Your cart is currently empty!
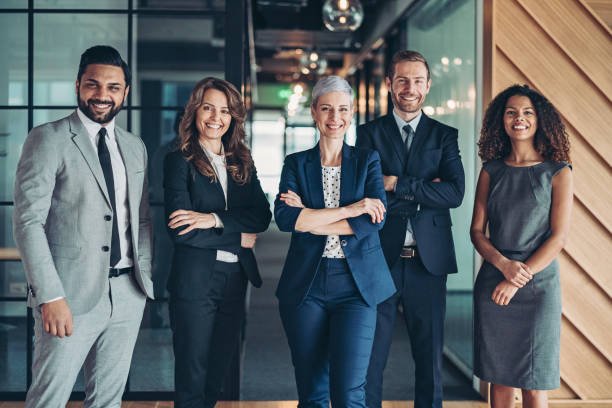
Deviation Management
Deviation Management
Deviation Management is a systematic approach used to identify, document, investigate, and resolve deviations from established quality standards or processes. These deviations can occur in various areas, such as manufacturing, testing, documentation, or supplier-related activities. The goal of deviation management is to identify the root cause, take appropriate corrective actions, and prevent the recurrence of similar deviations.
Objectives of deviation management:
- Ensuring Product Quality: Deviation management helps identify and resolve issues promptly, ensuring that products meet quality standards and specifications.
- Compliance with Regulations: Regulatory agencies, such as the FDA and EMA, require organizations to have a robust deviation management system to ensure compliance with industry regulations.
- Continuous Improvement: By analyzing deviations and their root causes, organizations can identify areas for improvement and enhance their processes.
Deviation Management Process
The Deviation Management process typically involves the following steps:
- Deviation Identification: Deviations are identified through various means, such as routine inspections, audits, testing, or employee reports.
- Deviation Documentation: All deviations are documented in detail, including the description of the deviation, its location, date, and initial impact assessment.
- Root Cause Analysis: A cross-functional team investigates the deviation to determine the root cause(s) behind the occurrence.
- Corrective Action Plan: Based on the root cause analysis, a plan for corrective actions is developed to address the deviation and prevent its recurrence.
- Implementation and Verification: The corrective actions are implemented, and their effectiveness is verified through follow-up assessments.
- Deviation Closure: Once the corrective actions are confirmed to be effective, the deviation is closed, and all relevant documentation is completed.
Effective Deviation Management
Implementing an effective deviation management system offers numerous benefits:
- Product Quality and Safety: Promptly addressing deviations ensures that products meet quality standards, reducing the risk of product recalls and adverse events.
- Regulatory Compliance: A robust deviation management system ensures compliance with regulatory requirements and guidelines.
- Improved Efficiency: Identifying and addressing deviations helps optimize processes, leading to increased operational efficiency.
- Continuous Improvement: Deviation management provides valuable insights into process weaknesses, contributing to a culture of continuous improvement.
Frequently Asked Questions (FAQ) on Deviation Management
Some common questions related to Implementing an effective deviation management system:
Q1: How are deviations identified in an organization?
Deviations can be identified through various means, such as internal audits, inspections, employee reports, customer complaints, or deviations identified during routine testing.
Q2: What is the difference between a deviation and a non-conformance?
A deviation refers to a departure from established standards or processes. A non-conformance, on the other hand, is a failure to meet specified requirements, such as product specifications or regulatory standards.
Q3: How is the root cause of a deviation determined?
The root cause of a deviation is determined through a comprehensive investigation, often involving techniques like the “5 Whys” or “Fishbone” analysis, to identify the underlying factors contributing to the deviation.
Q4: What is the role of the cross-functional team in deviation management?
The cross-functional team is responsible for investigating deviations, analyzing root causes, and developing appropriate corrective action plans. It typically includes representatives from relevant departments, such as quality, operations, and engineering.
Q5: How can an organization ensure that corrective actions are effective?
To ensure the effectiveness of corrective actions, organizations should monitor and measure the implementation of the actions and verify their impact through follow-up assessments and data analysis.
Conclusion
In conclusion, Deviation Management is a crucial aspect of quality management that ensures deviations from established standards or processes are identified, investigated, and resolved promptly. By implementing an effective deviation management system, organizations can improve product quality, regulatory compliance, and overall efficiency. Embracing deviation management helps organizations adapt to challenges and continually improve their operations.