Your cart is currently empty!
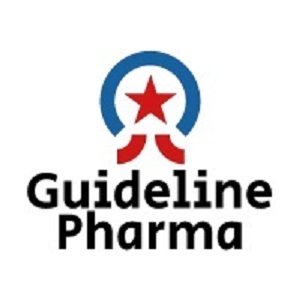
PREPARATION, CONTROL, ISSUANCE, REVIEW, RETRIEVAL, AND ARCHIVAL OF BATCH MANUFACTURING RECORD AND BATCH PACKING RECORD
PREPARATION, CONTROL, ISSUANCE, REVIEW, RETRIEVAL, AND ARCHIVAL OF BATCH MANUFACTURING RECORD AND BATCH PACKING RECORD
PURPOSE
To lay down a procedure for the preparation, control, issuance, review, retrieval, and archival of Batch Manufacturing Records (BMR) and Batch Packaging Records (BPR)
SCOPE
This SOP is applicable to describe the procedure for preparation, control, insurance, review, retrieval & archival of batch manufacturing records and batch packing records.
- BMR/BPR review Details
- Template for Master list of BMR/BPR
- Requisition for Issuance of BMR/BPR
- Issuance and retrieval record of BMR/BPR
- BMR/BPR Destruction Record
- BMR/BPR checklist
Batch Manufacturing Record:
A document used as a reference in pharmaceutical product manufacturing to monitor & processing the product as per defined instructions & record the manufacturing activities in the designated fields.
After completion of the manufacturing activities the appropriateness of product manufacturing is reviewed for assurance & release of the product.
Batch Packing Record:
A document used as a reference in pharmaceutical product packing to monitor & processing the product as per defined instructions & record the packing activities in the designated field.
After completion, batch packing activities & the appropriateness of the requirement of product packing are reviewed for assurance to release the product.
PROCEDURE:
Initiation and preparation of draft BMR/BPR.
Batch Manufacturing Record (BMR), which shall include manufacturing operation of dispensing, paste preparation, sugar preparation, mixing, milling, sifting, granulation, homogenization, Lubrication, blending, bulk preparation, compression, coating and Inspection, filling process, terminal sterilization, stirring, and autoclave.
Batch packing record (BPR) which shall include packing operation, filling & sealing, visual inspection, labeling, and stereo details, carton/foil/inserts (if any) details of the product, pet bottles, sachet, plastic drops, HDPE caps, LDPE granules, Vacuum leak test, Visual Inspection.
A batch Manufacturing Record (BMR) shall be prepared based on the process write-up/manufacturing instructions provided by the process development department or on the basis of information provided by the party regarding the manufacturing of that product or as per the approved Product Information form from CQA.
BMR is also prepared based on the Master Formula Record (MFR) of previous batches manufactured in any other plant and if a third party provided BMR same can be issued to the production department for manufacturing of the concerned product.
A batch Packaging Record shall be prepared on the basis of a Master Packaging Record (MPR).
After receipt of the Technology transfer document / Master Formula Record (MFR)/Product Development Report/Master Packaging Record from Formulation development, production personnel shall prepare the BMR / BPR.
The particulars to be mentioned in manufacturing records shall be as in Schedule – U of Drug and Cosmetic Rules 1945.
The production head/Designee shall check the BMR / BPR for the correctness of the content as per the technology transfer document / MFR.
After checking, Production Head/Designee shall put the signature in the relevant column and forward it to QA for review.
QA shall review the BMR / BPR and put the signature in the relevant column. After the final Draft copy forward it to Head-QA for review & comment.
The final draft copy after all amendments & recommendations shall take a final print copy for the Signature of all designated persons & final forward it to Head QA for approval.
On the approved copy, QA personnel shall put the ‘MASTER COPY’ stamp at the top left corner of each page in Red color.
Preparation of BMR/BPR Formats:
Each BMR & BPR shall have the following contents;
The font type and font size of the printed letters in the Header, Body, and Footer shall be Arial 11 Except for where bold text is required in case of headings or notes.
The header shall be repeated on each page of BMR/BPR Following the content in the header of BMR and BPR.
