Your cart is currently empty!
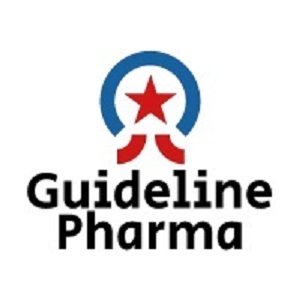
REPORTING OF DEVIATION
REPORTING OF DEVIATION
All deviations must be reported immediately on the day of discovery, but not later than the end of the next working day, and logged within the same day or the end of the next working day but not later than.
Deviation shall be initiated in the following circumstances but not limited to
- Processing deviations that have affected or potentially could affect a
- A general system breakdown or failure to follow
- An action limit is
- A value is outside the processing
At the discretion of the QA department, when there are excessive minor errors and/or recording errors. Errors that are found and corrected by manufacturing; however, are repetitive.
When BMRs are reviewed for product release, QA may issue a deviation report based on the information (or lack of required information) recorded in the BMRs/ Records.
A single deviation report may be used for more than one lot/batch if the deviation was repeated and the cause for the deviations is mutually related.
After initiating a deviation, the initiator can cancel the deviation if required. The cancellation shall be supported by justification and submitted to QA prior to the closure of deviation.
Any person (Initiator) can identify an incident or deviation and shall initiate an incident or deviation record. It shall be reported to the supervisor immediately and documented in the system on the day of discovery, but not later than the end of the next working day.
A unique identification number shall be assigned to the record. Quality Assurance shall be informed within one working day of discovery of the incident or deviation.
The concerned department person shall immediately initiate the issuance of deviation report from QA through “Documents/format requisition”.
QA person shall issue a deviation report as per Attachment-I (AK/QAD-006/F01) and allocate the deviation number serially as XX/DRNY/ZZZ
Where,
- XX: Plant code for example (AK for Relax Pharmaceuticals Pvt. Ltd. Unit-1)
- DR: Deviation report
- VY: Indicates the last two digits of the current year (23 for the Year 2023)
- ZZZ: Serial number of the deviations starting from 001
Record of deviation shall be maintained by QA in the format.
If the devIatIon Is related to environmental condItIon, the concerned dept. shall notify the same as per the respective SOP for immediate action. Simultaneously, the concerned department shall also fill deviation reports.
For activity related to the calibration of the QC instrument, if the instrument goes out of calibration, the QC department shall fill in the deviation and carry out the investigation as per the respective SOP.
The Initiator shall provide the following information, but not limited to, as applicable:
The initiator shall fill in the detail required in Part-I: Initiation of Deviation (Deviation Report) with identifier/initiator name & sign/date further points filled by the concerned HOD along with task list, immediate action, and description of immediate action based on initial assessment and reviewed by QA.
Part-I of the deviation report shall be completed on the day of discovery, but not later than the end of the next working day, and shall be logged within the same day or end of the next working day but not later than.
Consent Review and Assessment of Deviation (PART-II)
- Sections 1 & 2.2 shall fill and reviewed by QA.
- Section 2.3 shall fill by impacting department and recommendation along with the target date of completion.
- Section 2.4 shall fill by QA based on the review and approval required by External Agency/MAH QP.
- Section 2.5 shall fill by QA based on the review and approval required by the Customer.
QA shall evaluate the history of deviation regarding the first occurrence or recurrence of such or a similar kind of deviation.
Based on the history, the QA shall categorize the deviation as Critical/Major/Minor and provide the rationale for the re-categorization of deviation. Category of deviation may be subjected to change due to (but not limited to) consecutive failure, recurrence, or based on potential impact, risk on system/activity/process/formula.
If the deviation is repeated, QA shall specify the deviation number and its status..
deviation form shall fill by the head QA shall categorize the deviation by tick mark ( ) on Critical/Major/Minor followed by Approval of deviation or rejected. In case of rejection of deviation form, justification and recommendation of deviation required and based on evaluation, tick mark ( ) in the given box for investigation required or not followed by tick mark ( ) on the given box (Yes or No) for impact assessment and risk assessment.
Quality Risk Management (QRM) is required for critical and major deviations which directly impact or risk associated with the quality, safety, efficacy, and purity of drug product/facility/GxP activity.
