate and process will not sop. |
Inlet Temp. < Minimum | Set the inlet temp. below the Min. level | This alarm will generate and process will stop. |
Exhaust Temp. < Minimum
| Set the exhaust temp. below the Min. level | This alarm will generate and process will stop. |
Container Not In Place | If the proxy sensor fails or its alignment mismatches it will give alarm | Machine will trip and flashes alarm. |
Blower Fan MPCB Electrical
| This alarm will generate only if the blower trips due to overload or over current. | This alarm will generate and the process will stop. |
Check Blower Star Delta
| Increase the star to delta conversion timing greater than 15 sec. | This alarm will generate and the process will stop. |
Ex. Flap Protection Active
| Change the position of the liver of limit switch above exkanal, during the process on condition | This alarm will generate and the process will trip. |
Exhaust Temp. > Set | Increase the exhaust set temp. below the actual value | This alarm will generate and process will stop |
Product Temp. > Set | Increase the set temp. above actual value | This alarm will generate and process will not start |
Batch Process Time End | When the set time matches with the actual process time. | This alarm will generate and process will stop. |
Container Seal Pressure Min. | During the process operation, drop the pressure of container seal. | This alarm will generate and trip the process. |
PD filter > Max | Set the PD filter max. value more than actual | This alarm will generate and process will not start |
Filter Seal pressure minimum | During the process operation, drop the pressure of filter seal. | This alarm will generate and trip the process. |
Check electrical control relay | This alarm will generate only if the there is any malfunction in electrical supply, due to overload or over current. | This alarm will generate and the process will stop. |
Operation Air Pressure Minimum | Drop the compressed air supply less then its minimum set point. | This alarm will generate, and machine will trip. |
Inflate filter seal first | Try to start the process without inflating the Filter Seal | This alarm will generate, and process does not start. |
Deflate container seal first | Try to deflate filter seal without deflating container seal. | This alarm will generate. |
Connect product temp probe | Start the process without connecting temperature probe. | This alarm will generate. |
Remove product temp probe | Deflate the container seal while temperature probe is in connected condition. | This alarm will generate. |
Remove product container bowl | Try to deflate filter seal while container not removed. | This alarm will generate. |
Filter in unlock position | Try to inflate filter seal while filter is in unlock position. | This alarm will generate. |
PD product > Max | Set the PD Product max. value more than actual | This alarm will generate and process will not start |
Deflate filter seal first | Press Filter change before deflating the filters. | This alarm will generate. |
SFM system failure | During machine operation switch OFF SFM power supply | This alarm will generate and machine will trip. |
Filter bag not in place | Try to inflate filter, while filter bag is not in its proper position. | This alarm will generate. |
Product Temp > Maximum | Set the Product temp. max. value to lower than actual | This alarm will generate. |
Operational Qualification Tests Status
The table below lists the tests performed and related results.
Critical Feature |
Testing of Programmable Logic Controller’s Processor |
Testing of Programmable Logic Controller’s Processor |
Verification of Man Machine Interface Screens – MMI |
Power & Emergency Failure Recovery Verification |
Emergency Operation Verification |
Verification of Alarms |
LIST OF STANDARD OPERATING PROCEDURES
Description | SOP No |
Operating Procedure of Fluid Bed Processor | |
Cleaning Procedure of Fluid Bed Processor | |
Preventive maintenance of Fluid Bed Processor |
7.0 Data Analysis , Summary of OQ & Recommendations
8.0 AMENDMENT RECORD – Any changes made in the system must be recorded in this sheet.