Content in BMR Header: Company Name, Document Name, Space for Issued copy stamp, BMR No., Product Code, Revision No. Effective Date, Product Name, Generic Name Batch size in kg., batch size in No., Batch No. supersedes no & Page no.
Content in BPR Header: Company Name, Document Name, Space for Issued copy stamp, BPR No., Product No, Revision No. Effective Date, Product Name, Generic Name, Standard Batch size, revised batch size. Batch No, supersede No, & Page No.
The footer shall also be repeated on each page of the BMR & BPR. Footer on the first page and remaining pages (i.e. prepared by, checked by, reviewed by, and approved by).
BMR shall contain the following information (Product Detail on the First Page):
Shelf Life
Mfg. Date & Exp. Date: Manufacturing date Month and Year in which the dispensing of the batch has started, & Expiry Month and Year, when the shelf life of the packed product finishes.
- Product Name
- Category
- Generic Name of the Product
- Label Claim of Product
- Change Control No
- Dosage Form
- Description
- Punch Dimension (In the case of Tablets)
- Average Weight/Average fill weight (Tablets/ Liquid)
- Storage condition
- Type of Marketed Domestic
- Master Formula No.
- Manufacturing License No.
- Issued By stamp & Sign.
Another Page in Header & Footer Different from per the First page in BMR.
Batch Processing or Manufacturing Detail
Master Formula (Bill of Material): mentioned the standard quantity of API & Excipients in mg per unit (Tablet/Liquid/ Oral Dry Powder/ SWFI) & in kg acceding to standard batch size.
Dispensing: In this part dispense the Raw material (API & Excipients) acceding to Master formulation or on Calculation of API assay basis.
Granulation/Manufacturing/Simulation: In this part, the following activity is performed Acceding to the product.
Tablet | Liquid | SWFI | Oral Dry Powder |
1. Line Clearance for the Granulation process | 1. Line Clearance for the Manufacturing process | 1. WFI Preparation (Distillation) | 1. Line Clearance for the Granulation process |
2. Shifting | 2. Verification of dispensed raw material | 2. Line clearance (simulation) | 2. Verification of dispensed raw material |
3. Binder Preparation | 3. Sugar Preparation | 3. WFI collection in WFI storage tank | 3. Sifting of material |
4. Dry mixing | 4. Bulk Preparation | 4. CIP & SIP of mfg. tank & FFS | 4. Sizing((Milling) |
5. Wet Mixing | 5. PH adjusts in Bulk Preparation | 5. Line clearance (mfg. area) | 5. Geometrical mixing |
6. Drying | 6. Volume makeup | 6. Batch Manufacturing | 6. Blending |
7. Sizing & Milling | —- | 7. Bulk Filtration through 0.22µ filter | 7. Reconciliation |
8. Slugging & Milling | —- | —- | —- |
9. Blending & Lubrication | —- | —- | —- |
10. Reconciliation | —- | —- | —- |
Compression: In this part, the following activity is performed Acceding to the product.
- Line Clearance for the Compression process
- In-house Specification
- In-process observation for Production & IPQA.
- Reconciliation
Coating: In this part, the following activity is performed Acceding to product ……
- Line Clearance coating material Dispensing
- Coating Material Dispensing Sheet
- Line Clearance for the coating process
- Coating process
- In-process observation for Production & IPQA.
- Reconciliation
Aseptic filling & sealing through FFS
Terminal Sterilization
Vacuum leak test of Ampoules
Release for packing (Oral Dry Powder/Liquid/Tablet/SWFI)
BPR shall contain the following information: (Product Detail on First Page)
Mfg Date & Exp. Date: Manufacturing date Month and Year in which the dispensing of the batch has started, & Expiry Month and Year, when the shelf life of the packed finishes product define as per stability studies/ Pharmacopeia.
- Generic Name of the Product
- Reference BMR No.
- Manufacturing License NO.
- Label Claim of Product:
- Shelf Life
- Dosage Form
- Change Control No
- Description
- Batch size & Revised B. size
- Yield (Standard & Actual Yield)
- Date of Commencement
- Date of completion
- Issued By stamp & Sign.