The target completion date for different category deviations shall be as follows:
- For Minor deviation, TCD shall be within 30 days from the date of initiation.
- For Major deviation, TCD shall be within 15 days from the date of initiation.
- For Critical deviation, TCD shall be within 7 days from the date of
Root Cause, Action Plan Review (PAR1 Ill)
shall fill by the concerned HOD with action to be addressed through reference CAPA number (if applicable).
shall fill by the concerned HOD with a description of the action, the responsible person to complete the action, the closing date of action taken, the status of action (whether open/closed), and an attachment for evidence of action taken and completion.
Followed by a QA review. If the action plan required is not closed within define timeline then TCD (Target completion date) shall be taken to QA for completion of action/activity by filling the “Deviation TCD Extension form”
Root Cause shall be identified as per SOP on Investigations or Root cause shall include the detail of the investigation, tools used for investigation, and finding and conclusion of investigation reflecting the main cause of event/deviation.
The concerned department shall follow SOP on Corrective Action and Preventive Action (CAPA) to address the preventive action to avoid the recurrence of the same or similar failure or deviation.
Mention reference CAPA number, description of the action, responsibility, status, and any attachment including closing date/target date of completion (TCD).
The investigation and action plan shall be reviewed by QA and approved by the head of QA.
Monitoring, Follow-up, and Closure: Part-IV
The timeline for the closure of deviation shall be different for each category of deviation with CAPA. In case of an investigation or CAPA is not completed within the stipulated time, an extension for timelines can be requested with proper justification i.e. action plan to complete the job, target date of completion, responsible person. Maximum 02 extensions shall be allowed, and extension to be requested and justified by the concerned head of the department and approved by QA Head/ Quality Head or by senior management, if applicable.
The proposed target date of completion for two extensions shall not be more than 90 working days.
If any action requires more than 90 working days then deviation shall be closed mentioning the CAPA reference number and activity to be addressed or monitored with the respective CAPA.
In the case of civil work/Project work related to facility modification may go beyond 90 days. In such cases, CAPA shall remain open with the justification of work beyond the timeline. In that case, the timeline shall depend on work expedite.
Ensure to report the deviation reference in respective batch documents or activity documents, if applicable.
Ensure completeness of deviation form with attachments as the list of documents.
After completion of verification of all documents and action taken, conclude whether the deviation is to be closed satisfactorily.
A concerned person along with QA shall verify the completion of the proposed action as defined in the action plan.
Closure of deviation shall be done by QA Head/designee.
In case of extension of deviation PART-IV monitoring, follow up and closure
shall not close within the defined time line, an extension of deviation shall be filled by the user department or concerned responsible person extension and proposed extended TCD for further date of closure of deviation form.
Extension Approval status (Yes/No) shall give by Head QA based on justification of extension by the user department or concerned person/HODs.
Only two (02) extension of deviation are allowed and deviation can be extended up to a maximum of 90 working days If the deviation is not closed within 90 working days and remain in the open state, then close the deviation with the CAPA number and the same CAPA number as reference shall give to new deviation form raise for same event/subject or further extension of time line beyond 90 working days.
Trending:
Deviation trend shall be prepared by QA
While defining the criteria for trending of deviation data, the below-mentioned approach is to be followed:-
- Open versus close deviation
- Recurrence of deviation
- Category-wise review of deviation -Minor/ Major/Critical
Root cause/source-wise review of deviation
Due to malfunctioning of equipment/ instrument.
Due to human error e.g. failure to follow procedure, negligence, lack of knowledge, attention, etc.
Procedural deficiency etc.
For trending of the deviations prepare the following graphs:
- Time duration v/s is a number of deviations, with time on the X-axis and a number of deviations on the Y-axis.
- The frequency of deviation trending shall be
- If more than one batch is affected, a reference photocopy of the deviation shall be attached with each remaining batch record.
- The site technical team (QA Head/ Quality Head, QC Head, Production Head, Engineering Head, or as nominated by QA Head/ Quality Head and concerned department head) shall review the deviations and relevant CAPA in order to identify and evaluate its effectiveness to avoid recurrence of same or similar failure/case.
- The Deviation Analysis shall be part of the Product Quality Review and Management Review.