Another Page in Header & Footer Different from per Fist page in BPR.
Batch Processing or Packing Detail
General Instructions
Packing Specification
Standard Packing Instructions
Dispensing: In this part dispense the Packing material acceding to Master formulation.
Packing Process: In the packing process, the following activity performed Acceding to the product
- Instructions
- Line Clearance
- Verification of tablet/Liquid/Oral Dry powder/LDPE Granules received from the core area
- Stereo detail,
- Batch Over printing detail (blister/ strip, inner carton, outer carton, shipper, bottle label/Ampoules label)
- Blistering/Striping/Bottle filling/Sachet/Pouch Packing (Machine Setting)
- Blister/Strip/Bottle/Pouch packing Start-up control check
- Secondary and tertiary packing
In-process check by production & IPQA
Shipper weighting record
Reconciliation of packing material
Finished product sampling and Quality Control Approval
Finished goods transferred to FG store
Batch Reconciliation
Review of BPR
Dispatch Details
Each processing operation shall be written in the form of specific instructions, in a tabular form. Adequate space shall be provided for the manual recording of time and quantities used along with the doer & checker signatures, against each processing instruction.
The critical processing steps or Critical control parameters shall be identified/highlighted in the BMR/BPR. Each of these critical processing steps shall have a standard time/temperature etc. mentioned in the BMR/BPR.
Each critical control parameter shall have the doer and checker signature.
Against each operation, the operator shall put his / her initials. Therefore, appropriate space shall be provided for the signatures, against each operation.
“Precautions/cautions/note” shall be typed in ‘bold’ in the remarks column, if required.
The reference to relevant SOPs shall be made wherever necessary.
Each BMR shall be checked & reviewed by the production in charge and handed over to QA, after the completion of the batch manufacturing activities.
Review of BMR/BPR
Production Officer and above shall prepare a draft of the Master BMR/BPR and forward it to the Quality Assurance department for review.
The Quality Assurance shall review the draft copy of BMR/BPR/MFR/MPR to verify the Critical process/control parameters, sequence of activities, instructions, cautions, etc.
If the Quality Assurance shall is satisfied with the draft copy of BMR/BPR/MFR/MPR then the production head /designee shall take the final print copy and sign off BMR/BPR and send it to BMR/BPR to QA for final approval.
MFR/MPR is prepared first time by R&D and later by Production and approved by the quality assurance head.
Numbering of Master BMR/BPR
Once the QA executive and above have received & reviewed the draft BMR, a unique master BMR/BPR number shall be assigned to each master batch record.
Master BMR numbering system for Individual batches shall consist of the following characters:
Document code/Product code/version No.
Where
Document code = BMR/BPR or OBMR/OBPR (For Optimization Batch)
Product code =
Version No = 00
Approval of BMR/BPR
QA-Head shall finally Approve the BMR & BPR by signing off the batch record, after being satisfied with the same in all respects.
Once the batch record has been approved by QA-Head, the QA assistant and above shall stamp the same as “Master Copy” with the sign & date at the top left of the header of each page.
Control of Master Copy of Batch Manufacturing Records.
The approved Master copy of BMR/BPR shall remain in QA custody.
A photocopy of the BMR shall be issued to production, for manufacturing of a new batch of particular product.
A list of the entire master BMR/BPR shall be maintained by QA.
Issuance of BMR/BPR
The approved master copy along with the corresponding soft copy shall remain with the QA department.
The production chemist/officer shall raise the requisition for the issuance of BMR/BPR.
After taking approval from the respective head, the requisition shall be sent to QA for the issuance of BMR/BPR.
QA-Assistant and above shall receive the requisition and review it.
QA-Assistant and above shall assure the required number of photocopies of BMR/BPR from the master copy and check the correct sequence of page numbers.
QA personnel shall check and ensure the coverage of all pages, and legibility of the contents therein as per the master copy.
QA personnel shall put the “QA” stamp on the front page in the given box and put the “QA” Stamp in Green color on the right corner on each subsequent page, issued digitally through Adobe software.
In case Adobe software is not working temporally QA personnel shall put the ‘ISSUED COPY’ stamp on the front page in a given box with the signature and date and the right corner on each in subsequent page in green color for issuance of BMR/BPR in the relevant column.
QA personnel shall put the batch number on each page of BMR/BPR, as per requisition either manually or through scan copy of BMR/BPR with the software on each page.
After the handover of BMR/BPR to Production personnel, Production personnel shall sign in Issuance and Retrieval record.
Issuance and Retrieval Record of BMR/BPR from production and maintenance recorded by QA.
In case of production, the plan is canceled for any valid reason production shall return the BMR/BPR to QA and QA-Officer/Executive, and above shall mention remark as batch canceled.
In case the copy once issued to production is damaged, Production personnel shall put the request for an extra copy of BMR / BPR with proper justification and approval request to Head QA.
If the Justification is found valid and genuine the issued copy shall be retrieved by QA and the same BMR/BPR shall be issued against the justification request on the current date and entries shall be copied the same as in the previously issued copy and the retrieved damaged copy shall be preserved with a rewritten issued copy once the completion of manufacturing product after batch release.
The user shall fill in the same data as filled in the previous BMR/BPR and sign off on the same date by the same person as in the previously issued copy.
After consultation with head-QA, QA personnel shall issue an Additional copy of BMR/BPR as per requisition and also retain the damaged copy as per the submitted justification as proof.
Retrieval of BMR/BPR
Production personnel shall fill the BMR/BPR online as per the steps specified and complete the BMR/BPR.
The completed BMR/BPR shall be checked for completeness and correctness of content and shall sign by competent technical production personnel.
Completed BMR/BPR shall be submitted to QA before releasing the batch.
After submission of BMR/BPR to the QA department, production, and QA personnel shall sign in the relevant columns in the BMR/BPR record register.
QA-Officer/executive shall receive the BMR/BPR and maintain the record.
Review of BMR/BPR
Area / environmental monitoring records shall be available.
BOM for the quantity of raw material and Identification Lot No.
Correct and release (by QC) raw materials/intermediates/packaging components used in manufacturing.
Correct quantities of all ingredients are used in manufacturing.
All dispensing tags of Raw Materials/Packing materials are attached with BMR/BPR.
The equipment Identification number is mentioned at the appropriate place of operation.
Rinse water/swab sample analysis reports attached with BMR/BPR (if applicable).
All significant steps of the process are signed and dated by the doer & checker.
In-process checks are performed at a defined frequency and recorded at the appropriate place in BMR/BPR.
The results of In-process checks are within the limit.
Quality control samples are withdrawn at the appropriate stage and QC analysis results are within the limit and report of analysis attached with BMR/BPR.
Date and time of commencement and completion of different stages, in a logical sequential manner.
The batch processing record is complete with respect to yield norms/reconciliation and is signed.
Deviation (if any) recorded and approved.
Signed specimens of all packing material used during packing are attached with BPR.
Finished product sample/control samples are withdrawn and recorded in BPR.
The finished goods transfer note is attached to the BPR and verified by QA.
QA-Officer/executive and above shall review the BMR/BPR for the correctness of the quantity of RM/PM used, proper filling of BMR/BPR with sign and date, yield reconciliation, etc., and observation.
Final archival of the BMR/BPR
After final review and batch release assistant QA and above shall place the BMR/BPR in the document room.
Retention and disposition of BMR / BPR
The completed batch records shall be archived in QA with proper care.
The completed batch records shall be retained by QA for at least one year after the expiry date of the batch.
After completion of the retention period batch records shall be disposed off by shredding and destruction records shall be maintained
BPR/BMR shall be destructed after one year of the expiry date of that product and the record shall be maintained.
Validation/ Performance Qualification/re-validation/re-qualification BMR/BPR/ Stability batches shall be retained permanently.
Preparation, Issuance, retrieval & retention period of Optimization Batch Record.
Optimization BMR & BPR shall be prepared and Issuance and retrieval records shall be maintained.
Optimization batches record shall be retained permanently.